|
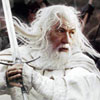
Atmospheric Tanks Pressure And Vacuum Relief
Started by djack77494, Nov 01 2005 02:17 PM
10 replies to this topic
Share this topic:
#1
Posted 01 November 2005 - 02:17 PM
In the design of relief devices for "atmospheric" or API-650 storage tanks, does it make any difference how the tank is designed and constructed? I know that API-2000 (and other standards) define the quantity of vent gases that must be allowed for. Though I've faced the problem many times, I find the way the whole topic is dealt with to be confusing. Ultimately a relief device is selected (should we say designed?). Most have characteristics of opening in proportion to the force exerted on the seat (it's really an orifice?). Thus the device provides an open or flow area that is in proportion to the force (or pressure difference). I've often heard it said that the device will not be fully open until the internal (tank) pressure is double the setpoint. Does that mean the setpoint should be 1/2 of the maximum pressure you want? Beyond that, what is the maximum allowable pressure for an old tank whose nameplate says the design pressure is "Atmospheric"? (Please don't suggest getting measurements of the tank's thickness if you respond to this question.) This is not just an interesting mental exercise. I've been asked in the past to add a blanketing system to such a tank to keep air away from an oxygen sensitive material. So you want to put in a blanket gas valve to admit say nitrogen when the pressure drops below a certain point. And you want to put in an exhaust valve to open and vent the nitrogen when the pressure increases above a certain point. What are those points? Obviously there are pressures used to size the pressure and vacuum relief devices since the flowrate that passes through the device depends on the pressure differential. So there must be some understood design pressure and vacuum. What are they? I find it somewhat frightening that I'm even asking questions such as these.
#2
Posted 01 November 2005 - 08:28 PM
Hi, you have many questions here. Might I suggest that you look at the several articles on my site, www.ostand.com, as they might be helpful.
Regards,
Regards,
#3
Posted 04 November 2005 - 08:51 AM
Thank you Mr. Ostand for making your paper(s) available to the public. That is a much appreciated public service to offer.
I read through your papers and agree that they offer a significant amount of material related to the subject of tank blanketing and venting. Much of the material skirts the issues I raised, however, and I feel that the subject I am most interested in is not addressed. More and more, I am feeling that there is no answer. Even the most knowledgable experts in our field have given this and related inquiries a miss in the past. Just to be absolutely clear about what is, to me, the most compelling part of the problem, allow me to restate it.
Is there any minimum pressure, be it as low as a fraction of an inch of water, that I can believe an mechanically sound "atmospheric" storage tank is capable of withstanding?
Without taking measurements and calling in vessel specialists to perform detailed calculations based on those measurements, is there some pressure that these tanks would be designed to? Even if it relates to the tank size, I would still be interested in knowing. If there just isn't any minimum pressure (or vacuum) that these tanks are built to, I would appreciate hearing that also.
Thanks,
Doug
I read through your papers and agree that they offer a significant amount of material related to the subject of tank blanketing and venting. Much of the material skirts the issues I raised, however, and I feel that the subject I am most interested in is not addressed. More and more, I am feeling that there is no answer. Even the most knowledgable experts in our field have given this and related inquiries a miss in the past. Just to be absolutely clear about what is, to me, the most compelling part of the problem, allow me to restate it.
Is there any minimum pressure, be it as low as a fraction of an inch of water, that I can believe an mechanically sound "atmospheric" storage tank is capable of withstanding?
Without taking measurements and calling in vessel specialists to perform detailed calculations based on those measurements, is there some pressure that these tanks would be designed to? Even if it relates to the tank size, I would still be interested in knowing. If there just isn't any minimum pressure (or vacuum) that these tanks are built to, I would appreciate hearing that also.
Thanks,
Doug
#4
Posted 04 November 2005 - 09:05 AM
It's probably bad form to "double post", but a new thought just came to me. Of course, it was milliseconds after I pressed the "SEND" button.
Least viewers think this is a ridiculous or irrelevant question, let me suggest a very reasonable scenario where it could arise. If there are solutions to the imagined problem that do not involve the tank's pressure holding ability, then I will consider the matter closed.
