Hello guys,
Please, i need information of how to determine the Height of Liquid Volume, h in the vertical vessel and Vertical Seam-to-Seam Length of the vessel, Lss.
Any idea of how to determine the position of the LZA(HH), LA(H), NL, LA(L) and LZA(LL) on the new design vertical vessel once i determine the Liquid volume height.
Thanks for your immediate responce,
Regards
|
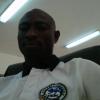
Vertical Vessel Design.
Started by asade abiodun, Nov 20 2006 09:45 AM
4 replies to this topic
Share this topic:
#1
Posted 20 November 2006 - 09:45 AM
#2
Posted 21 November 2006 - 06:29 PM
Asade,
I'm sure good and kind Art Montemayor would be offering his spreadsheet again.
But may I still insist on recommending you to have a look at Shell DEP's for this? If you are working in a design or EPC firm (regardless if your projects are greenfield or brownfield), it is highly likely that you will have access to such similar standards.
Trust me you will find the EXACT instruction on how to determine the position of the high/low pre-alarms and trips.
Having a spreadsheet does reduce your work time to calculate things. But nothing is more important than understanding 'why' is this being done/calculated this/that way.
I'm sure good and kind Art Montemayor would be offering his spreadsheet again.
But may I still insist on recommending you to have a look at Shell DEP's for this? If you are working in a design or EPC firm (regardless if your projects are greenfield or brownfield), it is highly likely that you will have access to such similar standards.
Trust me you will find the EXACT instruction on how to determine the position of the high/low pre-alarms and trips.
Having a spreadsheet does reduce your work time to calculate things. But nothing is more important than understanding 'why' is this being done/calculated this/that way.
#3
Posted 21 November 2006 - 06:50 PM
Mr. Abiodun,
I would second the excellent advise you just received from Radionise. I believe that you have already been sent the referenced spreadsheet from Art Montemayor, and I'm sure you'll find it to be most helpful. However, to fall back on an old cliche, "this is not rocket science". There is nothing overly difficult or tricky in setting up liquid level points in a separator. It's mainly a question of what residence times you want, which can be a function of the quality of your level control systems. There are also some "rule fo thumb" minimums. Of course, you've sized the diameter of the separator to provide for vapor-liquid separation, and you must ensure that the level never rises to a point where your design would be defeated.
I would second the excellent advise you just received from Radionise. I believe that you have already been sent the referenced spreadsheet from Art Montemayor, and I'm sure you'll find it to be most helpful. However, to fall back on an old cliche, "this is not rocket science". There is nothing overly difficult or tricky in setting up liquid level points in a separator. It's mainly a question of what residence times you want, which can be a function of the quality of your level control systems. There are also some "rule fo thumb" minimums. Of course, you've sized the diameter of the separator to provide for vapor-liquid separation, and you must ensure that the level never rises to a point where your design would be defeated.
#4
Posted 21 November 2006 - 07:28 PM
hello,
It is very common design practice in industry. But it differs from one organization to other based on their experiences, owner's preferences & project specifications. I'm trying to put a typical criteria for your concern.
In design vertical vessel, first step is to find out diameter of it based on critical vapor velocity, which i understand you know. The second step is to find out height of vessel. There are two components for it.
(A) Height of liquid levels, and
(
height of vapor space.
Height of liquid level is purely derrived from "residence time" of liquid based on the liquid outlet flow from bottom of vessel. Once you have defined residence time, you can find height based on cross section area of vessel and liquid volumetric flow rate. Following are typical values for residence time.
LZA(HH), LA(H), NL, LA(L) and LZA(LL)
[1] From BTL (bottom tangent line) of vessel to LZA(LL) = 1 to 1.5 minutes OR 150 mm whichever is higher. The minimum 150 mm is due to the allowances of welding for bottom head & shell, level guage nozzle etc.
[2] From LZA(LL) to LA(L) = 1 min. This may increase based on criticality of downstream equipment or pump.
[3] From LA(L) to LA(H) = 5 min.. This is actual working volume.
[4] NL (normal liquid level) : Consider 50% height between LA(L) & LA(H).
[5] From LA(H) to LA(HH) = 1 min.
