|
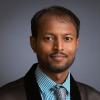
Reducing Batch Reactor Cycle Time
Started by Vivek Siddhaganesh, Nov 22 2012 06:23 AM
7 replies to this topic
Share this topic:
#1
Posted 22 November 2012 - 06:23 AM
Dear All,
This is my first post on the Cheresources please Kindly ignore if I made any mistake in asking Questions.
Currently I am working as trainee Engineer. As this is my first job it is going difficult to co-relate the theoratical knowledge with practical way.
Now my question is that,
I have Given one task to reduce the batch cycle time for one process. As an engineering point of view I have done the mass and heat balance for the process.
But I think I have to focus on Aagitation and Proper heat transfer problems.
Can I am going on the right track or any suggestions to focus on other parameters ?
Please reply...
Thanks and Regards
Vivek.
This is my first post on the Cheresources please Kindly ignore if I made any mistake in asking Questions.
Currently I am working as trainee Engineer. As this is my first job it is going difficult to co-relate the theoratical knowledge with practical way.
Now my question is that,
I have Given one task to reduce the batch cycle time for one process. As an engineering point of view I have done the mass and heat balance for the process.
But I think I have to focus on Aagitation and Proper heat transfer problems.
Can I am going on the right track or any suggestions to focus on other parameters ?
Please reply...
Thanks and Regards
Vivek.
#2
Posted 22 November 2012 - 07:37 AM
Some of my suggestions would be:
The first thing you have to check the reaction and what order it is.
Secondly check whether the reaction is exothermic or endothermic. whether providing any external heat can help increase the rate.
Type of catalyst used and whether increasing the quantity of catalyst can increase the speed of reaction.
Pressure at which the reaction is taking place. whether any increase in pressure is possible
The first thing you have to check the reaction and what order it is.
Secondly check whether the reaction is exothermic or endothermic. whether providing any external heat can help increase the rate.
Type of catalyst used and whether increasing the quantity of catalyst can increase the speed of reaction.
Pressure at which the reaction is taking place. whether any increase in pressure is possible
#3
Posted 22 November 2012 - 07:52 AM
Welcome, Vivek. I believe you have begun well with material and energy balances. You get familiar with the plant and its (flow / PID) diagrams. "Pushing" (increasing capacity of) heat transfer equipment seems more time consuming, so deal with it only if you have to, or if some exchanger problem is quite apparent. Same (with more emphasis) about agitation.
Probably now you have to investigate time intervals of the steps in batch cycle and how to shorten its total time by potentially shortening the time of critical steps to the extent possible. First quite practically, even not using Chemical Engineering knowledge (this can be used later, if needed). Is the production blocked by some capacity to be increased? Can we reduce dead times more? If two reagents are produced and directly used for a product, is their production time (almost) same? Is storage capacity enough for raw materials / products, or production is delayed due to small capacities? Clear thinking and observation is needed for this task, as well as guidance from someone knowing the plant well. I do not think there is a better way to know the plant in detail.
I have not worked in batch but in continuous processes, where "debottlenecking" was supposed to be simpler. Maintenance played an important role, too. Overhaul time for whole plant should be minimized. So overhaul time for each individual piece of equipment has to be short enough (we registered it) by either in plant spare, or effective maintenance service. Extent of preventive maintenance is an important issue, but probably not a present task for you.
Transport, storage, handling issues are often apt to more direct improvements, as I have heard; but this also depends on the plant. It would be useful to describe plant activities (now or next time) in order to get more specific info for those having relevant experience.
Then you can deal with improvements in heat transfer / agitation, if you have evidence that the relevant equipment block the production chain.
If you like it, it is an exciting job resulting in valuable experience. I assume you are in the plant (Operations), not in white collar offices.
Probably now you have to investigate time intervals of the steps in batch cycle and how to shorten its total time by potentially shortening the time of critical steps to the extent possible. First quite practically, even not using Chemical Engineering knowledge (this can be used later, if needed). Is the production blocked by some capacity to be increased? Can we reduce dead times more? If two reagents are produced and directly used for a product, is their production time (almost) same? Is storage capacity enough for raw materials / products, or production is delayed due to small capacities? Clear thinking and observation is needed for this task, as well as guidance from someone knowing the plant well. I do not think there is a better way to know the plant in detail.
I have not worked in batch but in continuous processes, where "debottlenecking" was supposed to be simpler. Maintenance played an important role, too. Overhaul time for whole plant should be minimized. So overhaul time for each individual piece of equipment has to be short enough (we registered it) by either in plant spare, or effective maintenance service. Extent of preventive maintenance is an important issue, but probably not a present task for you.
Transport, storage, handling issues are often apt to more direct improvements, as I have heard; but this also depends on the plant. It would be useful to describe plant activities (now or next time) in order to get more specific info for those having relevant experience.
Then you can deal with improvements in heat transfer / agitation, if you have evidence that the relevant equipment block the production chain.
If you like it, it is an exciting job resulting in valuable experience. I assume you are in the plant (Operations), not in white collar offices.
