Gas Flotation is one of the oldest methods for removal of solids, oil & grease and fibrous materials from waste water. It is part of the primary treatment of waste water. Removal efficiencies can be as high as 99%+ for suspended solids and oil and grease. Gas flotation is simply the process of generating microscopic gas bubbles in the container (tank / vessel) holding the waste water which enhances the tendency of the suspended solids / oil and grease to float up to the surface of the tank / vessel for further removal by mechanical skimming.
Please note that I have used the terminology "gas flotation" instead of "air flotation" which is very commonly used in literature because air as a gaseous media is most commonly used for municipal waste water treatment and in applications where there is no risk of forming a flammable or explosive mixture with the dissolved gases in the water. In the upstream oil and gas industry, due to the inherent risk of forming a flammable / explosive mixture with air, other gaseous media are used such as natural gas or nitrogen.
The gas flotation process is again categorized as the "Dissolved Gas Flotation" (DGF) and "Induced Gas Flotation" (IGF) process. Essentially both produce gas bubbles to enhance the flotation process but there are major differences in the way gas bubbles are produced and the efficacy of these processes.
Let us understand the process of DGF. In a DGF system air is dissolved in the water to be treated by passing the water through a pressurizing pump, introducing air, and holding the air-water mixture at high pressure long enough for the water to be saturated with air at the high pressure. Typical pressures are 1.5 to 5 barg. After saturating the water with air at high pressure, the mixed air-water stream plus the influent water are released at a lower pressure through a pressure-reducing nozzle in the flotation chamber where air precipitates as very tiny bubbles. DGF process can produce bubbles of the range of 50-100 microns. These small bubbles are the key for the enhanced removal of solids / oil and grease by flotation to the top of the flotation chamber. The smaller bubbles have much more surface area for their volume than do the larger bubbles. A particular volume of air has ten times the surface area when distributed as 50 micron bubbles as it does when distributed as 500 micron bubbles. Put another way, you need 10 times the air flow with 500 micron bubbles as you need with 50 micron bubbles in order to achieve the same air-water interfacial area.
The IGF is a variation of the DGF process. It involves inducing the gas into the total stream either by the use of an inductor device (referred to as the hydraulic type) or by a vortex set up by mechanical rotors (referred to as the mechanical type). For a hydraulic type, water from the effluent is pumped to a recirculation header that feeds a series of venturi eductors. Water flowing throught the eductor sucks gas from the vapor space that is released at the nozzle as a jet of small bubbles. The bubbles rise causing flocculation in the flotation chambers forming a froth that is skimmed with a mechanical skimmer. The mechanical type, by using a a rotating shaft and impeller, creates a vortex and a negative pressure, which draws the gas down the stand pipe entraining it in the water forcing the gas rich water throughout the chamber. Once in the chamber the gas is released as fine bubbles and lifts the oil and the suspended solids to the surface. The froth is than skimmed by a mechanical skimmer.
The DGF system has distinct advantages over the IGF system. Let us list down some of these:
1. DGF provides finer bubbles in comparison to IGF thereby increasing oil and suspended solid removal efficiency.
2. DGF requires a lower installed power requirement than an IGF.
3. DGF operating and maintenance cost is lower than IGF.
4. DGF overall efficiency and performance are higher than for a comparble IGF system.
5. Since flotation processes are enhanced by addition of flocculation chemicals, for a DGF unit the requirement for chemical additives is lower than for a comparable IGF unit.
IGF systems are getting outdated. Most of the new gas flotation units are of the DGF type.
Some excellent references are available freely on the internet and here are their links:
http://en.wikipedia....d_air_flotation
http://en.citizendiu...d_gas_flotation
A spreadsheet for DAF sizing by Hydro-Flo Technologies can be downloaded from:
http://www.dissolved...alculations.htm
Not to forget the reference that I have used for some of the description above is the excellent book
"Handbook of Water and Wastewater Treatment Technologies" by "Nicholas P. Cheremisinoff".
Also refer the image below which basically provides sketches for two different variants of the DGF using air as the gaseous media.
Would love to hear comments form the esteemed forum members and readers.
Regards,
Ankur.
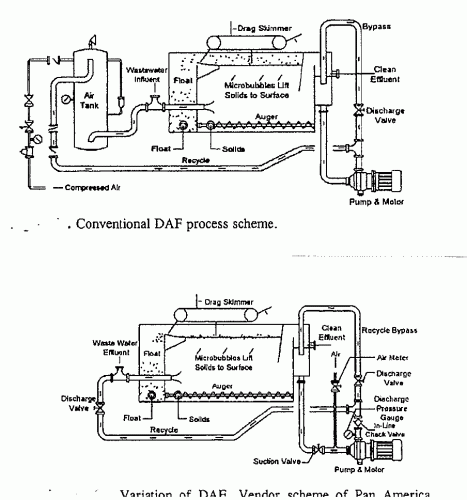
- especially concerning use of Gas(es) other than air.
- Although Previously "D.A.F." was the final (sort of) finishing treatment considered.
Regards