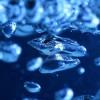
Beside the well-known application of treating Boiler Feed Water (BFW) with oxygen scavengers there are other applications which may require that the dissolved oxygen content in the water be reduced. One such application could be injection water for oil recovery from oil producer wells. Another application could be handling of produced water in upstream oil and gas where carbon steel piping and equipment is employed. The applications mentioned aforementioned are generally at or near ambient temperatures.
It is a well known fact that water has higher capacity to retain oxygen at lower temperatures than at higher temperatures or in simple terms lower the temperature higher the dissolved oxygen in water and vice-versa.
I had prepared an excel workbook wherein the various oxygen scavengers and their dosing rates are mentioned based on a reputed company standard. In the same workbook I had also provided a table and a graph plotted from the table for dissolved oxygen values in ppm against water temperature. The table is provided as an attachment for the benefit of the readers. The excel workbook is programmed to calculate the dosing rate for a particular oxygen scavenging chemical when the temperature of the water and the water flowrate has been specified as an input.
This particular excel workbook is applicable for dosing rates of oxygen scavenging chemicals in water at or around ambient temperatures. This workbook is not applicable for BFW since BFW is normally at or above its saturation temperature (100°C or above) and oxygen levels at these temperatures tend to be sub-ppm levels or parts per billion levels which is not accounted for in the dissolved oxygen versus water temperature table.
Some of the most commonly used oxygen scavenging chemicals are: 1) Carbohydrazide 2) Diethylhydroxylamine (DEHA) 3) Hydroquinone 4) Methyl Ethyl Ketoxime 5) Sodium Sulfite 6) Catalyzed Sodium Sulfite 7) Ammonium Bisulfite. The attached table provides the names and dosing rates based on per unit ppm of dissolved oxygen in the water to be treated.
Additional dosing is generally required over and above the stoichiometric requirements given in the attached table in order to ensure complete reaction and removal of dissolved oxygen from the water. As a rule-of-thumb dose 20 mg/L of scavenger in excess to the stoichiometric requirement.
Let us consider an example of 45% by weight ammonium bisulfite solution used as an oxygen scavenger. If 10,000 Liter of water containing 8 mg/L oxygen is to be treated with this solution then what would be the quantity of 45% ammonium bisulfite required.
The feed ratio for 100% ammonium bisulfite to oxygen ppm is 8 as defined in the attached table. Hence 45% ammonium bisulfite required:
[8*10,000 L*8 mg/L + 10,000 L*20 mg/L] / 0.45 = 1,866,666 mg or approximately 2 kg of 45% ammonium bisulfite solution.
The calculations are simple and anyone with basic knowledge of excel can program the oxygen scavenger dosing rates based on the attachments I am providing. At higher water temperatures (above 90°C) the calculations are not valid due to the lack of information on dissolved oxygen levels.
Hope to get some comments from the readers of my blog.
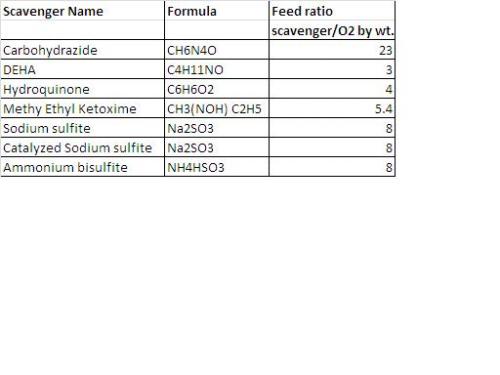
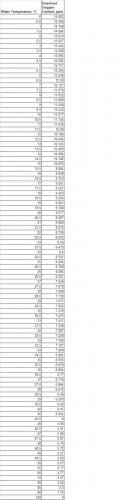
Regards,
Ankur.
I recommend periodically checking any automated DO scavenge system using the CHEMets colorimetric DO test kit (or similar). You should be able to shut off your chemical injection system and see the O2 level increase. Turn it back on and see the sample show in the low ppb range (or where ever you expect to operate). As a side note make sure the person performing the test is not color blind.