|
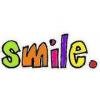
B31.3 Help - Calculating Pipe Diameters
#1
Posted 13 February 2013 - 12:10 PM
#2
Posted 13 February 2013 - 02:24 PM
Dayo:
There is confusion in your topic.
When “designing” a piping application, the first thing that is done is a process design. This specifies the pipe nominal size required for the given process flow. A process engineer does this determination when dealing with an engineering contractor.
Next, what happens is that the application is turned over to a mechanical engineer who uses a code – such as ASME B31.3 – and calculates or selects the pipe specification that fits the application.
What you are trying to do is combine both calculations into one. That is not logical. First you must determine the correct pipe size in accordance with the process pressure drop and fluid velocity constraints that are in your application. Once you do that, you use the required pipe size to apply the hoop stress formula in ASME and find the wall thickness / schedule number that is needed to identify the pipe physical characteristics.
#3
Posted 13 February 2013 - 02:38 PM
Dear,
As Junior engineer I learned that the simplest concept can help in cases such as yours. There are design criteria such as velocity and pressure drop that should guide your decision making regarding a pipe's size. I have seen two seniors coming up with 2 different pipe's size for the same system but both were right given the reasoning hehind the result. I have develope an excel spreadsheet I usually use the velocity criteria of 6-10 ft/sec for liquid/slurries and 50-110 ft/sec for gases. rough draft of your system can help or give us at least the flow, viscosity and S.G.
Volume flow=Area*Velocity=pi*D*velocity/4. This equation should get you going.
Thank you,
Alan
#4
Posted 14 February 2013 - 02:26 AM
Dayo,
If you did refer to scope of ASME B31.3 you had found that pipe sizing is out of scope of this code. In fact this code would be applied for mechanical integrity and design of a process piping system already sized based on meeting relevant process requirement/limitations.
#5
Posted 14 February 2013 - 03:10 AM
Dayo,
See attached copy.
http://www.keydesign...ingB3132008.pdf
http://www.pipingsol...s/Chapter 8.pdf
Regards
Shivshankar
Attached Files
Edited by Shivshankar, 14 February 2013 - 07:47 AM.
#6
Posted 14 February 2013 - 03:24 AM
Dayo,
Just add valuable comments from other members,
as far as i know, B31.3 didn't give any size data of pipe. You are definitely correct when related B31.3 with pipe wall thickness and as chemical engineer its "sometimes around our scope". The only link missed up is you also need B36.10 when you need to determine the NPS with correct schedule. But you must do line sizing first where its usually based on two main criteria (flowing fluid velocity and pressure drop) as Mr. Art mentioned above. For sizing line, you should look GPSA section 17 or API 14 E for both formula (equation) and criteria.
Hopefully this help.
#7
Posted 14 February 2013 - 09:23 AM
Thank you all very much. It all adds up! We all know how "senior" engineers can be...they tell you to "calculate pipe sizes using B31.3". I already did the sizing using promax, but just wanted to confirm it with hand calculations. This forum has enlightened me.
#8
Posted 14 February 2013 - 11:15 AM
Shivshankar's links give information on the activities supported by ASME B31.3 (piping design), which are normally responsibility of piping / mechanical engineer. Chemical engineers usually estimate wall thickness preliminarily (e.g. for cost estimate); Perry's subsection of "Process-Plant Piping" , in the "Transport and Storage of Fluids" (Section 10 in the 7th edition of Perry), provides guidance and data for estimate of wall thickness based on design pressure and temperature only. I think it is not bad as an introductory test to the subject.
Line sizing criteria (i.e. proper line diameter) and pressure drop formulas can be found in <http://www.cheresour...rent-standards/> and <http://www.cheresour...-for-pipelines/>.
It seems that pipe / thickness standardization per ASME B36.10 (e.g. table 10-18 of Perry 7th ed - properties of steel pipe) is valid for pipes or tubes in North America made of steel, (wrought) iron, stainless steel, <http://en.wikipedia....minal_Pipe_Size>; and that e.g.10" Sch40 means 10" nominal diameter and 0.365" wall thickness, independently of the material. Advice would be welcomed. Confusion on wall thickness - SchNo for different materials probably existed in the past (design press = SchNo× allowable material stress /1000).
Edited by kkala, 14 February 2013 - 11:20 AM.
Similar Topics
Pressure Of An Isolated Flow In PipeStarted by Guest_phoroogh_* , 30 Jan 2025 |
|
![]() |
||
Software For Calculating Flow Through A PipeStarted by Guest_Deep24_* , 07 May 2018 |
|
![]() |
||
![]() Pipe Entrance And Exit LossesStarted by Guest_katmar_* , 13 Nov 2024 |
|
![]() |
||
![]() Nitrogen Leak Test On PipeStarted by Guest_mesbah_* , 24 Oct 2024 |
|
![]() |
||
![]() ![]() Reciprocating Pump Acceleration Head With Vertical Pipe LineStarted by Guest_Sansan_* , 18 Oct 2024 |
|
![]() |