I want to know the where we can use air fail to open and air fail to close control valves and also the basic determining factor or parameter which decides usage of either of valves..!
|
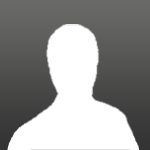
Control Valves
#1
Posted 21 November 2013 - 11:47 AM
#2
Posted 21 November 2013 - 01:50 PM
Hi,
The main purpose is reaching to a safe position in an air failure case. It will dicatate usage of either valve...For example a minimum flow control valve is certainly a FO valve because if it was a FC valve and air already failed, during a discharge blocked outlet might conduct the relevant pump to shut off condition...
Edited by fallah, 21 November 2013 - 01:53 PM.
#3
Posted 21 November 2013 - 02:28 PM
A relared question:
How common is it to spec. "Fail Indeterminate" on P&ID's. Is there a cost incentive to specify Fail Indeterminate for non critical duties? Or is Fail Indeterminate rarely used.
#4
Posted 21 November 2013 - 07:37 PM
Typically valves such as heating valves on a reactor, are fail closed/air to open, to avoid an overtemperature scenario. Valves that feed natural gas to a boiler would also be typically fail closed/air to open. Valves that control coolant flow to a condenser or reactor jacket to control an exotherm might be fail open. Valves should be specified to fail to the SAFE state. Meaning of safe, may vary, but I'd specify chemical addition valves typically as fail closed, so as not to, say, overfill a reactor by gravity feeding through a pump -- even if that meant pump might deadhead -- but each must be assessed on a case-by-case basis. Often limit switches are incorporated on critical block (on/off) valves. For control valves (throttling valves), position feedback is frequently called for so that control system knows actual field position of valve. Modern valve positioners can send position back over HART. I often program control valves to sound an alarm if a control valve fails to go to +-5% of commanded position and stays at that deviation for > 30 seconds. Typically valves are fail open, fail closed, or fail last. e.g. if I have a double-acting cylinder, and are is lost, it fails last. Though even that can be configured with an air reservoir with check valve at reservoir inlet, so that the solenoid, when de-energized, always has air to move piston back to closed even if main instrument air supply is severed. Double-acting cylinders are the less expensive actuator for larger sized valves but the spring return actuators are not terribly expensive. Typically P&ID indicates FC or FO above valve tag, e.g. XV-101 with FC above it.
#5
Posted 22 November 2013 - 07:18 AM
thanks fallah
could you please elaborate by giving more examples..?
#6
Posted 22 November 2013 - 07:23 AM
thanks fseipel
if I want to control fuel gas flowrate in furnance..which type of valve I would use?
#7
Posted 22 November 2013 - 07:36 AM
could you please elaborate by giving more examples..?
Hi,
Among on-off valves:
BDVs (Blowdown Valves): FO
SDVs (Shutdown Valves): FC
#8
Posted 22 November 2013 - 08:01 AM
could you please elaborate by giving more examples..?
Hi,
Among on-off valves:
BDVs (Blowdown Valves): FO
SDVs (Shutdown Valves): FC
thanks
which type of valves used for fuel gas flowrate control in direct fired heaters? both for natural n forced draught?
#9
Posted 22 November 2013 - 09:12 AM
thanks fseipel
if I want to control fuel gas flowrate in furnance..which type of valve I would use?
What would happen if the valve is Failed open? If you can explain what happen then you know the answer...
#10
Posted 22 November 2013 - 12:37 PM
More interesting scenarios: A valve in the reflux return line to a distillation column? I'd say FO but not sure.
How about a vacuum column with an ejector air bleed valve controlling the vacuum level. FC?
Feed line valve to a distillation column. FC? What if feed is being preheated by heat transfer with hot bottoms. Still FC?
#11
Posted 22 November 2013 - 06:44 PM
I always specify reflux valves to fail back to column/fail return as you suggest -- however it should be 'safe' whether they fail to cut tank(take off) or still pot(return). However if it fails to take-off position, that may mean you take over lights and have to redistill you receiver contents, whereas, if it fails in the return (reflux) position, it only wastes time (no take-off), and you can resume distillation upon repair without redistilling cut tank contents. So to me that's more a quality/efficiency issue than a safety one. Incidentally, perhaps this belongs in a different thread, but what is your preferred splitter valve on small pilot scale (3"-6") columns? I've used 3-way quarter turn plug and ball valves, 2-way valves on one leg only, dual 2-way valves, solenoid valves, buckets, etc. I think the magnetically coupled designs are nice but some are problematic to repair -- e.g. Distillation Engineers when the hinge breaks. Having the splitter external so it can be serviced without head removal is a huge advantage. Due to frequent cycling, when using a plug or ball valve, even with high cycle packing, maintenance is frequent. Buckets are great but expensive. Flappers aren't bad either. For vacuum I'd say it depends if product is air-reactive and/or whether low vacuum may cause vapor to blow by the condenser. I think feed should always be fail closed to avoid flooding a column liquid full and overflowing out vent or to vacuum pump. If preheating may want feed valve before preheater BUT need to be careful if it closes since then all feed in exchanger may vaporize potentially leaving foulant.