Say you have an existing atmospheric storage tank used to hold water. In a revamp situation, you'd like to change services on this tank and use it to store a material which degrades when exposed to moisture. (Of course you'll thoroughly dry the tank before reuse.) You decide to put a nitrogen blanketing system, or a vent pipe with a desiccant on the tank to exclude moisture, but you need to provide the valve vendor with setpoints. What to use? What pressure differential could you design a desiccant chamber for? Could you design this system if the tag on the tank listed the design pressure as "Atmospheric"?
I've been in that situation and had other engineers say, "Just use a setpoint of ____ in W.C. They're all designed to withstand that." One thing for sure is that people will think you're a *erk if your answer is to take thickness measurements and call a vessel specialist to analyze the sutuation. Somehow, that approach seems rather dangerous to me, no matter how low the number used to fill in the blank. Comments please.
Least viewers think this is a ridiculous or irrelevant question, let me suggest a very reasonable scenario where it could arise. If there are solutions to the imagined problem that do not involve the tank's pressure holding ability, then I will consider the matter closed.
Say you have an existing atmospheric storage tank used to hold water. In a revamp situation, you'd like to change services on this tank and use it to store a material which degrades when exposed to moisture. (Of course you'll thoroughly dry the tank before reuse.) You decide to put a nitrogen blanketing system, or a vent pipe with a desiccant on the tank to exclude moisture, but you need to provide the valve vendor with setpoints. What to use? What pressure differential could you design a desiccant chamber for? Could you design this system if the tag on the tank listed the design pressure as "Atmospheric"?
I've been in that situation and had other engineers say, "Just use a setpoint of ____ in W.C. They're all designed to withstand that." One thing for sure is that people will think you're a *erk if your answer is to take thickness measurements and call a vessel specialist to analyze the sutuation. Somehow, that approach seems rather dangerous to me, no matter how low the number used to fill in the blank. Comments please.
#5
Posted 04 November 2005 - 01:29 PM
Doug,
I am not a tank designer, even though I am a ME and understand the stresses.
We can probably agree that the tank integrity is essential, regardless of the stored product. We can't have "the roof come off". Some older tanks simply have weak joints, or weak roof materials. It is not uncommon to find that a blanketed tank leaks to atmosphere because of these faults. Further, if the nameplate says "atmospheric", that's what it means. If x" wc is ok, then why not 2x?
Also, keep in mind that even if one blankets to 1 inch wc, there most likely will be pressures, at times, above this due to venting and vent valve pressure characteristics. Also, the lower the blanketing pressure, the more attention that must be given to the possibility of vacuum in the tank. Further, once you "button up" the tank, the higher the possibility of a more significant pressure rise due to overfill, thermals etc.
I realize your frustation in approaching your project with these statements. I hope that I don't anger you, but the issue comes down to if one does not know the pressure capability of the vessel, how can we pressurize it? Is the cost of an engineering investigation justified versus the possibility of structural failure, even a roof-shell seam cracking, and no more?
I am not a tank designer, even though I am a ME and understand the stresses.
We can probably agree that the tank integrity is essential, regardless of the stored product. We can't have "the roof come off". Some older tanks simply have weak joints, or weak roof materials. It is not uncommon to find that a blanketed tank leaks to atmosphere because of these faults. Further, if the nameplate says "atmospheric", that's what it means. If x" wc is ok, then why not 2x?
Also, keep in mind that even if one blankets to 1 inch wc, there most likely will be pressures, at times, above this due to venting and vent valve pressure characteristics. Also, the lower the blanketing pressure, the more attention that must be given to the possibility of vacuum in the tank. Further, once you "button up" the tank, the higher the possibility of a more significant pressure rise due to overfill, thermals etc.
I realize your frustation in approaching your project with these statements. I hope that I don't anger you, but the issue comes down to if one does not know the pressure capability of the vessel, how can we pressurize it? Is the cost of an engineering investigation justified versus the possibility of structural failure, even a roof-shell seam cracking, and no more?
