|
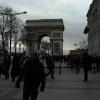
Damage In Molecular Sieves
#1
Posted 20 April 2012 - 01:40 PM
Anyone have any reference, known as quantify the expansion?
I appreciate any collaboration.
#2
Posted 21 April 2012 - 05:03 AM
Refer the link below where the regeneration cycle time including heating and cooling is mentioned for molecualr sieve adsorbers.
http://www.cheresour...sieve-adsorber/
Another link regarding regeneration of molecular sieve adsorber is:
http://www.cheresour...e-bed-adsorber/
From both links it is clear that the typical cooling cycle time during the regeneration step is half the heating cycle time.
Also note that bed deformation and adsorbent breakdown is also contributed by high operating pressures of the molecualr sieve tower. As mentioned in the book "Fundamentals of Natural Gas Processing" by Arthur J. Kidnay and William R. Parrish, higher pressures increase the amount of water and hydrocarbons that condense at the top of the bed and fall back onto the adsorption bed. This unavoidable refluxing is a major cause of bed aging, as it leads to adsorbent breakdown and subsequent fines agglomeration.
Hope this helps.
Regards,
Ankur.
Edited by ankur2061, 21 April 2012 - 05:04 AM.
#3
Posted 15 May 2012 - 06:11 AM
#4
Posted 16 May 2012 - 12:33 PM
#5
Posted 16 May 2012 - 02:31 PM
If there is evidence of potential adsorbent bed thermal shock damaging some adsorbents, I'd like to know about it. I know silica gel is relatively fragile towards dusting, and that is why I never use it anymore; I quit using it about 40 years ago. All I would use today is Activated Alumina or Molecular Sieves.
#6
Posted 16 May 2012 - 03:18 PM
#7
Posted 16 May 2012 - 07:36 PM
What I described in my previous post are all gas drying operations with adsorption units - not liquid dehydration. I have also done liquid drying - LPG and Butane - but there are more steps in the regeneration step than just a blowdown of the residual liquid in the bed. Adsorbing water from a liquefied gas is more complex.
I want to make this a clear and well-understood topic because I don't want members to think that the adsorption of water from a gas is the same operation as the adsorption of water from a liquid - especially a compressed liquefied gas. You haven't furnished us with much basic data except that you are carrying out simultaneous sweeterning and dehydration of liquid propane with an adsorption unit. We don't know the capacity, the process conditions, or the detailed cycle steps that are incorporated into your unit - as well as the number of beds involved in the unit and how you are regenerating them.
I believe we all know that if you are treating the propane in the compressed liquid phase, you are going to undergo a cooling phase of the spent bed when you blow it down for preparation of the heating step. How you do this depends on the original design of the unit and the type of regeneration system you are using. Please furnish us with a detailed schematic of your unit showing the beds, the switching valves, the regeneration system complete with heater and/or blower used. If you are indeed using Mol Sieves, then you shouldn't have any temperature problems - however, the preparation step prior to heating the bed is, in my opinion, an important one because you want all liquid fluid to be thoroughly purged and evacuated from the bed before applying the high regeneration heat. You don't want to evaporate liquids within the adsorbent bed if you can avoid it. Your regeneration heat should be that required for sensible heating and only latent heat for the adsorbed components - the water and dissociation heat for the CO2, H2S, and mercaptans (if any). Of course, you need additional heat for the unit's steel, adsorbent, insulation, etc.
If you have any hydrocarbon "heavies" in the liquid Propane, these may be a cause of the problems you are bringing up. A detailed description of the NEMA cycle for the unit is needed to appreciate the various steps required for a successful regeneration.
#8
Posted 17 May 2012 - 09:02 PM
Adsorption
Draining
Cold Fuel Gas circulation
Heating
Cooling with Fuel Gas
Cooling with Propane
Filling
Stand-by & Switch
My concern is after cooling with fuel gas the temperature inside the molecular sieve is 284°F and the vapor of pressure of the propane is very large and potentially causing damage to the molecular sieve because one of the functions of liquid propane gas is cooled displace fuel that is in the pores of the sieve.
