|
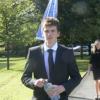
Cochwillan Hydropower Siphon Questions
#1
Posted 09 March 2016 - 04:07 AM
#2
Posted 09 March 2016 - 05:11 AM
A few questions before we get down to details. Your spreadsheet gives the required flow as 1.62 m3/s but you have calculated the flow as 11.0 m3/s. Does your pipe really need to be so oversized? How is the flow rate controlled?
The spreadsheet (J16 - J18) shows the elevation change between the inlet and outlet to be -7.92 m, but the drawings give it as -4.03 m. Which is correct?
The submergence of the inlet looks very small to me. Have you checked for vortexing? You do not want to draw air into a siphon. I would be uncomfortable with a siphon designed to run with the pipe half full of air.
#3
Posted 09 March 2016 - 06:06 AM
Steffan ,
Harvey is a master in fluid dynamic . Please answer his questions .
Breizh
Edited by breizh, 09 March 2016 - 06:12 AM.
#4
Posted 09 March 2016 - 06:31 AM
The design flow rate of the turbine is 1.62m3/s so that is the desired flow to go down the pipes to generate 90kW. The pipes were sized initially to keep the velocity below 1m/s. There is a sluice gate an the intake to control the flow rate. Yes I've noticed what I've done by calculating the 11m3/s on the spreadsheet, that considers the velocity over the full elevation change which is why it's so high but as I said, the design flow rate is 1.62m3/s which occurs around 30% of the year for the river (Q30 flow).
The elevations on the spreadsheet between the inlet and the outlet water level is -7.92m. I'm not sure where you've seen on the drawings that the elevation change is -4.03m but the value on the spreadsheet are correct. The intake water level is at 19.162, the water level above the outfall channel floor is 11.240 (calculated based on the channel width and considering the water level in the river at the design rated flow).
Yes, based on Gordon J.L vortices at intakes theorem with 1.5m pipes, design flow rate of 1.62m3/s (v = 0.9167m/s) the minimum submergence to prevent air entrainment is 610mm. The bellmouth entrance to the pipeline is therefore located 610mm below the minimum water level.
#5
Posted 09 March 2016 - 11:00 AM
Thanks for the quick answers. The 4.03 m elevation change I calculated was a mistake, but I would question using the full differential that you have taken. I have not used this type of turbine myself so I have assumed that the head available is only from the surface of the supply to the centreline of the turbine inlet. This would be 5.84 m, which is still much more than you need to get the 1.62 m3/s that you require so it is probably not an issue.
What is the reason for wanting the velocity below 1 m/s? The document referenced by breizh recommends a minimum velocity of 2.6 m/s for a siphon diameter of 1200 mm. Your Froude number of 0.239 means that any air that enters the pipe will be trapped. A rule of thumb is that the Froude number should be kept below 0.3 in a line that should be self venting. In your case self venting is exactly what you do not want - you want the air to be removed. A Froude number greater than 0.5, and ideally more than 0.7, would be the target.
It is good that you have addressed the question of required submergence, but the greater submergences recommended in breizh's reference would make me feel more comfortable.
A pipe diameter of 900 mm would give you a velocity of 2.5 m/s and a Froude number of 0.84 - and a much cheaper installation. Any air that enters a pipe of this size will be rapidly flushed out. But this also raises the question of whether entrained air is any problem for the turbine. As I said, I do not know these turbines and don't know whether air would be a problem. If air is a problem I would definitely go for a larger safety factor on the submergence.
#6
Posted 09 March 2016 - 11:09 PM
Hi ,
Just a comment , how do you intend to prime the line ?
Breizh
Edited by breizh, 10 March 2016 - 01:51 AM.
#7
Posted 10 March 2016 - 05:58 AM
Hi both,
With the Crossflow turbine, the head available is from the intake water level to the outfall water level due to the draft tube beneath the turbine. You can see the layout on the turbine house layout I've attached where the draft tube end is submerged. For you information, the draft tube is a conduit which connects the turbine runner exit to the outfall, where water is discharged at atmospheric pressure. The purpose of it is to reduce the velocity of the discharged water to minimise the loss of energy at the outlet. If the velocity is higher, the kinetic energy would be higher meaning the losses would be more. In other words we use a draft tube to have more net available head across the turbine to produce more power.
Just to correct my previous answer and clarify - the sluice gate will be used to shut off the water supply to the intake area, but the flow rate will be controlled by the inlet guide vanes on the turbine.
The reason for wanting to keep the velocity below 1m/s is to keep the losses down in the pipeline to maximise the head available. The total head loss as a percentage of gross head is 5.44% for a 1.5m pipe. If we used a 900mm pipe as you mentioned the total head loss as a percentage of gross head would be 21.24% which would be too much of a head loss and compromise the economic feasibility of the scheme because it would significantly affect the energy capture.
We can use a vacuum pump if necessary to remove the air prior to starting the siphon, though it would be nice to avoid this is possible. With the current arrangement, it sounds like it would be needed. If we used a vacuum pump to remove air from the highpoint on the pipe at turbine start up, and assuming no air would be able to enter the siphon through the intake assuming the submergence was satisfactory with a safety factor, what are the implications of having a Froude number of 0.239 (1.5m pipe) in this case? I understand that any air that would enter the system wouldn't get flushed out with this Froude number but if it was primed at start up, would this be ok?