#6
Posted 04 November 2005 - 02:22 PM
Doug:
I’ll try to make a contribution to this thread because I consider the basic question an important one that keeps repeating itself – in other threads and in other forums. I’ll address this to you, although it also is meant for all readers. I am confident I know the answer; however, I don’t know if I can successfully communicate it correctly or confirm it with my experience. I’ll give it a try, and I hope that Paul Ostand and other experienced engineers that have been through this trial also write a response. Low pressure storage tanks can be lethal and dangerous vessels – even in the pressure ranges of 0 to 15 psig and especially in the ranges of negative pressure (partial vacuum or “external pressure”).
In your example, you say you’re revamping an existing API water tank to include a N2 blanket system or a fixed desiccant chamber in the breathing pipe. You find yourself in a dilemma because you need to fix the set points and “dead band” for the tank’s instrumentation and don’t know how to obtain these. My reaction to the situation is that one should never attempt to make any modification on a vessel – whether pressure or storage – unless the actual design calculations or specifications are in hand or if one can generate (or calculate) the required mechanical specifications that meet the proposed application.
As I’ve stated in previous threads and personal correspondence in the past, an API 650 or 620 storage tank is usually built to conform to operating pressures of 0 – 5 psig and partial vacuums down to 24 inches of water column (WC). I have found this range to be very appropriate and flexible for application to a very large variety of liquid chemicals – with or without N2 blanketing. HOWEVER, the ranges I’ve mentioned aren’t necessarily the ones that a specific tank was designed and built for. Tank fabricators will build an API tank to your purchase specifications and order. It has been my experience in inheriting existing field tanks in the past that most (if not all) tanks were purchase with nothing more than the description of “API storage tank”, period. No engineering specification or guidelines were given to the fabricator – especially a requirement to design to a specific MAWP (maximum allowable working pressure) or MAWV (maximum allowable working vacuum) – nor was the requirement for written design calculations and an API stamp noted. Naturally, the fabricator did exactly as the purchaser indicated (or did not indicate) and supplied just that: an API storage tank (probably one that was already partially built and “on the shelf” for immediate application. The sad result is what I and many others (like you) have had to confront out in the field, trying to make a sound, safe, and economic engineering decision.
Some years ago I decided I was not going to jeopardize my health and life as well as other people’s by taking the attitude of “Just use a setpoint of ____ in W.C. They're all designed to withstand that.” I took a stand with what I thought was sound engineering and demanded that mechanical integrity be proven and documented in all tanks that I applied engineering on. I obtained what I thought was sound logic in the services of an experienced mechanical engineer with whom I worked hand-in-hand in making all vessel revamps. I learned a lot about what can and can’t be done with API storage tanks and the results speak for themselves: no “suck-ins”, stabile and safe operation, credible and reliable documented records, totally reduced emissions, minimal inert gas consumption, and quality product as well as raw material. I’ve done modifications such as umbrella roofs, anchor lugs, double-bottoms, wall re-enforcements, sloped floors, emissions controls, and many others. I would not attempt a revamp on a tank without a minimal of documentation and calculations that confirm the MAWP and MAWV of the vessel. That’s my comment, and I’ll add another directed to your specific first question: No, there is no “minimum pressure, be it as low as a fraction of an inch of water”, that one can believe a mechanically sound ‘atmospheric’ storage tank is capable of withstanding” - at least, not without proving it with checked, accurate, and documented calculations. That’s the very least that any owner can furnish you as an engineer working on their project. You deserve it, and you should have it coming to you. Fair is fair and you can’t compensate for past errors or omissions by taking steps that jeopardize your life and others. It isn’t morally (and now, finally) legally correct.
Paul Ostand has written a lengthy and, in my opinion, a very needed and useful paper on the employment of N2 blanketing. I dare not speak for such a qualified and experienced individual, but he does state the importance of storage tank mechanical integrity in his paper. Part I, under Methods and Requirements, states:
“When considering safety in relation to the gas blanketing system, bear in mind the following. The tank must be capable of operating at the desired pressure, with an appropriate factor of safety. The tank must be protected from vacuum and pressure that might occur outside of the operating pressure range and within safe limits of tank operation.”
So, even though Paul is not writing about API tank design and fabrication, he specifically identifies a pre-requisite for revamping a storage tank: make sure that your tank can withstand the pressures (or vacuums) you intend to impose on it before attempting any revamp.