#4
Posted 22 November 2012 - 09:45 AM
My advice is - do not start looking at specifics until a detailed cycle time analysis of the entire batch process is complete. Account for every minute of time with a reason, such as pumping raw material A, heating to reaction temperature, reacting according to batch instructions, extra reaction time to obtain quality, waiting on laboratory results, no activity (operator at lunch), pumping out product, rinsing reactor, etc., etc., etc.
Then, decide what can be changed to shorten the cycle time without affecting product quality. Can two seperate items be done at the same time? This sometimes gives good cycle time reductions at no cost! Can transfer rates of the most time consuming steps be reduced with a bigger pump/piping? Will more heat transfer area speed up some steps? Will more "delta T" speed up some heat transfer steps? Will process automation eliminate periods of no activity controlled by operators? Is "turnaround time" (the time from the end of batch #1 to the beginning of batch n# 2) excessive? There should be a zero standard for "turnaround time".
I've been in batch processes for 33 years. The detailed analysis mentioned above is the starting point that drives all downstream investigations, so it must be done and documentation must be painstakingly thorough! Or, you will get lost somewhere along the way. Focus on those items that give the biggest bang (largest cycle time reduction) for the buck (lowest cost).
Then, decide what can be changed to shorten the cycle time without affecting product quality. Can two seperate items be done at the same time? This sometimes gives good cycle time reductions at no cost! Can transfer rates of the most time consuming steps be reduced with a bigger pump/piping? Will more heat transfer area speed up some steps? Will more "delta T" speed up some heat transfer steps? Will process automation eliminate periods of no activity controlled by operators? Is "turnaround time" (the time from the end of batch #1 to the beginning of batch n# 2) excessive? There should be a zero standard for "turnaround time".
I've been in batch processes for 33 years. The detailed analysis mentioned above is the starting point that drives all downstream investigations, so it must be done and documentation must be painstakingly thorough! Or, you will get lost somewhere along the way. Focus on those items that give the biggest bang (largest cycle time reduction) for the buck (lowest cost).
#5
Posted 22 November 2012 - 07:25 PM
A few examples to support the excellent explanation given by latexman.
Now you should be ready for the hard work!
Hope this helps
Breizh
Now you should be ready for the hard work!

Hope this helps
Breizh
#6
Posted 23 November 2012 - 08:15 AM
It might be also useful to follow a brief seminar on time scheduling (PERT etc), to get accustomed with the idea of critical path and float. Of course in case you are not accustomed with them.
These concepts and diagrams are used here for big projects or construction works; yet one can get the feeling how to systematize time; even by activities different to these met in chemical batch processes.
These concepts and diagrams are used here for big projects or construction works; yet one can get the feeling how to systematize time; even by activities different to these met in chemical batch processes.
Edited by kkala, 23 November 2012 - 08:15 AM.
#7
Posted 04 December 2012 - 11:14 AM
Vivek;
Welcome to Forum.
After detailed cycle analysis ,one has to check with Material and energy balance.
Limiting equipment capacity which decides overall capacity of reaction steps.For example reactor volume or centrifuge capacity
By increasing limiting equipment capacity ,One can increase Production in Batch process.
I hope this shall help.
SRShah
Welcome to Forum.
After detailed cycle analysis ,one has to check with Material and energy balance.
Limiting equipment capacity which decides overall capacity of reaction steps.For example reactor volume or centrifuge capacity
By increasing limiting equipment capacity ,One can increase Production in Batch process.
I hope this shall help.
SRShah
#8
Posted 05 December 2012 - 09:12 AM
Hello Vivek
To reduce the batch cycle time, first of all we need to go through the each steps of process and check the time consumption in individual steps. This would lead us to focus on particular step where time consumption is high.
It also happens that undersized equipment consume more time (e.g. filtration area of sparkler filter).
Wrong selection of equipment also increases the batch cycle time as it increases the time of operation.
Definitely increasing the limiting equipment capacity increases the batch size.
With Regards
Chirag Ukani
To reduce the batch cycle time, first of all we need to go through the each steps of process and check the time consumption in individual steps. This would lead us to focus on particular step where time consumption is high.
It also happens that undersized equipment consume more time (e.g. filtration area of sparkler filter).
Wrong selection of equipment also increases the batch cycle time as it increases the time of operation.
Definitely increasing the limiting equipment capacity increases the batch size.
With Regards
Chirag Ukani
Similar Topics
Tank Filing TimeStarted by Guest_not_mikhail_* , 17 Mar 2025 |
|
![]() |
||
Batch Adsorption: H/d Ratio For Vessel SizingStarted by Guest_Victor_process_Engineer_* , 28 Feb 2025 |
|
![]() |
||
![]() Multi-Tubular Packed Bed ReactorStarted by Guest_shambola_* , 12 Feb 2025 |
|
![]() |
||
![]() Help On Simulation Of Reactor In Aspen PlusStarted by Guest_m.ghaziasgar_* , 06 Jan 2025 |
|
![]() |
||
Psv Release Rate Vs TimeStarted by Guest_stu_* , 30 Nov 2024 |
|
![]() |