Dear All,
In a water bath heater, how do you explain the relationship between the fouling factor and the heat flux rate?
Heat flux rate calculated for both side, fire tube and process coils separately and it is based on heat flow per unit area of heat transfer surface.
Fouling factor is resistance to heat transfer due to some impurities and fouling in the fluid at the process side and the fire tube side.
As we all know Fouling factor used in the calculation of overall heat transfer coefficient which is overall heat transfer coefficient of the fire tube calculation. And it takes the outside and inside film heat transfer coefficient values for the heat surface area.
So, how can we explain those heat flux converted to fouling factor?
In advance I thank you for your inputs.
Kybele
|
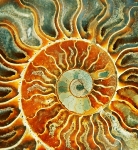
Heat Flux Rate And Fouling Factor
Started by kybele39, Jul 13 2010 08:38 AM
5 replies to this topic
Share this topic:
#1
Posted 13 July 2010 - 08:38 AM
#2
Posted 13 July 2010 - 09:15 AM
Kybele:
There is no "relationship" between a fouling factor and the heat flux of a direct-fired reboiler, coil, or submerged reboiler.
I don't understand why you are looking for one. The heat flux is a design consideration - mainly to distribute heat evenly and in such a way that vapor-binding is avoided on the external surface of a submerged reboiler tube bundle. If fouling of the bundle takes place, the heat transfer area is still there but the available heat transfer rate is not - due to increased heat transfer resistance. The effective heat flux is reduced; but the design heat flux remains. Fouling is a detriment to achieving the design heat flux - and rate.
Fouling is to be avoided and the design heat flux rate is required to maintain design heat transfer. There should not be any "fouling" to cope with on a normal hot water bath heater - at least not on an industrial design scale. You should only be using fully treated water as makeup.
#3
Posted 13 July 2010 - 09:52 AM
Dear Art,
Thank you very much for your response.
I did ask this question because in the industry people are looking for a great equipment. And want to understand the effects of the parameters before they use it. So when I say my assumption is 0.1% fouling in the system they automatically think their flux rate will change by time and the thermal efficiency of the heater will change. This may true to a degree.If the design is not sufficient for the environment.(This is my interpretation only and I might be wrong.)
I am using glycol instead of hot water, and heating NG. Using glycol will eliminate my cost for the hot water treatment. Plus I am already assuming 0.1% fouling factor for the process coil and I am calculating 0.1% fouling rate for the fire tube. My flux rate calculated based on 10000 btu/hr-ft2 on the process coil and 12000btu/hr-ft2 on the fire tube side.
As firing NG in the burner and heating NG in the coil with using glycol in the bath will not cause any fouling that will create a drop on the design flux rate. (This is again my interpretation from your response and my HT knowledge). However, this is always asked and may be misinterpreted by the industry people which is measuring a flux rate in the tube. My next question this is. How do we measure the flux rate?
As always, I thank you very much for your valuable inputs. And I hope this discussions related to water bath heaters can benefits to everyone.
Kybele
Thank you very much for your response.
I did ask this question because in the industry people are looking for a great equipment. And want to understand the effects of the parameters before they use it. So when I say my assumption is 0.1% fouling in the system they automatically think their flux rate will change by time and the thermal efficiency of the heater will change. This may true to a degree.If the design is not sufficient for the environment.(This is my interpretation only and I might be wrong.)
I am using glycol instead of hot water, and heating NG. Using glycol will eliminate my cost for the hot water treatment. Plus I am already assuming 0.1% fouling factor for the process coil and I am calculating 0.1% fouling rate for the fire tube. My flux rate calculated based on 10000 btu/hr-ft2 on the process coil and 12000btu/hr-ft2 on the fire tube side.
As firing NG in the burner and heating NG in the coil with using glycol in the bath will not cause any fouling that will create a drop on the design flux rate. (This is again my interpretation from your response and my HT knowledge). However, this is always asked and may be misinterpreted by the industry people which is measuring a flux rate in the tube. My next question this is. How do we measure the flux rate?
