Dear All,
Could you please any body can advise me how we can simulate a liquid ring compressor in hysys?
My main concern is circulated seal liquid will combine with suction or discharge gas of compressor?
another point is how we can calculate outlet temperature from compressor when inlet gas condition e.g. flowrate and composition changed.
Rgrds
Afshin
|
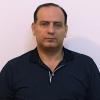
Simulation Of Liquid Ring Compressor In Hysys
Started by Afshin445, Jan 27 2011 10:44 PM
4 replies to this topic
Share this topic:
#1
Posted 27 January 2011 - 10:44 PM
#2
Posted 28 January 2011 - 12:59 AM
Afshin,
HYSYS provides flexibility to opt for both centrifugal and reciprocating compressors. However, reciprocating compressors are a little complicated to specify since information such as cylinder dimensions, bore, stroke, clearance volumes need to be specified to model a reciprocating compressor. Centrifugal compressors are easier to model in HYSYS.
While modeling existing compressors you need to enter data available from the compressor manufacturer in the form of capacity versus head curves.
There is no specific item in HYSYS such as a liquid ring compressor as well as a seal liquid circulation system. These need to be modeled separately as other pieces of equipment using our engineering understanding and judgment.
For the last part of your question the discharge or outlet temperature (T2) of a compressor stage is the function of the inlet temperature (T1) to the stage, the compression ratio for the stage (Pout / Pin) and the specific heat ratio (k) of the gas being compressed and has no relation with the flow rate. The thermodynamic equation for discharge temperature thus becomes:
T2 = T1*(Pout / Pin)k-1/k
Hope this helps.
Regards,
Ankur.
HYSYS provides flexibility to opt for both centrifugal and reciprocating compressors. However, reciprocating compressors are a little complicated to specify since information such as cylinder dimensions, bore, stroke, clearance volumes need to be specified to model a reciprocating compressor. Centrifugal compressors are easier to model in HYSYS.
While modeling existing compressors you need to enter data available from the compressor manufacturer in the form of capacity versus head curves.
There is no specific item in HYSYS such as a liquid ring compressor as well as a seal liquid circulation system. These need to be modeled separately as other pieces of equipment using our engineering understanding and judgment.
For the last part of your question the discharge or outlet temperature (T2) of a compressor stage is the function of the inlet temperature (T1) to the stage, the compression ratio for the stage (Pout / Pin) and the specific heat ratio (k) of the gas being compressed and has no relation with the flow rate. The thermodynamic equation for discharge temperature thus becomes:
T2 = T1*(Pout / Pin)k-1/k
Hope this helps.
Regards,
Ankur.
#3
Posted 28 January 2011 - 01:48 AM
Dear Ankur,
My main question is how we can model the liquid seal stream by hysys.If we combine liquid by gas in suction we received "Liquid in Compressor" warning and If we change this to discharge I don't know is correct or no.I used process information received from vendor but I can't reach to discharge temperature vendor gave to me(60 C) with both scheme, then I used dummey exchanger (as per attached file) to reach vendor discharge temperature.
I only need to calculate discharge temperature and I want to change feed for different flowrates and composition, but I don't know my modeling is correct or not?
Rgrds
Afshin
My main question is how we can model the liquid seal stream by hysys.If we combine liquid by gas in suction we received "Liquid in Compressor" warning and If we change this to discharge I don't know is correct or no.I used process information received from vendor but I can't reach to discharge temperature vendor gave to me(60 C) with both scheme, then I used dummey exchanger (as per attached file) to reach vendor discharge temperature.
I only need to calculate discharge temperature and I want to change feed for different flowrates and composition, but I don't know my modeling is correct or not?
Rgrds
Afshin
Attached Files
Edited by Afshin, 28 January 2011 - 01:49 AM.
#4
Posted 29 January 2011 - 12:24 AM
Dear,
This is common practice of combining the CDU cold reflux drum compressed vapors and the liquid before it enters in the cooler and subsequent to Naphtha Stabilizer Feed drum. From your sketch I am not understood why you need the cooler E-100 where you reduce temperature of the liquid to 50 Deg C, rather I will suggest you to connect the stream number-3 to RCY-1 inlet. Now you can check the temperature of the combine stream.
