Dear sir,
I'm trying to calculate the vent and breather valve sizes for a double wall refrigerated storage tank of capacity 50,000 m3 at a presure of atm+, full of liquid and a temp of -32 oC. Plz guide me if there is standard for the double wall refrigerated storage tank with 50,000 m3. i.e, fluid is LPG. As there is no standard, is there something in API 2000 for this case.
|
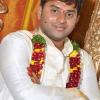
Venting Calculation For A Double Wall Refrigerated Storage Tank
Started by raviteja goriparthi, Aug 16 2012 12:51 AM
5 replies to this topic
Share this topic:
#1
Posted 16 August 2012 - 12:51 AM
#2
Posted 22 August 2012 - 10:01 AM
Raviteja;
First, I believe you made another posting of this same topic in another Forum. Please do not do this anymore. I deleted the other post; it is very confusing for our members who try to help by responding to your multiple requests in different Forums.
This application of normal relief for low pressure, refrigerated LPG storage tanks is one I am familiar with. What you (and the Forum) require is a complete description of your Scope of Work and a full, technical description of your tank system – including a P&ID.
This is NOT a normal, atmospheric tank venting and breathing operation. You are not allowed to “breathe” LPG into the atmosphere and much less breathe in atmospheric air into the LPG tank. Simply stop for a moment and focus on your scope of work: do you seriously believe that your tank will be allowed to breathe in atmospheric air? Do you think that you will be allowed to break a potential vacuum by allowing atmospheric air into the LPG tank? Handling saturated LPG at sub-zero temperatures is a very special situation and one that is full of potential hazardous scenarios.
You must sit down, detail out your basic data and carefully think of all the required scope of work operation that you must design around and comply with. This is a simple, basic task that must be done in DETAIL and scrutinized very carefully to ensure that all safety precautions and steps are incorporated in designing a pressure and vacuum relief system for this type of application.
First, I believe you made another posting of this same topic in another Forum. Please do not do this anymore. I deleted the other post; it is very confusing for our members who try to help by responding to your multiple requests in different Forums.
This application of normal relief for low pressure, refrigerated LPG storage tanks is one I am familiar with. What you (and the Forum) require is a complete description of your Scope of Work and a full, technical description of your tank system – including a P&ID.
This is NOT a normal, atmospheric tank venting and breathing operation. You are not allowed to “breathe” LPG into the atmosphere and much less breathe in atmospheric air into the LPG tank. Simply stop for a moment and focus on your scope of work: do you seriously believe that your tank will be allowed to breathe in atmospheric air? Do you think that you will be allowed to break a potential vacuum by allowing atmospheric air into the LPG tank? Handling saturated LPG at sub-zero temperatures is a very special situation and one that is full of potential hazardous scenarios.
You must sit down, detail out your basic data and carefully think of all the required scope of work operation that you must design around and comply with. This is a simple, basic task that must be done in DETAIL and scrutinized very carefully to ensure that all safety precautions and steps are incorporated in designing a pressure and vacuum relief system for this type of application.
#3
Posted 22 August 2012 - 12:32 PM
Raviteja; for refrigerated tanks regardless if is simple wall or double tanks the normal ventaing shall be calculated for the following scenarios according to EN1473:
- heat input: due to heat input in normal operation is to be determined by
assuming ambient air at the maximum temperature observed in the course of a hot summer day.
- fluid input: Filling of the tank generate a piston effect. The maximum volume flow rate for tank filling is to be taken for the value of VL the resulting gas volume flow rate (expressed under the actual conditions of temperature and pressure in the gaseous crown of the tank).
- flash at filling: instantaneous vaporisation occurs (called "Flash") see API 2000.
- variation in atmospheric pressur: see API 2000.
- fluid suction: Withdrawal of liquid shall be offset by a gaseous input in order to prevent negative pressure. The volume flow rate of gas is taken to be equal to the maximum volume flow rate of the suction pumps.
The causes shown above are the relief during normal venting, but I think that your design case is fire out the tank, during early stage of fire, heat gain will be utilized for expansion of vapors between the walls. It will take several hours for vaporization of liquid in these tanks.
However Ludwing chapter seven "Applied Process Design for Chemical and Petrochemical Plants" regardless the type of wall described a method to calculate the relief emergency for fire, let me attach the file for your information.
- heat input: due to heat input in normal operation is to be determined by
assuming ambient air at the maximum temperature observed in the course of a hot summer day.
- fluid input: Filling of the tank generate a piston effect. The maximum volume flow rate for tank filling is to be taken for the value of VL the resulting gas volume flow rate (expressed under the actual conditions of temperature and pressure in the gaseous crown of the tank).
- flash at filling: instantaneous vaporisation occurs (called "Flash") see API 2000.
- variation in atmospheric pressur: see API 2000.
- fluid suction: Withdrawal of liquid shall be offset by a gaseous input in order to prevent negative pressure. The volume flow rate of gas is taken to be equal to the maximum volume flow rate of the suction pumps.
The causes shown above are the relief during normal venting, but I think that your design case is fire out the tank, during early stage of fire, heat gain will be utilized for expansion of vapors between the walls. It will take several hours for vaporization of liquid in these tanks.
However Ludwing chapter seven "Applied Process Design for Chemical and Petrochemical Plants" regardless the type of wall described a method to calculate the relief emergency for fire, let me attach the file for your information.
