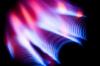
The purpose of today's blog entry is to provide a brief description of the most common methods for heavy hydrocarbon recovery from natural gas and what these methods are capable and their limitations:
The most common methods employed for hydrocarbon recovery in Gas processing plants are as follows:
1. Mechanical Refrigeration plants (using propane for refrigerant)
2. Lean Oil Absorption Plants / Refrigerated Lean Oil Absorption Plants
3. Turboexpander plants
Let us understand the application and / or limitation of each of these methods:
1. Mechanical Refrigeration Plants:
If the major purpose of a plant is to condition rich gas to meet certain pipeline specifications, the mechanical refrigeration plant may be the proper selection. Refrigeration is used to condition produced gas to meet pipeline hydrocarbon (HC) dew point specification, heating value specification, limited gas liquids recovery of heavier hydrocarbons such as C5+, or a combination of these objectives. The straight refrigeration plant is limited to chilling the gas stream to the range of -34°C (-29°F) to -40°C (-40°F). This limits product recovery to about 60 percent of the propane content at typical plant operating pressure
2. Lean Oil Absorption Plants:
The most efficient lean oil absorption plants recover only about 40 percent of the ethane, 90 percent of the propane, and 100 percent of the butane and heavier hydrocarbons from the gas. Additional heat is required to separate the products from the lean oil, and additional cooling is required in order to reliquify the raw products before fractionation. Lean oil absorption plants usually have higher operating costs than either refrigeration plants or turboexpander plants.
3. Turboexpander Plants:
Turboexpander plants can recover from 60 to 90 percent of the ethane, 90 to 98 percent of the propane, and 100 percent of the butane and heavier hydrocarbons from the gas. These plants are compact and relatively simple to install and operate, if designed properly. The inlet gas to a turboexpander plant must have essentially all of the water removed (to 1 ppm or less) to prevent hydrate formation. Turboexpander plants have less process equipment (towers and external heating) than lean oil absorption plants, but they have more mechanical equipment (gas exchangers and re-compressors). If ethane recovery is the objective, the expander process is the most economical means for recovering a high percentage of ethane and heavier hydrocarbons from a gas stream.
The above mentioned guidelines are very general in nature and there can be specific instances where a particular method with certain adaptations may be more suitable for a particular heavy hydrocarbon recovery in contradiction to the guidelines provided above. Many technology licensors today are providing state-of-the-art technology for selective and optimum heavy hydrocarbon recovery from natural gas and readers of this blog entry are well advised to search for more efficient and economical methods offered by some of these technology licensors.
A flow scheme for a turboexpander and refrigeration plant is provided as an attachment,
Readers are also advised to read through the chapter titled:
Section 16, Hydrocarbon Recovery, GPSA Engineering Databook, 11th Edition (SI units)
Looking forward to comments from the readers of "Cheresources".
Regards,
Ankur,
Thank you.