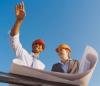
Today's blog entry is specifically targeted for new chemical engineers joining the engineering design and consulting field as freshers. Without further ado, let's get on with what IDC is all about.
An engineering design and consulting firm engaged in providing consultancy services in the chemical process industry is a multi-disciplinary organization. Typically the engineering disciplines that exist in an engineering design and consulting firm are "Process Engineering", "HSE Engineering","Piping Engineering", "Instrumentation Engineering", Mechanical Engineeering","Electrical Engineering", "Civil Engineering" "Project Engineering" and "Quality Assurance (QA)". Some companies may have even more such as "Telecommunications Engineering", "Costing Engineering" etc.
All the aforementioned disciplines prepare engineeering documents and deliverables during the execution of a project. However, it is important to remember that most projects are multi-disciplinary in nature, with a few exceptions. It means that drawings, documents, calculations are required from all disciplines for completion of the engineering activity. In a nutshell, the complete engineering package of any project comprises items from all disciplines.
When working for a project in a multi-disciplinary environment, drawings, documents and deliverable for all disciplines become to a great extent a joint or co-ordinated effort of all disciplines. Remember, the start point or initiation of any project is from the process engineering group. No wonder, good process engineers are prized possessions of any engineering consulting company.
The process of IDC is basically an activity which ensures the following:
1. Creating complete awareness about the project for the assigned multi-disciplinary team
2. Ensuring all critical documents / drawings / calculations are reviewed, marked and corrected as required by the multi-disciplinary team for correct inputs, removal of errors and ensuring that the project quality plan is folllowed for producing first-class project deliverables
3. Ensuring information flowing periodically during the project execution phase, for example vendor data, design review(s) / HAZOP is captured in the engineering deliverables, to bring these deliverables up to the level of being useful for the construction of the plant.
Since I am a process engineer, I will be talking more about process engineering in context to IDC. The engineering documents / drawings that a process engineering team prepares and that need an IDC from other disciplines are typically listed below:
a. PFDs (need IDC only from Instrumentation and QA and that too if PFD represents control logic)
b. Project Design Basis (Instrumentation, Piping, Mechanical, Electrical, HSE, Civil, Projects, QA)
c. P&IDs (IDC from Piping, Instrumentation, Mechanical, Electrical, HSE, Projects, QA, Civil)
d. Equipment Process Datasheets (Mechanical, Instrumentation, Electrical, Piping, QA)
e. Instrument Process Datasheets (Instrumentation, Piping, Electrical, QA)
f. Hazardous Area Classification Drawings prepared by Process / HSE (Electrical, Instrumentation, Mechanical, Piping. QA)
g. Operating, Control and Safeguarding Philosophy (Instrumentation, Mechanical, Piping, QA)
h. Pre-commissioning and Commissioning Procedures (Mechanical, Instrumentation, HSE, Piping, QA)
i. Plant Operating Manual (Instrumentation, Mechanical, HSE, Electrical, Piping, QA)
j. Design Review and Closeout Report (Instrumentation, Mechanical, HSE, Piping, Electrical, Projects, QA)
k. HAZOP Review and Closeout Report (HSE, Instrumentation, Mechanical, Piping, Electrical, Projects, QA)
The aforementioned deliverables are just a few of the important process/HSE deliverables that need an IDC. There can be many more and some of them could also be project specific.
Some of the deliverables from other disiplines that need IDC from process are:
1. Mechanical Material Requisitions or specifications
2. Instrument Material Requistions or specifications
3. Electrical Load List prepared by Electrical
4. Equipment (Static / Rotating / Package) Vendor Data
5. Instrument Vendor Data
6. Piping Material Requisitions or specifications
7. Pipe / Valve / special in-line fittings Vendor Data
A process engineer certainly does not need to do an IDC for a transformer or sub-station specification. A process engineer certainly does not require to do an IDC of civil foundation drawings and structural piles. Similarly, there is absolutely no sense of a process engineer reviewing an electrical single-line diagram or instrument loop drawings. It doesn't make sense for a process engineer to review cable schedules. What I am trying to say is that, there should be some analysis of what deliverable requires an IDC and from whom. Generally good engineering companies have an IDC matrix which specifies the discipline-wise individual deliverable which requires an IDC and from whom.
Well, I think I have written enough for a blog entry and I would be happy to entertain questions from the readers and members of "Cheresources" regarding IDC. In fact, I look forward to some queries from the young engineers who have just started their career in engineering consulting.
Regards,
Ankur.
Very good explanation. We are also following IDC metrix in our organization.
This is a very good tool for improve quality of document with minimum error.
I feel that follwing deliverable also required IDC from process on & above you had explain.
- Equipment layout from piping
- Piping GA from piping\
- Alram & trip schedule form instrumentation
Regards,