The type of sieve is aluminosilicate.
#9
Posted 18 May 2012 - 12:41 PM
Thank you for the additional basic data that I requested. We still don't know the capacity, the process conditions, the regeneration system, or the number of beds involved in the unit and how you are regenerating them - so I have had to make a bunch of assumptions in putting together a workbook to use as a working tool to find possible causes to what you are witnessing. Please refer to the attached and make as many pertinent comments, corrections, and questions as you can by inserting “call outs” on the sketches furnished. Revise the workbook if you make changes on it by attaching a Rev # to it. That way, we can keep track of the comments as we progress to a resolution. Note that I designate the "open" or "closed" position of all valves. You can easily un-protect the worksheet and make changes if you need to do that.
Please note that I do not recommend what you are describing: “after cooling with fuel gas the temperature inside the molecular sieve is 284 °F”. I always cool down the adsorption beds as much as I can – hopefully to the same temperature as the incoming raw fluid that is being treated. This means that you should be cooling down the bed to approximately 90 °F (if that is the temperature of the raw propane).
I hope this helps to clear up a lot of unknowns and speeds us towards a resolution.
Attached Files
#10
Posted 27 May 2012 - 10:55 PM
Drainage: Propane vapors are used to recover propane spongy.
Cold fuel gas flow: this is done with the purpose of recovering the liquid propane.
Heating: using hot fuel which is heated used a heater. In this step is removed the water and H2S of the molecular sieve.
Cooling with fuel gas : Is the first step in which the molecular sieve is cooled
Cooling with liquid propane
Filled with liquid propane
#11
Posted 28 May 2012 - 10:22 AM
I don’t understand part of your response. For example, I don’t know what is meant by the phrase, “the liquids should do everything possible to avoid contaminating the product described above liquid”.
When you detail the steps in the regeneration portion of the operation, are you quoting the operating manual for the adsorption unit? Who designed and built the adsorption unit? Surely, there is an operating and maintenance manual that details out all of the critical operational steps to be employed in the operation and what to expect in keeping the unit well-maintained.
I also have problems in interpreting the steps described and I am offering my comments, in RED, on what I normally expect and design for in an adsorption cycle of this type:
Drainage: Propane vapors are used to recover propane spongy.
(What is meant by “propane spongy”? Normally, the vessel is drained of saturated propane liquid by opening a bottom outlet valve and letting the liquid propane’s own vapor pressure force the liquid out to a lower pressure system or vessel. Is this what is meant?)
Cold fuel gas flow: this is done with the purpose of recovering the liquid propane.
(Recovering the residual liquid propane is only one of the objectives in this step. Of greater importance is the total evacuation of all residual liquid propane from the adsorption vessel and the establishment of a hydrocarbon gas atmosphere (“fuel” gas, in this case) inside the vessel prior to starting the heat up. It is important to evacuate the residual liquid propane for reasons already clearly indicated in prior posts.)
Heating: using hot fuel which is heated used a heater. In this step is removed the water and H2S of the molecular sieve.
(The introduction of hot (500 – 700 oF) regen gas (“fuel” gas, in this case) is done ONLY after ALL residual liquid propane has been purged from the vessel (and recovered) and the adsorption bed has a 100% atmosphere of fuel gas. The adsorption bed and all internals are heated to approx. 500 – 700 oF in order to expel all captured contaminants in the bed out of the vessel with the exiting hot regen gas.)
Cooling with fuel gas : Is the first step in which the molecular sieve is cooled.
(After successfully heating the adsorption bed to 500 – 700 oF, the next step is to cool the bed down to an acceptable ambient temperature that is conducive with the normal vapor pressure of the liquid propane to be introduced afterwards. Normally, depending on the specific unit design, the hot bed is cooled down to approx. 90 oF – using the same regen gas that was used to heat it, except that it is in a cooled state. Note that the bed is cooled with the regen gas – not with the subsequent introduction of the raw liquid propane.)