The second part of height (
has again some criteria based on efficiency of vapor liquid separation, provision of demister pad etc. I'm again providing some typical values.
[1] From LA(HH) to centerline of inlet nozzle = minimum 300 mm or (150 mm + 50% of inlet nozzle diameter) whichever is higher.
[2] From center line of inlet nozzle to bottom of demsiter pad = minimum 300 mm or (150 mm + 50% of inlet nozzle diameter) whichever is higher.
[3] Thickness of demister pad = based on separate calculations.
[4] From top of demister pad to top tangent line of vessel = 150 mm.
Depending on inlet distributor of your vessel, above values may change. Because, there are various kind of distributors which helps to reduce liquid entrainment. Therefore, you can reduce height in vapor space.
One more aspect is L/D ratio of vessel. After calculating total height, you must check for L/D ratio. It should be around 3. You can adjust your liquid height or vapor space in order to keep L/D ration near 3.
You can refer to any of the standard practices of reputed companies for more detail calculations.
I hope this helps.
Thank you,
It is very common design practice in industry. But it differs from one organization to other based on their experiences, owner's preferences & project specifications. I'm trying to put a typical criteria for your concern.
In design vertical vessel, first step is to find out diameter of it based on critical vapor velocity, which i understand you know. The second step is to find out height of vessel. There are two components for it.
(A) Height of liquid levels, and
(

Height of liquid level is purely derrived from "residence time" of liquid based on the liquid outlet flow from bottom of vessel. Once you have defined residence time, you can find height based on cross section area of vessel and liquid volumetric flow rate. Following are typical values for residence time.
LZA(HH), LA(H), NL, LA(L) and LZA(LL)
[1] From BTL (bottom tangent line) of vessel to LZA(LL) = 1 to 1.5 minutes OR 150 mm whichever is higher. The minimum 150 mm is due to the allowances of welding for bottom head & shell, level guage nozzle etc.
[2] From LZA(LL) to LA(L) = 1 min. This may increase based on criticality of downstream equipment or pump.
[3] From LA(L) to LA(H) = 5 min.. This is actual working volume.
[4] NL (normal liquid level) : Consider 50% height between LA(L) & LA(H).
[5] From LA(H) to LA(HH) = 1 min.
The second part of height (

[1] From LA(HH) to centerline of inlet nozzle = minimum 300 mm or (150 mm + 50% of inlet nozzle diameter) whichever is higher.
[2] From center line of inlet nozzle to bottom of demsiter pad = minimum 300 mm or (150 mm + 50% of inlet nozzle diameter) whichever is higher.
[3] Thickness of demister pad = based on separate calculations.
[4] From top of demister pad to top tangent line of vessel = 150 mm.
Depending on inlet distributor of your vessel, above values may change. Because, there are various kind of distributors which helps to reduce liquid entrainment. Therefore, you can reduce height in vapor space.
One more aspect is L/D ratio of vessel. After calculating total height, you must check for L/D ratio. It should be around 3. You can adjust your liquid height or vapor space in order to keep L/D ration near 3.
You can refer to any of the standard practices of reputed companies for more detail calculations.
I hope this helps.
Thank you,
#5
Posted 22 November 2006 - 01:19 AM
I am sending my heartfelt gratitude to you all (Radionise, Djack and Nirav) for this valuable information you have given me.
Thanks for giving us yong engineers your experience to better ourselves.
Thanks to Art also.
Regards,
Thanks for giving us yong engineers your experience to better ourselves.
Thanks to Art also.
Regards,
Similar Topics
Refinery Lpg Deethanizer Column DesignStarted by Guest_Ilyes_* , 15 Feb 2025 |
|
![]() |
||
Alkaline Electrolytic Cell/stack Sizing/design For H2 ProductionStarted by Guest_BRS09_* , 13 Mar 2025 |
|
![]() |
||
Batch Adsorption: H/d Ratio For Vessel SizingStarted by Guest_Victor_process_Engineer_* , 28 Feb 2025 |
|
![]() |
||
![]() Heat Exchanger Network DesignStarted by Guest_Kakashi-01_* , 21 Feb 2025 |
|
![]() |
||
Vertical Ko Drum SizingStarted by Guest_alexzo1990_* , 27 Jan 2025 |
|
![]() |