i have doing some reasearch work on welded plate heat exchangers for last 20 days or so. after going thorugh their design versatility ,application versatility ,construction etc. i haven't found out any limitations or major disadvantages.are there any major disadvantages of such type of plate heat exchangers
?.
|
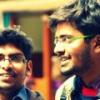
Welded Plate Heat Exchangers
Started by ayche, Jul 18 2012 02:07 PM
5 replies to this topic
Share this topic:
#1
Posted 18 July 2012 - 02:07 PM
#2
Posted 18 July 2012 - 02:48 PM
Ayche:
Welded plate heat exchangers (also called brazed heat exchangers) are very specialized and unique exchangers that are employed only when one has no other option with regards to potential leaks or spills. I am confounded by your statement that you have found no limitations or major disadvantages in applying them.
Some advantages of using welded exchangers are:
Some disadvantages are:
There may be other advantages / disadvantages, but I will wait for other, more experienced and capable members to contribute their comments. The main point here is that there ARE DISADVANTAGES – enough of them to make this type of exchanger a “minority group” member in the heat exchanger realm. I have never heard of one being applied within an oil refinery, for example.
Welded plate heat exchangers (also called brazed heat exchangers) are very specialized and unique exchangers that are employed only when one has no other option with regards to potential leaks or spills. I am confounded by your statement that you have found no limitations or major disadvantages in applying them.
Some advantages of using welded exchangers are:
- There are no leaks. This resolves the issue of handling toxic or hazardous fluids;
- They are very compact and take up less space with a small footprint;
- There is presumably no maintenance;
- They tend to be more efficient (with certain caveats).
Some disadvantages are:
- If your fluid gets contaminated and plugs the exchanger, you are in deep trouble;
- You must ensure that both fluids are very clean – always;
- They are limited in their ability to take thermal stresses because of an inability to have expansion joint capabilities; they are rigidly welded together with little or no ability to expand;
- Some composition changes in the two flow streams may give problems because one cannot change or modify the internals;
- They tend to be more expensive; their design is special and usually proprietary;
- If there is corrosion or erosion within the unit, you will not be aware of it until performance drops and the matter can only be resolved by total replacement.
- Some designs cannot handle 2-phase development inside the unit, so any condensation taking place would give problems in performance;
There may be other advantages / disadvantages, but I will wait for other, more experienced and capable members to contribute their comments. The main point here is that there ARE DISADVANTAGES – enough of them to make this type of exchanger a “minority group” member in the heat exchanger realm. I have never heard of one being applied within an oil refinery, for example.
#3
Posted 18 July 2012 - 05:08 PM
O.K., full disclosure. I'll discuss Alfa Laval's technology on the subject because I worked there for many years and know their technology the best, but there are others too.
Art has discussed the classical brazed plate heat exchanger in detail for you above. "Welded Plate Heat Exchangers" is a relatively broad terms and as you've no doubt found, there are several different configurations and options in this class. So, I'll speak from some of my experience.
Most often, welded plate heat exchangers are not accessible for mechanical cleaning (such as the brazed units that Art discusses). To be sure, if you're going to install one of these any where and there is any chance of solids...better install a strainer or a low cost heat exchanger (as brazed units usually are). Many of the inherent mechanical limitations of the brazed units have been addressed in this type of technology:
Alfa Laval AlfaRex
I've applied this very unit in many applications over the years. It has to be justified based on it's cost, but if the criteria are:
No or low solids present (can be reasonable handled by a strainer)
Significant pressure / temperature / operation cycling is expected
High temperature or pressure
Fluids incompatible with gaskets
Flows above a standard brazed unit (these units are available in 4" and 8" connections)
The mechanical change that were made with these particular units was that instead of being welded along the x, y, and z axes, each plate is only welded onto the plate underneath it (only x and y directions). The result is an extremely robust plate pack that acts something like an accordion. I saw one of these burst tested and the head of the tightening bolts was the first part to fail (rather than a plate or one of the laser welds).
The AlfaRex is one of the most robust plate heat exchangers that you'll find. You can hit it with pressure and temperature cycles over and over (many, many times) before it will eventually fail (I've seen them installed for many years in such applications).
Moving on to another class of welded plate heat exchangers, we have what I'll call the welded block style. Alfa Laval's trade name for this type of unit is the Compabloc. Over the past 5-8 years, Alfa Laval has indeed begun installing these types of units in refineries all over the world as a means of maximizing energy recovery.
You can read more about this unit here:
Compabloc
The welded block type unit utilizes lined, carbon steel panels around a welded "heart" of plates that are welded together. These units are welded in all three dimensions meaning that these types of units can be more susceptible to cycling operations. The significant advantage of these welded units is the ability to open them and access the plate "heart" for mechanical cleaning. Also, if a plate were to fail, individual channels can be blocked off much like you would plug a tube in a shell and tube unit.
These block type heat exchangers are among one of my favorites because of their versatility. They're excellent at liquid-liquid heat transfer (especially if one of the fluids is viscous) and they also make very good condensers and reboilers (in relatively clean services). Attached is an article that I authored several years ago on why they make excellent condensers.
There are other welded type plate heat exchangers, but these are two of my favorites....but they're very different, each with their own strengths.
Art has discussed the classical brazed plate heat exchanger in detail for you above. "Welded Plate Heat Exchangers" is a relatively broad terms and as you've no doubt found, there are several different configurations and options in this class. So, I'll speak from some of my experience.