Cooling with liquid propane
(Once the regenerated bed has been cooled down to approx. ambient temperature, the regen gas has to be evacuated from the vessel so that the next adsorption of raw liquid propane can take place in the vessel. This is done by introducing liquid propane into the vessel while the regen gas has stopped flowing. This step is to slowly purge out the remnants of the regen gas and establish a 100% liquid propane fill in the vessel. Since the regen gas normally used is at a lower pressure than the vapor pressure of liquid propane, there is a refrigerating effect that takes place when the initial liquid propane is “cracked” into the vessel and it starts to flush out the regen gas and then fills the vessel. This temporary and relatively small amount of refrigeration helps to cool down any internals and steel shell portions of the vessel that may still be a little warm from the heat-up portion of the cycle.)
Filled with liquid propane
(As described above, the vessel is slowly filled 100% with raw, liquid propane and should be ready to be put into adsorption service for the next cycle)
You have not responded to my comment where I do not recommend what you are describing: “after cooling with fuel gas the temperature inside the molecular sieve is 284 °F”. I do not understand how that high a temperature can be described as being cool. Without knowing all the basic data requested and having no answers to my queries or a response to the detailed Excel workbook that I have put together for this thread, I have no further comments to add.
I believe I not only have described and commented on my interpretation of the regeneration portion of the Adsorption cycle, but the detailed sketches and notes furnished in my workbook describe the operation in as great a detail as I can, given the little amount of basic data that has been presented.
#12
Posted 30 May 2012 - 01:00 PM
Thanks Mr. Art your comments are accurate, I appreciate your attention to the subject
Dear Art basically the question is what is the effect on the molecular sieve if obvious the step cooling with fuel gas. I have conducted research and thesis on the subject exists. There is an effect called "sintering" is a physical process that causes a loss of the solid surface, occurring when operating in the presence of large amounts of energy as heat, high temperatures or abrupt changes in temperature. This process may occur in specific areas of solid or throughout its volume. Sintering is a complex phenomenon, and so far it is difficult to predict the speed with which change the structural characteristics of the adsorbent.
Draining
After the adsorption phase, the Molecular Sieve Adsorber switches in regeneration mode The vessel is depressurized to the pressure of the vapor propane from Depropanizer overhead and drained to the Product Receiver. A Pressure Switch Low at Adsorber top indicates the end of the depressurization step.
Cold Fuel Gas circulation
Cold HP Fuel Gas from Plant Fuel Gas System flows downwards through the Adsorber in order to remove remaining propane (spongy propane) and avoid HP Fuel Gas System contamination during the next step.
Heating
The hot regeneration Fuel Gas at 368 psig/554°F flows downwards in the Adsorber under flow control providing enough energy to desorb the water and H2S from the molecular sieve.
Cooling with Fuel Gas
Cold Fuel Gas at 380 psig flows downwards through the vessel to perform a first cooling of the Adsorber from 554°F to 284°F. This step allows reducing the aggressive expansion of liquid propane due to its vaporization during final cooling which will damage the molecular sieve. Moreover, first cooling is stopped at 284°F to avoid adsorption of water and H2S contained in Fuel Gas by the sieve.
Cooling with Propane and filling
The liquid propane at 250 psig/115.1°F is heated while flowing upwards through the vessel but remains dry as no water is present on the sieve.Spongy propane; is the propane that is inside the pores of the molecular sieve. (belong to cold fuel gas circulation and not to draining step)
Mr. Art. if you need any additional information or details, please send me your email and information will be sent gladly.
Similar Topics
![]() ![]() Molecular Sieve UnitStarted by Guest_Sufy_* , 26 Feb 2025 |
|
![]() |
||
Molecular Sieve Regeneration At High PressureStarted by Guest_Victor_process_Engineer_* , 07 Jan 2025 |
|
![]() |
||
Low Molecular Flaring (H2 Rich Flare Gas)Started by Guest_TechExpert_* , 23 Dec 2023 |
|
![]() |
||
Molecular SievesStarted by Guest_KOSTAS933_* , 21 Apr 2023 |
|
![]() |
||
![]() Channeling In Molecular Sieve During AdsorptionStarted by Guest_Mateo_1974_* , 06 Jun 2022 |
|
![]() |