Agreeably, our engineering logic and sound judgment is countered in the real-life applications where an owner expects his project engineer to correct a previous mistake or existing safety or environmental problem by simply “converting” a vessel to today’s state-of-the-art through the addition of new equipment on a rusted, non-stamped, undocumented piece of junk. I wouldn’t do it until it was proven that the subject vessel is, in fact, a reliable and mechanically sound piece of equipment with defined pressure ratings. I realize that it’s easy for me to assert my position strongly since I’m a consultant and my paycheck does not depend on any one individual liking me, my under-arm deodorant, or what I say. But nevertheless, I’m doing what’s correct by my engineering license and I can go home knowing that I haven’t harmed or damaged anyone with my decision. And no one can offer a reasonable, logical, and much less legal argument against my decision – at least not to my knowledge.
Thanks to all my prior relations and working with mechanical engineers, I can generate API tank design hand calculations. I have never used this ability to design a tank. I demand a design result from a recognized and experienced engineer. But being able to follow and understand the bases and underpinnings of tank design help out a Chemical Engineer enormously in later making mechanical or process modifications decisions. I highly recommend any Chemical Engineer to follow this principle whenever the opportunity presents itself. Learning and respecting what Mechanical Engineers can do is simply another way to broaden and diversify your capabilities as a professional engineer and dominating your craft.
I’m open to anyone’s opinion and comments on this experience and line of reasoning. I would be particularly grateful if anyone can instruct me if I’ve said something incorrectly or left out some important matter on the subject. We can all learn and improve our engineering product on subjects such as these.
Art Montemayor
I’ll try to make a contribution to this thread because I consider the basic question an important one that keeps repeating itself – in other threads and in other forums. I’ll address this to you, although it also is meant for all readers. I am confident I know the answer; however, I don’t know if I can successfully communicate it correctly or confirm it with my experience. I’ll give it a try, and I hope that Paul Ostand and other experienced engineers that have been through this trial also write a response. Low pressure storage tanks can be lethal and dangerous vessels – even in the pressure ranges of 0 to 15 psig and especially in the ranges of negative pressure (partial vacuum or “external pressure”).
In your example, you say you’re revamping an existing API water tank to include a N2 blanket system or a fixed desiccant chamber in the breathing pipe. You find yourself in a dilemma because you need to fix the set points and “dead band” for the tank’s instrumentation and don’t know how to obtain these. My reaction to the situation is that one should never attempt to make any modification on a vessel – whether pressure or storage – unless the actual design calculations or specifications are in hand or if one can generate (or calculate) the required mechanical specifications that meet the proposed application.
As I’ve stated in previous threads and personal correspondence in the past, an API 650 or 620 storage tank is usually built to conform to operating pressures of 0 – 5 psig and partial vacuums down to 24 inches of water column (WC). I have found this range to be very appropriate and flexible for application to a very large variety of liquid chemicals – with or without N2 blanketing. HOWEVER, the ranges I’ve mentioned aren’t necessarily the ones that a specific tank was designed and built for. Tank fabricators will build an API tank to your purchase specifications and order. It has been my experience in inheriting existing field tanks in the past that most (if not all) tanks were purchase with nothing more than the description of “API storage tank”, period. No engineering specification or guidelines were given to the fabricator – especially a requirement to design to a specific MAWP (maximum allowable working pressure) or MAWV (maximum allowable working vacuum) – nor was the requirement for written design calculations and an API stamp noted. Naturally, the fabricator did exactly as the purchaser indicated (or did not indicate) and supplied just that: an API storage tank (probably one that was already partially built and “on the shelf” for immediate application. The sad result is what I and many others (like you) have had to confront out in the field, trying to make a sound, safe, and economic engineering decision.
