|
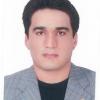
Multiple Psvs Set Pressure
#1
Posted 13 August 2012 - 05:03 AM
As per API 520 part I,in terms of multiple valve installations:
the first psv should be set at 100%MAWP
the additional psv should be set at 105%MAWP
What if the both PSVs set at 100%MAWP?
regards
Rohollah
#2
Posted 13 August 2012 - 05:22 AM
Due to cometition of the PSV's to open simultaneously at the set point and because it is almost impossible to execute symetrical piping of PSV's inlet lines, It will lead to chattering the PSV's and unstable relief operation. Indeed, stagerring the PSV's set points will allow to manage various relief loads without unstable relieving operation.
Fallah
#3
Posted 03 September 2012 - 01:25 AM
So as fallah sad "Various relief loads can be managed without unstable relieving operation i.e. opening and closing repeatedly, which may lead to mechanical damage to PSV seat and other parts as well.
Regards
Pravin
#4
Posted 04 September 2012 - 10:36 AM
In my experience I have designed a system protected by 5 PSVs with a T API orifice and for piping stress point of view there was as huge difference if PSVs where staggered or not.
#5
Posted 05 September 2012 - 12:42 AM
It is not common to set multiple PSV's at the same pressure in order to be opened similtaneously at that set point. It needs the valves to be identical and their inlet lines pipings to be absolutely symetrical, in fact in real world especially for mare than two PSV's, if may not impossible is hardly practicable. So, it is strongly recommended to set multiple PSV's in staggered position.
Fallah
#6
Posted 05 September 2012 - 02:47 AM
Multiple relief valves with staggered set pressures are as such recommended to
- Increase life of the valves
- Minimise leakage through the valves.
Regards,
Jatin
#7
Posted 05 September 2012 - 05:59 AM
I do agree with you, it is not advisable and not common to set multiple PSVs at the same set pressure. Nevertheless, I have seen experienced subcontractors to do so.
Under the final user point of view, we have highlighted to subcontractor that staggered set point should be considered, because of the reason stated above:
-Increase life of the valves
-Minimise leakage through the valves.
-Manage various relief loads without unstable relieving operation.
-Stress design
Nevertheless, it is my understanding that the symmetry is not the problem while sizing PSV inlet lines, but the pressure drop. As long as the pressure drop is below 3% of set pressure on the inlet line at relieving conditions (API 520 part II design criteria) on each PSV, chattering should not occur.
Lack of symmetry may lead to maldistribution of flows, but as long as the pressure loss in each line at rated flow condition is below of the blowdown of the PSV the valve should not close (which is usually higher than 3%set pressure).
Usually the selected orifice area is higher than the required area and this difference on flow can be handle by the rated flow of PSVs.
it is my understanding that valves can be designed with the same set pressure as long as the above points are reviewed, even if inlet lines are not symmetrical. Please note that it is usually acceptable to have 5% of maldistribution on equipment in parallel and with 3% set pressure loss this should not be a big difference
But this really complicates the engineering and consequently staggering is the easy way to solve the problem.
kind regards
#8
Posted 05 September 2012 - 07:19 AM
Your statements seem are to be theoretically right, but please consider multiple PSV's with the same set pressure to be installed to cover various relief loads of different scenarios. Then, e.g. for lowest relief load where it might even the orifice area of one PSV be larger than required you can imagine what would be happened: It creates continuous leakage from all PSV's, likely along with chattering and seat damage, till the pressure of the system drops low enough leading the PSV's to be closed.
Fallah
#9
Posted 05 September 2012 - 10:24 AM
I understand your point of view, I explain my understanding with the following example:
-A vessel requires two "T" orifice PSV for protection.
-Two relieving scenarios are credible for design: Fire scenario and Control valve failure.
-Flow rate from fire scenario is significantly lower than control valve scenario
-For Fire scenario only one valve is required to open.
-For control valve failure the two PSV are required to open.
Consequently, if fire scenario occurs the increase of pressure will open both valves, rated flow will be observed through both PSVs and the vessel will go below set pressure and the PSV might be closed.
This might happen because the flow relieved by the the two PSVs is twice the value of the required flow under Fire scenario.
Then the vessel will get pressurized again, because it is still under fire and chattering might occur.
I agree that this might happen if the different scenarios are applicable for a PSV design and they have different flowrates .
But then, the reason of chattering is not the lack of symmetry on the inlet lines, but the wide difference in relieving flow between the two scenarios and its relation with the selected capacity of PSV.
If the two scenarios had similar flow rates, the chattering should not happen.
