|
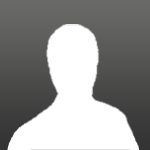
Temperature Cross In Hysys
Started by ramlalithravi, Oct 13 2011 12:56 AM
5 replies to this topic
Share this topic:
#1
Posted 13 October 2011 - 12:56 AM
I would like to know what is the rectification method to solve temperature cross in HYSYS. Which parameter to be adjusted and in such a way to avoid temperature cross.
Which is also associated with "FT Correction factor is Low". I presume FT is resistance co-efficient due to fouling of the material that should be accounted while calculating overall heat transfer co-efficient. So that Low FT factor will results in more Overall heat transfer co-efficient and ultimately leads to temeperature cross. If i am wrong, pls correct me and give ur ideas.
regards,
ramesh
#2
Posted 19 October 2011 - 11:42 AM
Ramesh
FT factor is not related to fouling in exchanger. It indicates how far off you are from perfect counter-current flow. The equation, Q=UA (LMTD) assumes perfect countercurrent flow. But that is not actually the case with shell & tube heat exchangers. Hence we use FT factor, which is the LMTD correction factor. It depends upon temperatures,number of shells in series, no of passes etc. Obviously too low FT is not preferred as it will lead to very large heat transferred area.
Coming to your second question, when hysys detects a temperature cross, you can remove the cross by changing outlet temp specification that you have given. If you don't want to change your temp specification, play with number of passes and number of shells in series to remove cross.
Actually the best way to simulate an exchanger is to specify minimum approach or HOCO, HICO, HOCI approach ( depending upon no. of passes on tube & shell side), which will ensure that you don't come across a temperature cross.
Hope this helps
Amit
FT factor is not related to fouling in exchanger. It indicates how far off you are from perfect counter-current flow. The equation, Q=UA (LMTD) assumes perfect countercurrent flow. But that is not actually the case with shell & tube heat exchangers. Hence we use FT factor, which is the LMTD correction factor. It depends upon temperatures,number of shells in series, no of passes etc. Obviously too low FT is not preferred as it will lead to very large heat transferred area.
Coming to your second question, when hysys detects a temperature cross, you can remove the cross by changing outlet temp specification that you have given. If you don't want to change your temp specification, play with number of passes and number of shells in series to remove cross.
Actually the best way to simulate an exchanger is to specify minimum approach or HOCO, HICO, HOCI approach ( depending upon no. of passes on tube & shell side), which will ensure that you don't come across a temperature cross.
Hope this helps
Amit
#3
Posted 19 October 2011 - 08:15 PM
hi ramesh
like Amit said, FT doesn't relate to the fouling on exchanger. it's a function of fluid temperature and the number of tube and shell passes.
in case of you, temperature cross presenting and FT is too low, you may try to select the exchanger exactly performing the counter flow exchanger. i.e. 1 shell pass & 1 tube pass.
this can increase the Ft factor and your exchanger will perform at the better effectiveness.
good luck
like Amit said, FT doesn't relate to the fouling on exchanger. it's a function of fluid temperature and the number of tube and shell passes.
in case of you, temperature cross presenting and FT is too low, you may try to select the exchanger exactly performing the counter flow exchanger. i.e. 1 shell pass & 1 tube pass.
this can increase the Ft factor and your exchanger will perform at the better effectiveness.
good luck
#4
Posted 02 November 2011 - 04:27 AM
The quick way is to define it 1 shell pass & 1 tube pass and make the volumes both shell and tube are zero.
#5
Posted 22 January 2012 - 09:46 PM
Usually we would like that mass velocity of fluid flowing through the exchanger increases, so that the
film coefficients increase improving heat transfer and reducing the physical size and cost of the exchanger. But, increasing the fluid mass velocity will also increase the pressure drop across the unit.
So, it's beter to adjust the pressure drop close to allowalbe pressure drop limit to get a optimal design.
film coefficients increase improving heat transfer and reducing the physical size and cost of the exchanger. But, increasing the fluid mass velocity will also increase the pressure drop across the unit.
So, it's beter to adjust the pressure drop close to allowalbe pressure drop limit to get a optimal design.
#6
Posted 23 January 2012 - 10:53 PM
Similar Topics
![]() Hysys Expander/compressor Input Using Dimensionless CurveStarted by Guest_Alfreedo_* , 21 Apr 2025 |
|
![]() |
||
Water Hammer Study: Hysys Dynamics Vs PipenetStarted by Guest_powerox29_* , 07 Apr 2025 |
|
![]() |
||
Need Help In Hysys For Production Of Vinyl AcetateStarted by Guest_christinalee12_* , 31 Mar 2025 |
|
![]() |
||
Cross Over Temperature In Countercurrent Heat ExchangerStarted by Guest_panoska_* , 18 Feb 2025 |
|
![]() |
||
Aspen Hysys - Blowdown Utility Heat Flux MethodStarted by Guest_yuvi.ardekar1999@gmail.com_* , 27 Feb 2025 |
|
![]() |