I am a recently graduated Chemical engineer working for a design consultancy providing liquid drying plants.
I am working on dehydration of Tetrahydrofuran liquid from its intial water content of 3% by wt to less than 200 ppm level in the dried product using Molecular sieve 4A adsorbent. THF flowate is 125 L/hr.
We are going to design the bed for adsorption cycle of 24 hrs. It is a dual bed process (one would be in adsorption cycle while the other on desorption mode)
I have been carrying out lab scale experimentation to generate break through curve.
My concerns are
1. Scale up approach: What is the usual approach to scale up the process to full scale i.e by using L= LUB + LES obtained from break through data. or calculating amount of adsorbent required assuming 5% dynamic
efficiency of adsorbent (Mol Sieve 4A) to adsorb "X" quantity of adsorbate for a given number of hours of operation (in this case it is 24 hours). Which is the best approach of the two approaches mentioned
above.
2.what should be the superficial velocity of liquid through the adsorption bed (any thumb rule); THF is flowing in a bottom to top direction throgh the adsorber. Is it necessary to maintain superficial
velocity of liquid to be the same in full scale as was maintained during lab scale experimentation.
3. What should be H/D for the adsorption bed.
4. Temperature rise of the adsorption bed: If it is very significant we are planning to incorporate internal cooling coils to remove heat of adsorption. how to calculate temperature rise of both adsorption
bed as well as THF fluid ( B.P of THF = 66 C @ atm pressure) during adsorption.
Your assistance would be very much helpful to me.
|
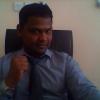
Thf Dehydration Molecular Sieve 4A
Started by Mohd Rasool, Apr 16 2011 02:44 AM
5 replies to this topic
Share this topic:
#1
Posted 16 April 2011 - 02:44 AM
#2
Posted 16 April 2011 - 11:23 AM
Mohd:
Go to the following thread on this Forum:
http://www.cheresour...ose&f=2&t=12418
After reading that and downloading the recommended Paper on How to Design an Adsorption Column, use our Search Feature by typing in the key word “Adsorption”. You will find numerous threads on the subject and these should answer or address all of your query.
Basically:
- Working to generate a “break-through” curve is fine if it helps you understand the process and makes you feel good. It does you no good for the design of the actual unit. The break-through point is an academic issue – you never want to go there (or even near there). You design to avoid the break-through from taking place. Otherwise, you wind up with wet product! I personally think you are wasting your time on break-through, but if you think it helps you out, fine.
- A 24-hour NEMA cycle is a good decision, in my opinion, for an industrial process.
- You fail to tell us the most important basic data: what is the type of cycle? Is it a Thermal Swing Adsorption (TSA) type? I would hope it is. You also fail to tell us HOW you will regenerate: with dry, hot nitrogen? Hot humid air? How will you purge? How will you cool down? How will you salvage the residual (and valuable) THF left in the spent bed. What is the design bed regeneration temperature used?
- You don’t “scale up” an adsorption process – no more than you scale up a distillation process. You should know enough to design it outright.
- Follow the adsorbent manufacturer’s recommendations. They are the experts – not you. Use their recommended superficial velocities – as a maximum. And stop fussing about the L/D ratio. This takes care of itself when you stick to not exceeding the recommended superficial velocities – that obviously sets the diameter of the columns. That is common sense.
- You should generate or find out about any temperature rise in the bed by running the pilot unit. Now THAT is useful pilot information.
#3
Posted 18 April 2011 - 08:52 AM
Thanks Art Sir,
As you have rightly pointed out it is TSA (Temperature Swing Adsorption) cycle. We shall use Nitrogen gas with a flow rate of around 250 Nm3/hr in a closed loop by heating it to a temperature of around 280 C so that Molecular sieve bed temperature of 250 C could be attained. Make up Nitrogen is available @ 5 Nm3/hr.
Desorption cycle consists of 14 hrs of purging with hot nitrogen gas in the direction counter current to adsorption, 4 hours of cooling with ambient temp nitrogen in concurrent direction to adsorption until bed temperature drops down to around 60 C and rest 6 hours idling time.
1. Is this sequence of regeneration OK. What could be the problems associated with using purge Nitrogen gas in a closed regeneration loop due to non availability of enough Nitrogen gas required for regeneration at Client's Site from a PSA process...?
2. Is it ok if we heat the Mol Sieve bed to 250 C for regeneration or we need to go for still higher temperatures without collapsing the porous structure of adsorbent.
2. Which is more justifiable option, using internal cooling coils or pre-chilling THF fluid to a temperature of say 10 C before adsorption step being carried out, if bed temp rise is significant during adsorption step...???
3. Does Empirical criteria of Cross Over Ratio (COR) i.e. to know relative velocities of thermal and mass transfer front in the adsorption bed; plays any significant role in the design of adsorption process...??
4. One last question, Which is more suitable Adsorbent Mol Sieve 3A or Mol Sieve 4A for dehydration of Tetrahydrofuran...???
As you have rightly pointed out it is TSA (Temperature Swing Adsorption) cycle. We shall use Nitrogen gas with a flow rate of around 250 Nm3/hr in a closed loop by heating it to a temperature of around 280 C so that Molecular sieve bed temperature of 250 C could be attained. Make up Nitrogen is available @ 5 Nm3/hr.
Desorption cycle consists of 14 hrs of purging with hot nitrogen gas in the direction counter current to adsorption, 4 hours of cooling with ambient temp nitrogen in concurrent direction to adsorption until bed temperature drops down to around 60 C and rest 6 hours idling time.