Attached Files
#4
Posted 22 August 2012 - 02:35 PM
Robert:
I may be wrong, but I believe that the heat gain curve that is depicted in Ludwig is the same as the API 2000 curve and this relationship is strictly derived from empirical data related to standard, single-wall API atmospheric storage tanks filled with crude oil or other similar hydrocarbons.
I think the heat gain/vapor generated relationship for a double-wall tank is much more complicated than that.
Additionally, low-temperature LPG vessels normally are not allowed to breathe to the atmosphere. They are normally installed with a refrigeration capability that allows them to control the vapor pressure inside the tank. This is done either by recompression of the generated vapors or by an external refrigeration system. Therefore, the PVSVs depicted in the Ludwig information do not apply. There is no "normal" venting to the atmosphere or to flare - unless the LPG is considered so inexpensive that it is cheaper to do so. But if that were the case, then why employ an expensive double-wall storage tank?
I may be wrong, but I believe that the heat gain curve that is depicted in Ludwig is the same as the API 2000 curve and this relationship is strictly derived from empirical data related to standard, single-wall API atmospheric storage tanks filled with crude oil or other similar hydrocarbons.
I think the heat gain/vapor generated relationship for a double-wall tank is much more complicated than that.
Additionally, low-temperature LPG vessels normally are not allowed to breathe to the atmosphere. They are normally installed with a refrigeration capability that allows them to control the vapor pressure inside the tank. This is done either by recompression of the generated vapors or by an external refrigeration system. Therefore, the PVSVs depicted in the Ludwig information do not apply. There is no "normal" venting to the atmosphere or to flare - unless the LPG is considered so inexpensive that it is cheaper to do so. But if that were the case, then why employ an expensive double-wall storage tank?
#5
Posted 22 August 2012 - 03:07 PM
Dear Art very good, you are right, the list above is the typical list of overpressure in any refrigerated tank include normal and emergency venting, for the first case is normal include a boil-off compressor in order to recovery the vapors generated during each case, in the second case is emergency fire case this relief could be go to atmosphere or to flare depending of the dispersion study and the local regulations.
Now regarding the fire case of tank with double wall, is different the behavior to simple wall, now is something is right the more conservative case is assume that the wall is simple for calculate the load relief for fire case. but there is a factor very important the initial cost because for double wall is higher than simple wall this is because a tank with double wall keeps the temperature allows to keep the temperature for a longer time in the tank that a single-walled tank, in fact are used when the liquid temperature is quite low for example liquid nitrogen and the external temperature is considerable high. I read the standard EN1473 here is described the types of tank and not discriminate between two or one wall.
Please iif you have any suggestions please let me know
thank you!
Now regarding the fire case of tank with double wall, is different the behavior to simple wall, now is something is right the more conservative case is assume that the wall is simple for calculate the load relief for fire case. but there is a factor very important the initial cost because for double wall is higher than simple wall this is because a tank with double wall keeps the temperature allows to keep the temperature for a longer time in the tank that a single-walled tank, in fact are used when the liquid temperature is quite low for example liquid nitrogen and the external temperature is considerable high. I read the standard EN1473 here is described the types of tank and not discriminate between two or one wall.
Please iif you have any suggestions please let me know
thank you!
Edited by Robert Montoya, 23 August 2012 - 07:01 AM.
#6
Posted 23 August 2012 - 12:34 AM
Dear All,
In LPG storage tanks the pressure/vacuum are normally controlled by two different pressure control valves. Pressure regulator for overpressure control connects to flare network and vacuum control is to be performed by introducing fuel gas via another pressure regulator from the fuel gas network. Out of normal operating pressure range, overpressure and vacuum conditions due to both thermal breathing and fire case are prevented by a proper sized vent system based on API/2000, API 521, API 521.
A set of PSV's would act as pressure relief devices in the case of overpressure whose tail pipes will be provided with dry powder connections for snuffing. A PSE element (normally a rupture disk) with higher set pressure is usually provided as a reserve capacity of the mentioned PSV's.
A set of vacuum breakers will protect the tank from high vacuum conditions.
Fallah
In LPG storage tanks the pressure/vacuum are normally controlled by two different pressure control valves. Pressure regulator for overpressure control connects to flare network and vacuum control is to be performed by introducing fuel gas via another pressure regulator from the fuel gas network. Out of normal operating pressure range, overpressure and vacuum conditions due to both thermal breathing and fire case are prevented by a proper sized vent system based on API/2000, API 521, API 521.
A set of PSV's would act as pressure relief devices in the case of overpressure whose tail pipes will be provided with dry powder connections for snuffing. A PSE element (normally a rupture disk) with higher set pressure is usually provided as a reserve capacity of the mentioned PSV's.
A set of vacuum breakers will protect the tank from high vacuum conditions.
Fallah
Similar Topics
![]() Phosphoric Acid 56% Tank LiningStarted by Guest_Phosphoric123_* , 20 Apr 2025 |
|
![]() |
||
![]() Tank Inlet Diffuser LengthStarted by Guest_RAFAELDAVE_0752_* , 08 Apr 2025 |
|
![]() |
||
Discussion - Predict Storage Tank Heat Transfer Precisely By Jimmy D KStarted by Guest_raj shekhar_* , 25 Mar 2025 |
|
![]() |
||
Tank Filing TimeStarted by Guest_not_mikhail_* , 17 Mar 2025 |
|
![]() |
||
![]() Api Calculation In HysysStarted by Guest_phoroogh_* , 22 Feb 2025 |
|
![]() |