Most often, welded plate heat exchangers are not accessible for mechanical cleaning (such as the brazed units that Art discusses). To be sure, if you're going to install one of these any where and there is any chance of solids...better install a strainer or a low cost heat exchanger (as brazed units usually are). Many of the inherent mechanical limitations of the brazed units have been addressed in this type of technology:
Alfa Laval AlfaRex
I've applied this very unit in many applications over the years. It has to be justified based on it's cost, but if the criteria are:
No or low solids present (can be reasonable handled by a strainer)
Significant pressure / temperature / operation cycling is expected
High temperature or pressure
Fluids incompatible with gaskets
Flows above a standard brazed unit (these units are available in 4" and 8" connections)
The mechanical change that were made with these particular units was that instead of being welded along the x, y, and z axes, each plate is only welded onto the plate underneath it (only x and y directions). The result is an extremely robust plate pack that acts something like an accordion. I saw one of these burst tested and the head of the tightening bolts was the first part to fail (rather than a plate or one of the laser welds).
The AlfaRex is one of the most robust plate heat exchangers that you'll find. You can hit it with pressure and temperature cycles over and over (many, many times) before it will eventually fail (I've seen them installed for many years in such applications).
Moving on to another class of welded plate heat exchangers, we have what I'll call the welded block style. Alfa Laval's trade name for this type of unit is the Compabloc. Over the past 5-8 years, Alfa Laval has indeed begun installing these types of units in refineries all over the world as a means of maximizing energy recovery.
You can read more about this unit here:
Compabloc
The welded block type unit utilizes lined, carbon steel panels around a welded "heart" of plates that are welded together. These units are welded in all three dimensions meaning that these types of units can be more susceptible to cycling operations. The significant advantage of these welded units is the ability to open them and access the plate "heart" for mechanical cleaning. Also, if a plate were to fail, individual channels can be blocked off much like you would plug a tube in a shell and tube unit.
These block type heat exchangers are among one of my favorites because of their versatility. They're excellent at liquid-liquid heat transfer (especially if one of the fluids is viscous) and they also make very good condensers and reboilers (in relatively clean services). Attached is an article that I authored several years ago on why they make excellent condensers.
There are other welded type plate heat exchangers, but these are two of my favorites....but they're very different, each with their own strengths.
Attached Files
#4
Posted 19 July 2012 - 12:09 AM
sir Art Montemayor
i m sorry i couldnty make myself very clear regarding my query.
sincere apologies.
actually my enquiry was specifically about the bloc welded type plate heat exchangers ,the ones which can be opened and can be mechanically cleaned very easily.
brazed plate heat exchanger is not my topic of interest as i have been specifically told to work on plate and shell and bloc welded heat exchangers.
so i want to know whether these bloc welded and shell and plate have any major disadvantages(not the brazed ones)
sir chris
u discussed about compabloc. are there any major disadvantages. ?
i m sorry i couldnty make myself very clear regarding my query.
sincere apologies.
actually my enquiry was specifically about the bloc welded type plate heat exchangers ,the ones which can be opened and can be mechanically cleaned very easily.
brazed plate heat exchanger is not my topic of interest as i have been specifically told to work on plate and shell and bloc welded heat exchangers.
so i want to know whether these bloc welded and shell and plate have any major disadvantages(not the brazed ones)
sir chris
u discussed about compabloc. are there any major disadvantages. ?
#5
Posted 19 July 2012 - 06:02 PM
Well, as mentioned, it's best suited for continuous service. The operating pressures on each side should not be too close to one another to avoid flexing on the liners in the corners. In other words, you don't want the operating pressures to cross each other inside the heat exchanger. They're a little expensive to manufacture, but if you compare $ / Btu recovered with other options, I think you'll see that they are pretty good options.
As Art always says, there's a trade-off for everything. Check for some references in your area with Alfa Laval. I'd be surprised if they don't have any.
As Art always says, there's a trade-off for everything. Check for some references in your area with Alfa Laval. I'd be surprised if they don't have any.
#6
Posted 20 July 2012 - 12:16 AM
sir
Chris Haslego
thank you so much for the information.so i suppose as such there are no major limitations as sch when we use bloc welded heat exchangers
and in your article for plate and frame heat exchangers th graphs given.are they valid for gasketed as well as welded plate and frame.?
Chris Haslego
thank you so much for the information.so i suppose as such there are no major limitations as sch when we use bloc welded heat exchangers
and in your article for plate and frame heat exchangers th graphs given.are they valid for gasketed as well as welded plate and frame.?
Similar Topics
Steam Pressure In Heat ExchangerStarted by Guest_mvanrijnbach_* , 15 Apr 2025 |
|
![]() |
||
Heat Exchanger Steam FlowStarted by Guest_aliebrahem17_* , 25 Nov 2024 |
|
![]() |
||
Discussion - Predict Storage Tank Heat Transfer Precisely By Jimmy D KStarted by Guest_raj shekhar_* , 25 Mar 2025 |
|
![]() |
||
Cross Over Temperature In Countercurrent Heat ExchangerStarted by Guest_panoska_* , 18 Feb 2025 |
|
![]() |
||
Aspen Hysys - Blowdown Utility Heat Flux MethodStarted by Guest_yuvi.ardekar1999@gmail.com_* , 27 Feb 2025 |
|
![]() |