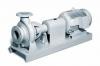
One of the foremost rotating machinery and reliablity specialist of our times is Heinz P. Bloch with numerous books, articles and research papers on rotating machinery and machine reliability. His fame as a machinery specialist is such that Wikipedia has an article on him. Refer the link below:
http://en.wikipedia..../Heinz_P._Bloch
The comparison that I am providing is referenced from his book "Pump User's Handbook Life Extension" co-authored with Allan R. Budris
ANSI vs API
Compared to an API pump, the typical ANSI pump has the following characteristics:
1. A thinner casing, i.e. less corrosion allowance
2. An ANSI pump has reduced permissible nozzle loads. It is even more sensitive to pipe-induced stresses than the API pump.
3. An ANSI pump has a smaller stuffing box size. Unless a large bore option is chosen, an ANSI pump may not be able to accomodate the optimum mechanical seal for a given service.
4. ANSI pump impellers are designed and manufactured without wear rings. Many ANSI pump impellers are open or semi-open whereas API pumps feature closed impellers with replaceable wear rings.
5. ANSI pumps are generally foot-mounted, whereas the API pump will be centerline mounted. Refer the attached sketch. In foot-mounted pumps casing heat tends to be conducted into the mounting surfaces and thermal growth will be noticeable. It is generlly easier to maintain alignment of API pumps since their supports are surrounded by the typically moderate-temperature ambient environment.
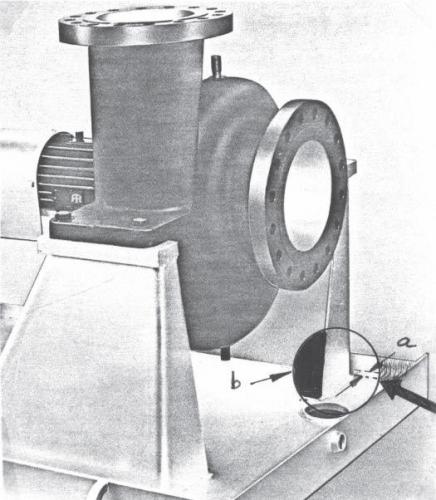
The decision on API vs ANSI construction is experience-based and is not governed by governmental or regulatory agencies. However, experienced machinery specialists have their own likes and dislikes based on the experience gathered by them over their long years in the machinery field.
Many highly experienced and reliability-focused machinery engineers would prefer to use pumps designed and constructed according to API 610 for toxic, flammable, or explosion-proof services at on-site locations in close proximity to furnaces and boilers in some of the conditions (rules-of-thumb) that are listed below:
a. Head exceeds 106.6 m (350 ft)
b. Temperature of pumpage exceeds 149°C (300°F) on pumps with discharge flange sizes larger than 4 inch or 177°C (350°F) on pumps with 4 inch discharge flange size or less.
c. Driver horsepower exceeds 74 kW (100 hp)
d. Suction pressure in excess of 516 kPag (75 psig)
e. Rated flow exceeds flow at best efficiency point (BEP)
f. Pump speed in excess of 3600 rpm.
The author mentions that there have been exceptions made where deviations from the rules-of-thumb were minor, or in situations where the pump manufacturer was able to demonstrate considerable experience with ANSI pumps under the same, or even more adverse conditions.
Finally the author gives his opinion on choosing either API or ANSI pumps based on the following:
Conventional Wisdom: API-compliant pumps are always a better choice than ANSI or ISO pumps
Fact: Unless flammable, toxic or explosion-prone liquids are involved, many carefully selected, properly installed, operated and maintained ANSI or ISO pumps may represent an uncompromising and satisfactory choice.
Hope readers of my blog like this comparison of API & ANSI pumps provided by one of the foremost machinery specialists of our time.
Let me have your comments on this blog entry.
Regards,
Ankur.