1. Is this sequence of regeneration OK. What could be the problems associated with using purge Nitrogen gas in a closed regeneration loop due to non availability of enough Nitrogen gas required for regeneration at Client's Site from a PSA process...?
2. Is it ok if we heat the Mol Sieve bed to 250 C for regeneration or we need to go for still higher temperatures without collapsing the porous structure of adsorbent.
2. Which is more justifiable option, using internal cooling coils or pre-chilling THF fluid to a temperature of say 10 C before adsorption step being carried out, if bed temp rise is significant during adsorption step...???
3. Does Empirical criteria of Cross Over Ratio (COR) i.e. to know relative velocities of thermal and mass transfer front in the adsorption bed; plays any significant role in the design of adsorption process...??
4. One last question, Which is more suitable Adsorbent Mol Sieve 3A or Mol Sieve 4A for dehydration of Tetrahydrofuran...???
#4
Posted 18 April 2011 - 12:34 PM
Mohd:
You are asking a lot of detailed, engineering design questions and yet you have not furnished any detailed design information yourself. You have furnished some design data, but no PFD, material and heat balance, a P&ID or sample calculations.
I can respond to your need for advice and comments, but I can’t furnish detailed design information that you require for the design of what you are furnishing your client. You ask for details on the adsorbent, and I have already clearly commented: “Follow the adsorbent manufacturer’s recommendations. They are the experts – not you.” I think this was explicit enough.
I can’t comment on the sequence of regeneration without a copy of the detailed calculations that confirm what you propose.
Without a detailed PFD and P&ID, I can’t indentify what you call “purge” and what you call “closed loop” circulated nitrogen. What do you call “makeup nitrogen”?
You propose a drying upward flow direction and a downward heating direction with a subsequent bed cooling that is in an upward direction. If your cooling nitrogen fluid has any water vapor in it, you will contaminate the bed and will require extra adsorbent to meet specifications.
If I have misunderstood your process, it is because you haven’t furnished what I describe above.
#5
Posted 21 April 2011 - 05:54 AM
I have attached a schematic of the THF Drying process... hope this would make things clearer to a greater extent... this project is yet in design stage... Same nitrogen gas is being used for regeneration by reheating in an electric heater after stripping liquid in a knock out drum.
I was expecting to get some advice for my above queries from the professionals in the forum who have vast experience in design, operation and trouble shooting of such processes...
I tried to contact UOP India Mol Sieve supplier to know the value of maximum superficial velocity recommended for the process but to no avail. This was the reason I had approached the forum to know its optimum value (range) to start with.
To know bed temperature rise... I shall monitor temperature profile of the lab scale experimental adsorber.
any article or literature to predict the bed temperature rise would help me a lot....
Has any body came across the situation of pre-chilling the adsorbing fluid before adsorption to avoid significant temperature rise of the bed or providing internal cooling coils in the bed is the better option. I hope providing external jacket to bed serves no means for effective heat transfer in adsorption process.
Kindly oblige.
I was expecting to get some advice for my above queries from the professionals in the forum who have vast experience in design, operation and trouble shooting of such processes...
I tried to contact UOP India Mol Sieve supplier to know the value of maximum superficial velocity recommended for the process but to no avail. This was the reason I had approached the forum to know its optimum value (range) to start with.
To know bed temperature rise... I shall monitor temperature profile of the lab scale experimental adsorber.
any article or literature to predict the bed temperature rise would help me a lot....
Has any body came across the situation of pre-chilling the adsorbing fluid before adsorption to avoid significant temperature rise of the bed or providing internal cooling coils in the bed is the better option. I hope providing external jacket to bed serves no means for effective heat transfer in adsorption process.
Kindly oblige.
Attached Files
#6
Posted 21 April 2011 - 11:55 AM
Mohd:
Please download and study the attached Workbook very carefully. Next time, invest some of your time in producing a decent flow diagram that another engineer can mark up and/or make comments on. It is impossible to make comments on your sketch and I have had to invest my time and effort in generating a quick version of what you are trying to show in order to make my comments.
Your very elementary sketch has several major flaws and errors that you should be made aware of.
You should not depend solely on UOP for adsorbent expert advice. There are many other suppliers of Molecular sieves and you should contact them as well. UOP did not develop Molecular Sieves. They got into the market quite late in the game. American Linde (when it belonged to Union Carbide) invented and developed Molecular Sieves in 1960. They are the original and leading experts in Mol Sieve adsorption and research.
Do not waste time believing that you can control a packed bed with a vessel cooling jacket. That is not only inefficient, it is impractical. So are internal cooling coils. If you have to cool, use a sub-cooled feed.
Attached Files
Similar Topics
![]() ![]() Molecular Sieve UnitStarted by Guest_Sufy_* , 26 Feb 2025 |
|
![]() |
||
Molecular Sieve Regeneration At High PressureStarted by Guest_Victor_process_Engineer_* , 07 Jan 2025 |
|
![]() |
||
![]() Teg DehydrationStarted by Guest_Root_* , 22 Aug 2022 |
|
![]() |
||
Low Molecular Flaring (H2 Rich Flare Gas)Started by Guest_TechExpert_* , 23 Dec 2023 |
|
![]() |
||
![]() Sieve Tray Rating In Aspen PlusStarted by Guest_Root_* , 24 Sep 2023 |
|
![]() |