Some years ago I decided I was not going to jeopardize my health and life as well as other people’s by taking the attitude of “Just use a setpoint of ____ in W.C. They're all designed to withstand that.” I took a stand with what I thought was sound engineering and demanded that mechanical integrity be proven and documented in all tanks that I applied engineering on. I obtained what I thought was sound logic in the services of an experienced mechanical engineer with whom I worked hand-in-hand in making all vessel revamps. I learned a lot about what can and can’t be done with API storage tanks and the results speak for themselves: no “suck-ins”, stabile and safe operation, credible and reliable documented records, totally reduced emissions, minimal inert gas consumption, and quality product as well as raw material. I’ve done modifications such as umbrella roofs, anchor lugs, double-bottoms, wall re-enforcements, sloped floors, emissions controls, and many others. I would not attempt a revamp on a tank without a minimal of documentation and calculations that confirm the MAWP and MAWV of the vessel. That’s my comment, and I’ll add another directed to your specific first question: No, there is no “minimum pressure, be it as low as a fraction of an inch of water”, that one can believe a mechanically sound ‘atmospheric’ storage tank is capable of withstanding” - at least, not without proving it with checked, accurate, and documented calculations. That’s the very least that any owner can furnish you as an engineer working on their project. You deserve it, and you should have it coming to you. Fair is fair and you can’t compensate for past errors or omissions by taking steps that jeopardize your life and others. It isn’t morally (and now, finally) legally correct.
Paul Ostand has written a lengthy and, in my opinion, a very needed and useful paper on the employment of N2 blanketing. I dare not speak for such a qualified and experienced individual, but he does state the importance of storage tank mechanical integrity in his paper. Part I, under Methods and Requirements, states:
“When considering safety in relation to the gas blanketing system, bear in mind the following. The tank must be capable of operating at the desired pressure, with an appropriate factor of safety. The tank must be protected from vacuum and pressure that might occur outside of the operating pressure range and within safe limits of tank operation.”
So, even though Paul is not writing about API tank design and fabrication, he specifically identifies a pre-requisite for revamping a storage tank: make sure that your tank can withstand the pressures (or vacuums) you intend to impose on it before attempting any revamp.
Agreeably, our engineering logic and sound judgment is countered in the real-life applications where an owner expects his project engineer to correct a previous mistake or existing safety or environmental problem by simply “converting” a vessel to today’s state-of-the-art through the addition of new equipment on a rusted, non-stamped, undocumented piece of junk. I wouldn’t do it until it was proven that the subject vessel is, in fact, a reliable and mechanically sound piece of equipment with defined pressure ratings. I realize that it’s easy for me to assert my position strongly since I’m a consultant and my paycheck does not depend on any one individual liking me, my under-arm deodorant, or what I say. But nevertheless, I’m doing what’s correct by my engineering license and I can go home knowing that I haven’t harmed or damaged anyone with my decision. And no one can offer a reasonable, logical, and much less legal argument against my decision – at least not to my knowledge.
Thanks to all my prior relations and working with mechanical engineers, I can generate API tank design hand calculations. I have never used this ability to design a tank. I demand a design result from a recognized and experienced engineer. But being able to follow and understand the bases and underpinnings of tank design help out a Chemical Engineer enormously in later making mechanical or process modifications decisions. I highly recommend any Chemical Engineer to follow this principle whenever the opportunity presents itself. Learning and respecting what Mechanical Engineers can do is simply another way to broaden and diversify your capabilities as a professional engineer and dominating your craft.
I’m open to anyone’s opinion and comments on this experience and line of reasoning. I would be particularly grateful if anyone can instruct me if I’ve said something incorrectly or left out some important matter on the subject. We can all learn and improve our engineering product on subjects such as these.
Art Montemayor
#7
Posted 08 November 2005 - 10:18 AM
Thanks to Messrs. Ostand and Montemayor for your most helpful replies. You've done as good a job of answering the question as I believe is possible.
My suggestion to the API is that a design pressure and vacuum rating be required to be on the nameplate of the tank (similar to ASME coded pressure vessels). That would go far to avoid the uncertainty that exists regarding this subject.
I'd also like to make a request to Mr. Montemayor. I know from previous posts that you are knowledgable (and somewhat passionate) about the subject of vessel design, including demisters. I had what I thought was a challenging question about demister design that I posted in this forum on June 6 of this year, hoping to draw responses from experts on the subject. Unfortunately, the posting failed to catch much attention, and solicited only a single response. I would invite you (and any other interested persons) to revisit this posting and to reply if appropriate.
Thank you,
Doug
My suggestion to the API is that a design pressure and vacuum rating be required to be on the nameplate of the tank (similar to ASME coded pressure vessels). That would go far to avoid the uncertainty that exists regarding this subject.