Looking at the spreadsheet I put together for these calculations, the allowable suction head on the siphon Hs is higher than the Heffs value considering the upstream head losses which satisfies the siphon design given in the reference. Regarding the allowable downstream head on the siphon HT, this is lower than the HeffT value considering the downstream head losses along the 1.5m pipe. I don't understand fully what can I conclude from this?
Regarding the air entrainment causing a problem for the turbine, I believe it's fine at start up but not desirable for prolonged periods but I'm not entirely sure so I'll answer that in another response once I've clarified with my colleague later on today.
Thank you,
Steffan
#8
Posted 10 March 2016 - 07:55 AM
I couldn't find a head vs flow chart for the Ossberger, but a theoretical calculation shows that you will need 7 or 8 m head at the turbine inlet, so I understand that you are basically compelled to use the large diameter pipe. The bit above the water level is not very high, so the pressure won't be much below atmospheric and it should be easy to prevent air leaking into the pipe through flanges and fittings
So your only real concern is air being entrained into the inlet, and you have addressed this problem by designing for a safe submergence. You will probably need a vacuum pump for start-up so if air does turn out to be a problem you may have to run the vacuum pump manually now and then, or connect it to a pressure switch at the turbine inlet so that it can run automatically when needed. The pipe is such a large diameter that if the air ingress is small you may find you need to run the vacuum pump only every few weeks, if at all.
I also do not understand the significance of the Heff values and I don't have time to work through that reference in detail now.
#9
Posted 10 March 2016 - 10:22 AM
Thanks Katmar.
Yes that's right, with an overall efficiency (turbine 82%, gearbox 98% and generator 95%) of 76.3%, the net head required is 7.47m to be able to produce 90kW from a flow of 1.62m3/s. I don't have the head flow chart for the Crossflow turbine either that I could send you but yeah as you said, we are compelled to use the large pipes.
I will re-do some calculations to check the minimum submergence at the intake to ensure what I calculated before was ok and allow a safety factor.
I have allowed for a DN100 stubbed flange for the vacuum pump connector on the plastic pipe highpoint so I will spec and source a vacuum pump for this application. It is a good idea to connect it to a pressure sensor at the turbine inlet so that it can run automatically when needed so I will look into that.
Also, I have allowed for extra stubbed flanges at the pipe highpoint for air/vacuum valves or combination air valves because I wasn't sure what was needed. Following this discussion, I don't think we'd need either on this system. Do you have any comments on this?
Ok that's fair enough regarding the Heff values, I appreciate the time you've spent looking into this. I will dig deeper into that to see what I can conclude. If anyone else has any comments I would be very interested to hear from you.
Regards,
Steffan
#10
Posted 10 March 2016 - 10:59 AM
Something that just occurred to me now is the need for the plastic pipe to withstand a bit of vacuum. You won't need much vacuum to draw the water up into the section in the culvert, but large diameter pipes are notorious for collapsing under vacuum. You have probably checked that already, but just in case...
#11
Posted 10 March 2016 - 08:11 PM
http://www.ossberger...s-water-plants/
Hi ,
May be interesting to take a look , with reference to efficiency , 80 % up.
The size of the pipe could be enlarged at the mouth of the turbine only .
Breizh
Edited by breizh, 11 March 2016 - 01:50 AM.
#12
Posted 14 March 2016 - 09:32 AM
Hi both,
Katmar - yes that's right. The 4kN twinwall plastic pipe is constructed in box sections and is tested to withstand a negative pressure of up to 0.5 bar. We would be lifting the water by a height of 850mm in the pipe (worst case), so this should be fine.
Breizh - The expected efficiency Ossberger have specified for this turbine is 82% and as mentioned in your link, a higher efficiency can be achieved in some cases but for my calculations I have been using 82% as a design efficiency for the turbine excluding the drive efficiency. If we enlarged the pipe at the mouth of the turbine only, we would still have significant losses along the pipeline due high velocity, elbows in the pipe route etc which is why the large pipes were chosen. However, I understand what you were saying, that if the efficiency was higher, we could afford a higher head loss by using smaller pipes.
Thanks,
Steffan
Similar Topics
Mdea QuestionsStarted by Guest_Board operator_* , 09 Jun 2024 |
|
![]() |
||
![]() Pe Chemical Practice Exam QuestionsStarted by Guest_AthlonXPme_* , 31 Mar 2024 |
|
![]() |
||
Steam Reforming For Hydrogen-QuestionsStarted by Guest_daraj_* , 05 Nov 2021 |
|
![]() |
||
[Pressure Swing Adsorption - Sizing Questions] Step By Step Method ToStarted by Guest_CamilleGroulx_* , 07 Oct 2020 |
|
![]() |
||
Questions About Moving Bed Coal GasifierStarted by Guest_Jade331_* , 18 Aug 2020 |
|
![]() |