As always, I thank you very much for your valuable inputs. And I hope this discussions related to water bath heaters can benefits to everyone.
Kybele
#4
Posted 13 July 2010 - 10:34 AM
Kybele:
If you want to apply a fouling effect to your water bath heater, then essentially what you are doing is that you are inflating the size of the heat transfer area required at the initial onset of the heating operation. If fouling does, indeed, take place as the heating operation proceeds - then you will begin to "degrade" your heating surface and your heat flux will start to increase from a conservative, initial low figure to a higher figure. Presumably you would stop the heating when the heat flux reaches the design point, or when it surpasses it, and you will resort to cleaning the unit to restore it to the original, conservative heat flux level and put it back into service.
What this all means simply is that you are over-sizing the required tube bundle and paying extra for the additional heat transfer area you are requesting (as specified by the included fouling factor). Your unit will work very well at the reduced heat flux experienced at the onset - and if no fouling occurs, it should work very well. However, you are going to pay for the extra area in capital monies up front.
You measure the heat flux at the clean, onset condition. That is what you are paying for initially. What happens after that is under your control. I believe that is what all fabricators of water bath equipment will tell you.
#5
Posted 13 July 2010 - 10:40 AM
Looking at the heat flux equation, q = U*dT, it is clear that increasing heat flux normally means increasing the hot fluid temperature or (rarely) heat transfer coefficient by e.g. increasing the velocity through tubes or installing high-flux tubes which has certain surface area improvements. As long as there is no degradation of fluids caused by increased temperature difference, the fouling factor will not be affected.
#6
Posted 13 July 2010 - 12:40 PM
Kybele:
Art is right. Fouling is a phenomenon that occurs based on the nature of fluid, process conditions and on the surface conditions. Flux is something that you design for; be realistic about what you can achieve; on paper, you can push through any amount of BTU per ft2 per hour !!!; Is it practical??
Also I'd suggest you browse the article " No Fooling; No fouling" as suggested by Art in a different trail of question.
Sometimes, Process Engineers, specify more fouling than needed, and end up with a higher Heat Transfer area. On one hand, you pay more (Capital Costs). On the other, it may (may) be detrimental to the exchanger. The higher area, leads to lower velocities, and lower velocities tend to favor fouling.
In your case, a bath, may or may apply.
I'd suggest you explain your problem with some more specifics, and make the most of the forum.
Good Luck
MVP
Art is right. Fouling is a phenomenon that occurs based on the nature of fluid, process conditions and on the surface conditions. Flux is something that you design for; be realistic about what you can achieve; on paper, you can push through any amount of BTU per ft2 per hour !!!; Is it practical??
Also I'd suggest you browse the article " No Fooling; No fouling" as suggested by Art in a different trail of question.
Sometimes, Process Engineers, specify more fouling than needed, and end up with a higher Heat Transfer area. On one hand, you pay more (Capital Costs). On the other, it may (may) be detrimental to the exchanger. The higher area, leads to lower velocities, and lower velocities tend to favor fouling.
In your case, a bath, may or may apply.
I'd suggest you explain your problem with some more specifics, and make the most of the forum.
Good Luck
MVP
Similar Topics
Steam Pressure In Heat ExchangerStarted by Guest_mvanrijnbach_* , 15 Apr 2025 |
|
![]() |
||
Heat Exchanger Steam FlowStarted by Guest_aliebrahem17_* , 25 Nov 2024 |
|
![]() |
||
Discussion - Predict Storage Tank Heat Transfer Precisely By Jimmy D KStarted by Guest_raj shekhar_* , 25 Mar 2025 |
|
![]() |
||
Cross Over Temperature In Countercurrent Heat ExchangerStarted by Guest_panoska_* , 18 Feb 2025 |
|
![]() |
||
Aspen Hysys - Blowdown Utility Heat Flux MethodStarted by Guest_yuvi.ardekar1999@gmail.com_* , 27 Feb 2025 |
|
![]() |