I'd also like to make a request to Mr. Montemayor. I know from previous posts that you are knowledgable (and somewhat passionate) about the subject of vessel design, including demisters. I had what I thought was a challenging question about demister design that I posted in this forum on June 6 of this year, hoping to draw responses from experts on the subject. Unfortunately, the posting failed to catch much attention, and solicited only a single response. I would invite you (and any other interested persons) to revisit this posting and to reply if appropriate.
Thank you,
Doug
#8
Guest_rey_*
Posted 23 November 2005 - 03:18 PM
Hi! with regards to your question here is my idea in addition, API-2000 is for determination of storage tank inbreathing-outbreathing rates for the breather valve sizing. I don't think they're really intended as any sort of pressure relief device as they are used for normal blanketing operations and sized based on the estimated flowrates in the API-2000 tables. I don't remember the API-2000 completely but i think the major factors in calculation are tank size, pump in/out rate (accounting for possible pulling a vacuum in an atmospheric tank) and i think sometimes maximum venting due to fire for conservative estimates (i know it seems to contradict my earlier statement about it as a relief device).
so far, i have prepared tank datasheets not taking the fire case into account though. just for normal blanketing purpose.
as for maximum design pressure of an atmospheric tank, I'm not a ME but i think it would be conservative to assume maximum tank design pressure as Atmospheric pressure + Max Liquid Head. That is what i use for rating of the pump maximum suction pressure in place of the design pressure for pressure vessels as MAWP is not yet usually available until construction phase and maybe not available at all for atmospheric tanks. This is from the FEED stage standpoint.
as for the breather valve setpoints, i think it is not really safe to rely on the setpoints provided by others especially online but for comparison purposes, i think i indicated about -50 to 150 mmH2O in a datasheet before but this is project specific and based on client standards so unless we have the same client, i don't think you should use it. i think it shouldn't be more than a few kPa from atmospheric though and i don't think it'd reach partial vaccuum as your tank roof may have collapsed by then. Maybe your company has standards or if there are previous breather valve installations in your refinery, maybe you should check the setpoints on those too. I think its very likely that some of your tanks are already provided with blanketing systems one way or the other not necessarly using automatic breather valves but maybe a PCV setup. I think the setpoints should be somewhat similar in your old installations if any.
Good luck.=)
so far, i have prepared tank datasheets not taking the fire case into account though. just for normal blanketing purpose.
as for maximum design pressure of an atmospheric tank, I'm not a ME but i think it would be conservative to assume maximum tank design pressure as Atmospheric pressure + Max Liquid Head. That is what i use for rating of the pump maximum suction pressure in place of the design pressure for pressure vessels as MAWP is not yet usually available until construction phase and maybe not available at all for atmospheric tanks. This is from the FEED stage standpoint.
as for the breather valve setpoints, i think it is not really safe to rely on the setpoints provided by others especially online but for comparison purposes, i think i indicated about -50 to 150 mmH2O in a datasheet before but this is project specific and based on client standards so unless we have the same client, i don't think you should use it. i think it shouldn't be more than a few kPa from atmospheric though and i don't think it'd reach partial vaccuum as your tank roof may have collapsed by then. Maybe your company has standards or if there are previous breather valve installations in your refinery, maybe you should check the setpoints on those too. I think its very likely that some of your tanks are already provided with blanketing systems one way or the other not necessarly using automatic breather valves but maybe a PCV setup. I think the setpoints should be somewhat similar in your old installations if any.
Good luck.=)
#9
Guest_rey_*
Posted 23 November 2005 - 03:25 PM
oh additionally, it may interest you that the breather valve pressure setpoints were not used for determining the valve load. The loading is just based on the tables provided in API-2000 depending on the factors stated above, you find the value in the table where your parameters indicate and that is the inbreathing outbreathing rate.
This is very different from pressure relief valve sizing where the relieving pressure is used to calculate relief load and valve size.
This is very different from pressure relief valve sizing where the relieving pressure is used to calculate relief load and valve size.
#10
Guest_Saurabh Agarwal_*
Posted 28 March 2006 - 05:42 PM
Hi, I am tryign to size a pressure relief valve and have stumbled on the issue of over pressure.