Nevertheless, I have to clarify that the best practice is to staggered the set pressure.
kind regards
Edited by Mark-TR, 05 September 2012 - 11:56 AM.
#10
Posted 06 September 2012 - 12:29 AM
But then, the reason of chattering is not the lack of symmetry on the inlet lines, but the wide difference in relieving flow between the two scenarios and its relation with the selected capacity of PSV.
Mark-TR,
At first thanks a lot for your kind and effective contribution in current discussion...
I am agree with you that lack of symmetry of inlet piping isn't only reason of chattering of two identical PSV's, let say 2*50%, with the same set pressure. In other word, it is a needed but not adequate condition for prevention of PSV chattering at mentioned configuration.
In fact, when the possible difference in the onset of relief operation of two valves till 6% due to the error in set pressure accuracy of up to 3% (allowable tolerance), will combine with the difference in inlet pressure loss due to lack of piping symmetry; the likelihood of PSV chattering will rise and, as you mentioned, will forced us to prefer staggered situation in set pressures.
Fallah
#11
Posted 07 May 2013 - 12:48 PM
As a result of discussion I have come up to this idea that, it is not advisable and not common to set multiple PSVs at the same set pressure.
On the other hand I have seen multiple and supplemental PSVs with the same set pressure.
How can it be justified?
Regards
Rohollah
#12
Posted 08 May 2013 - 03:38 AM
Rohollah,
Staggering set pressure of the multiple PSVs is a general practice which is highly recommended by API/ASME. There might the cases be such that not to follow mentioned practice would lead to no problem in PSVs function/operation standpoints. The key point through which getting equal set pressures for multiple PSVs can be justified is stable operation of them from relieving start to full closed duration. For example, if there would be only one scenario for multiple PSVs and the the pressure drop is well below 3% of the set pressure at the inlet line of each PSV at relieving conditions then equal set pressures could be acceptable, but most designers might not want to bother theirselves to find such exceptions and usually follow such general practice for all multiple PSVs.
The matter for supplemental PSV is another story and it could be set at 110% of the MAWP of the relevant vessel to cover relieving capacity for an additional hazard created by exposure to fire.
Edited by fallah, 08 May 2013 - 03:42 AM.
#13
Posted 23 June 2013 - 11:21 PM
i would like to raise one more query which has bothering me for some time.
Lets take the case described by Mark-TR
-Flow rate from fire scenario is significantly lower than control valve scenario
-For Fire scenario only one valve is required to open.
-For control valve failure the two PSV are required to open.
For fire case the PSV set @ 100% set pressure will pop open, but for full opening of this valve, there would be an increase in system pressure by 10-21% (accumulation). which will result in pressure of 121% in system before PSV reaches full capacity.
Now my question is if the system pressure will reach either 110% or 121% depending on scenario, how is that the second PSV which is set @ 105 % doesnt open..
Hope my query is clear enough..
Reagrds.
#14
Posted 23 June 2013 - 11:51 PM
MI_Sidd,
I think the case described by Mark-TR included two PSVs with the same set pressure while you are describing the case with staggered set pressures...
Indeed, as he mentioned both valves will be opened if fire scenario occurs...
However, in staggered case you described it is obvious that the second valve opens when the vessel pressure will reach to 105% of the set pressure...
If the point is still not clarified for you let's know to present additional explanations...
Edited by fallah, 23 June 2013 - 11:55 PM.
#15
Posted 24 June 2013 - 12:55 AM
Nasser,
Thanks for your quick response
My query is for staggered case, if the second staggered valve set @ 105% is going to open in any case, due to accumulation of the safety valve set @ 100%.
what is the point of providing staggering?
Regards.
Siddiqui
Edited by MI_Sidd, 24 June 2013 - 01:08 AM.
#16
Posted 24 June 2013 - 01:32 AM
MI_Sidd,
The point is to make stepwise opening or closing the two (or more) PSVs in relieving scenario to prevent probable chattering...
Similar Topics
Steam Pressure In Heat ExchangerStarted by Guest_mvanrijnbach_* , 15 Apr 2025 |
|
![]() |
||
![]() Valve Cavity - Pressure Relief ValveStarted by Guest_CS10_* , 20 Feb 2025 |
|
![]() |
||
![]() Psvs Relieving To Closed Drain SystemStarted by Guest__1angelia23_* , 12 Jan 2025 |
|
![]() |
||
Pressure Of An Isolated Flow In PipeStarted by Guest_phoroogh_* , 30 Jan 2025 |
|
![]() |
||
![]() Maximum Allowable Accumulated PressureStarted by Guest_mahmooddalvi09_* , 30 Jan 2025 |
|
![]() |