Another concern is that the compressor modeling where it is shown a single stage compressor of having a compression ratio of 8.0 which is industrially unrealistic (Compressor discharge Temperature limits < 130 to 150 Deg C as commonly seen), since the discharge temperature is too high i.e. 237.7 Deg C. Try compressor stages with an equal compression ratio with inter cooling option. Collect all liquids with the Recycle Operation in a minimum pressure drum (it may be the 1st stage discharge KOD / or second stage suction KOD and pump the liquid to mix with the last stage vapors. Hope you understand what I mean to suggest.
This is common practice of combining the CDU cold reflux drum compressed vapors and the liquid before it enters in the cooler and subsequent to Naphtha Stabilizer Feed drum. From your sketch I am not understood why you need the cooler E-100 where you reduce temperature of the liquid to 50 Deg C, rather I will suggest you to connect the stream number-3 to RCY-1 inlet. Now you can check the temperature of the combine stream.
Another concern is that the compressor modeling where it is shown a single stage compressor of having a compression ratio of 8.0 which is industrially unrealistic (Compressor discharge Temperature limits < 130 to 150 Deg C as commonly seen), since the discharge temperature is too high i.e. 237.7 Deg C. Try compressor stages with an equal compression ratio with inter cooling option. Collect all liquids with the Recycle Operation in a minimum pressure drum (it may be the 1st stage discharge KOD / or second stage suction KOD and pump the liquid to mix with the last stage vapors. Hope you understand what I mean to suggest.
#5
Posted 30 January 2011 - 08:08 PM
Dear Sir,
Thank you for your fast reply and information.
With attached scheme I tried to model vendor process data for liquid ring compressor(LRC) we have in our project.
As per vendor P&ID, they used an air cooler to cool sealing liquid (Water) from 60 to 50 cel. and E-100 is that cooler.
Your description about 2 stage compressor is wright and we need two stage compressor for this compression ratio but In LRC we have isothermal compression (In my case discharge temperature is also lower).
My main concern is that,how I can simulate liquid ring stream?it must add to discharge or suction side of compressor?
If gas flowrate or composition will be changed is it any effect of discharge temperatur?
How we can calculate sealing liquid flowrate?
Your prompt responce is appriciated.
Rgrds
Afshin
Thank you for your fast reply and information.
With attached scheme I tried to model vendor process data for liquid ring compressor(LRC) we have in our project.
As per vendor P&ID, they used an air cooler to cool sealing liquid (Water) from 60 to 50 cel. and E-100 is that cooler.
Your description about 2 stage compressor is wright and we need two stage compressor for this compression ratio but In LRC we have isothermal compression (In my case discharge temperature is also lower).
My main concern is that,how I can simulate liquid ring stream?it must add to discharge or suction side of compressor?
If gas flowrate or composition will be changed is it any effect of discharge temperatur?
How we can calculate sealing liquid flowrate?
Your prompt responce is appriciated.
Rgrds
Afshin
Edited by Art Montemayor, 30 January 2011 - 08:39 PM.
Similar Topics
![]() Hysys Expander/compressor Input Using Dimensionless CurveStarted by Guest_Alfreedo_* , 21 Apr 2025 |
|
![]() |
||
Water Hammer Study: Hysys Dynamics Vs PipenetStarted by Guest_powerox29_* , 07 Apr 2025 |
|
![]() |
||
![]() Steam Carrying Liquid From The Sour Water Stripping TowerStarted by Guest_kaidlut_* , 12 Sep 2024 |
|
![]() |
||
Dynamic Simulation - SeparatorsStarted by Guest_tomr91_* , 10 Mar 2025 |
|
![]() |
||
![]() Dynamic Simulation After Feed Flow ReductionStarted by Guest_Kakashi-01_* , 20 Mar 2025 |
|
![]() |