I have been able to determine the flow capacity required for a pressure relief valve using API 2000. Now I looked up at manufacturers table (Groth) and it states the flow capacity of the valve at 100% over pressure, and to calculate it at any other over pressure it states to use (Flowing Pressure - Set Pressure)/Set Pressure. If the set pressure for the valve to open is 6.0 inch W.C what is the flowing pressure. Is it that pressure in the pipe to which the tank vents, or is it the actual pressure in the tank. If this is pressure in the pipe to which the tank vents then the equation implies this pressure to be higher than that in the tank, in which case there should be a back pressure in the tank and the valve should not be able to provide relief rather increase the tank pressure even further.
Any comments would be most valuable.
Thanks
Saurabh
I have been able to determine the flow capacity required for a pressure relief valve using API 2000. Now I looked up at manufacturers table (Groth) and it states the flow capacity of the valve at 100% over pressure, and to calculate it at any other over pressure it states to use (Flowing Pressure - Set Pressure)/Set Pressure. If the set pressure for the valve to open is 6.0 inch W.C what is the flowing pressure. Is it that pressure in the pipe to which the tank vents, or is it the actual pressure in the tank. If this is pressure in the pipe to which the tank vents then the equation implies this pressure to be higher than that in the tank, in which case there should be a back pressure in the tank and the valve should not be able to provide relief rather increase the tank pressure even further.
Any comments would be most valuable.
Thanks
Saurabh
#11
Posted 28 March 2006 - 07:59 PM
Sorry to say but in low pressure (API style) tanks using conservation venting or just plain pressure venting, the pressure in the tank will be higher (or lower) than the set pressure. This is the flowing pressure you speak of. For pressure, the vapor has to exit the tank and get into a pipe (or maybe just a nozzle) and through some pressure relieving device and maybe some additional piping. You have to overcome several resistances to flow. To achieve flow, the pressure in the tank will have to be greater than what you would think to set the pressure relief for. For vacuum relief, the opposite is true. Say you start from atmosphere. The air has to get into the tank some how. The air may have to pass through some piping (may not), then through some vacuum relieving device and possibly some minimal piping or just a nozzle befire getting into the tank. Again, you have to overcome several resistances to flow. Since you start at atmospheric pressure, you have to have some vacuum in the tank to create flow and this will greater than what you may set your vacuum relief for.
I just got finished doing some conservation vent sizing for tanks with nitrogen blankets and had to settle for almost 7" W.C. in my tank with a set pressure of 6" W.C. for my pressure relief device. It is a good thing the design pressure is significantly higher than this. I had to set the vacuum for -1.5" W.C so I would not exceed my -2" W.C. design vacuum during design flow.
These set points and resulting end pressures will be a function of the actual type of device you pick. I suggest you call Groth or Protecoseal and discuss the situation with them. My Protectoseal rep was extremely helpful in helping me choose the correct conservation device to use in my application. They don't mind helping you, trust me.
I just got finished doing some conservation vent sizing for tanks with nitrogen blankets and had to settle for almost 7" W.C. in my tank with a set pressure of 6" W.C. for my pressure relief device. It is a good thing the design pressure is significantly higher than this. I had to set the vacuum for -1.5" W.C so I would not exceed my -2" W.C. design vacuum during design flow.
These set points and resulting end pressures will be a function of the actual type of device you pick. I suggest you call Groth or Protecoseal and discuss the situation with them. My Protectoseal rep was extremely helpful in helping me choose the correct conservation device to use in my application. They don't mind helping you, trust me.
Similar Topics
Steam Pressure In Heat ExchangerStarted by Guest_mvanrijnbach_* , 15 Apr 2025 |
|
![]() |
||
Vacuum RecoveryStarted by Guest_Paper_* , 25 Feb 2025 |
|
![]() |
||
![]() Valve Cavity - Pressure Relief ValveStarted by Guest_CS10_* , 20 Feb 2025 |
|
![]() |
||
Pressure Of An Isolated Flow In PipeStarted by Guest_phoroogh_* , 30 Jan 2025 |
|
![]() |
||
![]() Maximum Allowable Accumulated PressureStarted by Guest_mahmooddalvi09_* , 30 Jan 2025 |
|
![]() |