Chemical and Process Engineering Resources
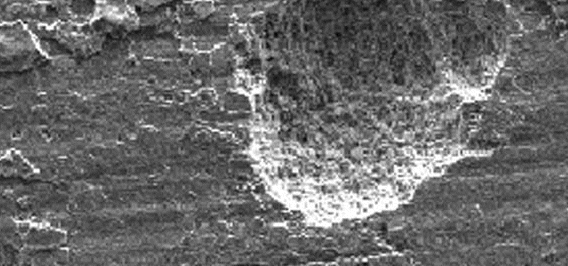
Corrosion is costly! If you doubt this, then you probably have never been bitten by the "corrosion bug". Imagine specifying Titanium for 10 brand new heat exchangers or reactors and later realizing that the processing stream has fairly high concentrations of flourine ions.
The Titanium will be destroyed in weeks and you'll have wasted hundreds of thousands of dollars. There you stand in front of your supervisor, you'll get that sick feeling in your stomach....that's the "corrosion bug"! I'd like to think that things like this don't happen, but I've heard my share of horror stories.
If you'd like to avoid a situation like this, I've got two words for you.....FLUID ANALYSIS. A fluid analysis can save you pain, embarassment, and in some cases your job. But if you think about, there' really no excuse for not having one done considering the impact that a material of construction decision can have. With this in mind, I thought that it may be a good idea to review some of the most basic forms of corrosion.
Uniform attack is a form of electrochemical corrosion that occurs with equal intensity of the entire surface of the metal. Iron rusts when exposed to air and water, and silver tarnishes due to exposure to air. Pontentially very risky, this type of corrosion is very easy to predict and is usually associated with "common sense" when making material decisions.
Galvanic corrosion is a little more difficult to keep track of in the industrial world. You'll notice below that simply adding a screw of the wrong material can have severe consequences. Galvanic corrosion occurs when two metals having different composition are electrically coupled in the presence of an electrolyte. The more reactive metal will experience severe corrosion while the more noble metal will be quite well protected. Perhaps the most infamous examples of this type of corrosion are combinations such as steel and brass or copper and steel. Typically the steel will corrode the area near the brass or copper, even in a water environment and especially in a seawater environment. Probably the most common way of avoiding galvanic corrosion is to electrically attach a third, anodic metal to the other two. This is referred to as cathodic protection.
Another form of electrochemical corrosion is crevice corrosion. Crevice corrosion is a consequence of concentration differences of ions or dissolved gases in an electrolytic solution. A solution became trapped between a pipe and the flange on the left. The stagnant liquid in the crevice eventually had a lowered dissolved oxygen concentration and crevice corrosion took over and destroyed the flange. In the absence of oxygen, the metal and/or it's passive layer begin to oxidize. To prevent crevice corrosion, one should use welds rather than rivets or bolted joints whenever possible. Also consider nonabsorbing gaskets. Remove accumulated deposits frequently and design containment vessels to avoid stagnant areas as much as possible.
Pitting, just as it sounds, is used to describe the formation of small pits on the surface of a metal or alloy. Pitting is suspected to occur in much the same way crevice corrosion does, but on a flat surface. A small imperfection in the metal is thought to begin the process, then a "snowball" effect takes place. Pitting can go on undetected for extended periods of time, until a failure occurs. A textbook example of pitting would be to subject stainless steel to a chloride containing stream such as seawater. Pitting would overrun the stainless steel in a matter of weeks due to it's very poor resistance to chlorides, which are notorious for their ability to initiate pitting corrosion. Alloy blends with more than 2% Molybdenum show better resistance to pitting attack. Titanium is usually the material of choice if chlorides are the main corrosion concern. (Pd stabilized forms of Ti are also used for more extreme cases).
The Titanium will be destroyed in weeks and you'll have wasted hundreds of thousands of dollars. There you stand in front of your supervisor, you'll get that sick feeling in your stomach....that's the "corrosion bug"! I'd like to think that things like this don't happen, but I've heard my share of horror stories.
Uniform Attack
Uniform attack is a form of electrochemical corrosion that occurs with equal intensity of the entire surface of the metal. Iron rusts when exposed to air and water, and silver tarnishes due to exposure to air. Pontentially very risky, this type of corrosion is very easy to predict and is usually associated with "common sense" when making material decisions.
![]() |
Figure 1: Uniform Corrosion Attack |
Galvanic Corrosion
Galvanic corrosion is a little more difficult to keep track of in the industrial world. You'll notice below that simply adding a screw of the wrong material can have severe consequences. Galvanic corrosion occurs when two metals having different composition are electrically coupled in the presence of an electrolyte. The more reactive metal will experience severe corrosion while the more noble metal will be quite well protected. Perhaps the most infamous examples of this type of corrosion are combinations such as steel and brass or copper and steel. Typically the steel will corrode the area near the brass or copper, even in a water environment and especially in a seawater environment. Probably the most common way of avoiding galvanic corrosion is to electrically attach a third, anodic metal to the other two. This is referred to as cathodic protection.
![]() |
Figure 2: Galvanic Corrosion |
Crevice Corrosion
Another form of electrochemical corrosion is crevice corrosion. Crevice corrosion is a consequence of concentration differences of ions or dissolved gases in an electrolytic solution. A solution became trapped between a pipe and the flange on the left. The stagnant liquid in the crevice eventually had a lowered dissolved oxygen concentration and crevice corrosion took over and destroyed the flange. In the absence of oxygen, the metal and/or it's passive layer begin to oxidize. To prevent crevice corrosion, one should use welds rather than rivets or bolted joints whenever possible. Also consider nonabsorbing gaskets. Remove accumulated deposits frequently and design containment vessels to avoid stagnant areas as much as possible.
![]() |
Figure 3: Crevice Corrosion |
Pitting
Pitting, just as it sounds, is used to describe the formation of small pits on the surface of a metal or alloy. Pitting is suspected to occur in much the same way crevice corrosion does, but on a flat surface. A small imperfection in the metal is thought to begin the process, then a "snowball" effect takes place. Pitting can go on undetected for extended periods of time, until a failure occurs. A textbook example of pitting would be to subject stainless steel to a chloride containing stream such as seawater. Pitting would overrun the stainless steel in a matter of weeks due to it's very poor resistance to chlorides, which are notorious for their ability to initiate pitting corrosion. Alloy blends with more than 2% Molybdenum show better resistance to pitting attack. Titanium is usually the material of choice if chlorides are the main corrosion concern. (Pd stabilized forms of Ti are also used for more extreme cases).
![]() |
Figure 4: Pitting Corrosion |
2 Comments
Thank you for good basic summary. Easily understood.
such an informative article.