#12
Posted 22 November 2013 - 11:28 PM
Thanks @fspeipel!
To answer your question: I don't have that much of pilot plant distillation experience but I've always preffered valves on both legs for the splitter and very often simple plug / ball valves if reflux was set manually and an automatic flapper for the more instrumented columns.
A +1 for the external splitter comment.
I think I agree with all your FC / FO assessments.
#13
Posted 23 November 2013 - 02:43 AM
More interesting scenarios: A valve in the reflux return line to a distillation column? I'd say FO but not sure.
Hi,
Control valve in reflux return line;
If would be FO, in the case of air failure major consequences would be as follows:
- Temperature profile in distillation column will drop. This may also lead to flooding of top trays. Potential off spec product from distillation column.
- Level in column bottom may build up due to more liquid flow to bottom till reboiler compensates.
- Potential decrease in reflux drum level as an immediate consequence.
If would be FC, in the case of air failure major consequences would be as follows:
- Build up of level in reflux drum leading to overfilling. Overhead condenser can flood leading to loss of condenser duty. Overpressurization of distillation column and reflux drum might happen.
- Loss of reflux to distillation column leading to high temperature in column followed by overpressurization.
To decide the valve to be FO or FC you should evaluate the available safeguards against each consequence, but at a glance appears the consequences of FC condition are more severe than FO one. In real world also the control valves in reflux return lines are mostly specified as FO...
Above explanations being submitted as an example to show the way to decide about the position of a control valve in air failure...
#14
Posted 23 November 2013 - 08:40 AM
thanks fseipel
if I want to control fuel gas flowrate in furnance..which type of valve I would use?
What would happen if the valve is Failed open? If you can explain what happen then you know the answer...
It should be fail closed..because during shutdown if instrument air fails and if it is fail open, valve will be 100% open and all of the fuel gas would enter the furnace..but we want opposite of that..therefore we will use fail closed..!! is it right sir?
#15
Posted 24 November 2013 - 08:26 AM
Columns reflux or feed line control valves can be failed open to drain back the liquid to the vessel in case of any plant trip. Designing of control valve FO/FC to provide safe plant trip and depressurization conditions during total instrument air pressure failure rather than looking into individual control valve failure during normal running. It differs plant to plant depends on HAZOP study. Our plant equipped with two feed control valve to column in which one is equipped with FC another one FO. Hence most of time process upset can be compromised to maintain plant safety.
Edited by Babu Prasad, 24 November 2013 - 08:31 AM.
#16
Posted 24 November 2013 - 08:31 AM
Our plant equipped with two feed control valve to column in which one is equipped with FC another one FO.
What's the rationale there? Are they in parallel? If the outage is long enough the FO valve can still flood the column, right?
Or are you talking about two different columns? I am confused.
Edited by curious_cat, 24 November 2013 - 08:32 AM.
#17
Posted 24 November 2013 - 08:56 AM
Our plant equipped with two feed control valve to column in which one is equipped with FC another one FO.
What's the rationale there? Are they in parallel? If the outage is long enough the FO valve can still flood the column, right?
Or are you talking about two different columns? I am confused.
It is same column but two different feed trays, one feed control valve with FC goes as top feed and another feed control valve with FO goes thro exchanger to middle of column. if any one fails & flow can be controlled with other valve until affected valve isolated during normal run.
#18
Posted 12 June 2014 - 09:46 AM
when will we use FC valve in column reflux line..
Similar Topics
![]() Breather Valves - Liquid Movement In Breathing ScenarioStarted by Guest_panoska_* , 14 Dec 2024 |
|
![]() |
||
Surge Analysis-Control LogicsStarted by Guest_stu_* , 30 Dec 2024 |
|
![]() |
||
![]() Pump Dischrge Control Valve SizingStarted by Guest_Lyne_* , 04 Jun 2024 |
|
![]() |
||
![]() ![]() Ahu Chilled Water Hot Water Control And FunctioningStarted by Guest_RAMSAI_* , 23 Sep 2024 |
|
![]() |
||
![]() Isolation Requirement For Bypass Valves/ Movs.Started by Guest_shantanu.ghag_* , 15 Sep 2024 |
|
![]() |