I know it's inadvisable (or worse) to allow liquid droplets to enter into the suction of a compressor. However, I'd like to know just how bad is it, and how does your change depending on the compressor type?
I understand that even a very small amount of carryover into a high speed centrifugal compressor can be catastrophic. Is that true for dry screw compressors? Presumably it is not true for wet screw. How about for reciprocating compressors? I'd appreciate hearing anything you might like to offer on the topic.
Thanks,
Doug
|
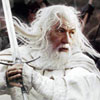
Liquids In Compressor Suction
Started by djack77494, Dec 13 2006 01:55 PM
6 replies to this topic
Share this topic:
#1
Posted 13 December 2006 - 01:55 PM
#2
Posted 13 December 2006 - 02:26 PM
With reciprocating compressors here is what happens. For small amounts, the misting liquids will vaporize because of the heat in the suction bottles. As the amount of liquids increase, the droplets will hit the suction valves and again vaporize because the valves are hot (the heat is from the temperature rise in the cylinder). As more liquids enter and hit the valves, damage will occur, as the liquids vaporize, the heat they absorb causes localized cooling of the metal and the valves will break. Some compressors have metal srings and plates that break easily, plastic materials will hold up better in these conditions.
If the liquid does get through the valves in the liquid form, they will fall (you should have suction on top, discharge on bottom) through the cylinder and they can again vaporize due to heat of compression. At this point, the valves may be broken and gas will pass back and forth through the broken valves cause an increase in average cylinder temperature. Hot suction valves indicate this type of problem.
Finally, a huge amount of liquid will have a hard time getting into a cylinder because the amount of passage area through the suction valves and discharge valves is really small. But with broken suction valves, more liquid can enter than the discharge valves can let out. This large amount of liquids will fill the cylinder so on the next compression cylcle, the cylinder will stop because it cannot push the liquids out. Of course you can not stop the cylinder so some thing will give. The typical breakage point is not the cylinder walls, but the pistong rod, rod pin or crank will fail and the unit should stop because of vibration, pressures errors, or other sensors. Typically there will not be a large escape of gas because the failures are outside the cylinder containing the gas.
If the liquid does get through the valves in the liquid form, they will fall (you should have suction on top, discharge on bottom) through the cylinder and they can again vaporize due to heat of compression. At this point, the valves may be broken and gas will pass back and forth through the broken valves cause an increase in average cylinder temperature. Hot suction valves indicate this type of problem.
Finally, a huge amount of liquid will have a hard time getting into a cylinder because the amount of passage area through the suction valves and discharge valves is really small. But with broken suction valves, more liquid can enter than the discharge valves can let out. This large amount of liquids will fill the cylinder so on the next compression cylcle, the cylinder will stop because it cannot push the liquids out. Of course you can not stop the cylinder so some thing will give. The typical breakage point is not the cylinder walls, but the pistong rod, rod pin or crank will fail and the unit should stop because of vibration, pressures errors, or other sensors. Typically there will not be a large escape of gas because the failures are outside the cylinder containing the gas.
#3
Posted 14 December 2006 - 08:04 AM
Hi. I am very interested in your explaination of the effect of liquid carry over to compressor. Normally, there will be a gas-liquid separator/ knock out pot before enter the compressor. Can you explain in more details using simple drawing? What is the normal checking parameter? Only vibration & noise? How it happen? I saw people calculate on the lube oil dropping rate as well. Appreaciate your expertise advice. Thanks!
#4
Posted 14 December 2006 - 09:07 AM
Hi,
I believe that the purpose of inlet scrubber to the compressor is to remove the water from the feed stream.
If the scrubber is properly sized and the feed composition and water flowrate is well defined, then the compressor should be free from water.
But, when i simulate a three stage compression, the 10 MMSCFD feed entering the suction scrubber contains 1.2E-02 mole fraction of H2O with stream vapor fraction of 0.9989. The gas stream from the scrubber contains 1.01E-02 mole fraction of H2O and stream vapor fraction of 1.
I thought that since my VP is 1, it is assumed that there is negligible or minimal liquid in the stream and my simulation is okay for compression to take place.
I need correction if my assumption is wrong.
I believe that the purpose of inlet scrubber to the compressor is to remove the water from the feed stream.
If the scrubber is properly sized and the feed composition and water flowrate is well defined, then the compressor should be free from water.
But, when i simulate a three stage compression, the 10 MMSCFD feed entering the suction scrubber contains 1.2E-02 mole fraction of H2O with stream vapor fraction of 0.9989. The gas stream from the scrubber contains 1.01E-02 mole fraction of H2O and stream vapor fraction of 1.
I thought that since my VP is 1, it is assumed that there is negligible or minimal liquid in the stream and my simulation is okay for compression to take place.
I need correction if my assumption is wrong.

#5
Posted 15 December 2006 - 11:56 AM
Doug:
This is a not only an interesting topic, it is a topic that – in my experience – can only be learned out in real life, engineering practice. It is very unfortunate that this very important topic and all the real-life applications that are related to it are not even mentioned in University engineering training – much less taught. Nevertheless, it is a subject that must be well understood and appreciated by all engineers dealing with compressible fluids – especially those that specialize in process design. Engineering errors or oversights can prove to be very hazardous, embarrassing, and expensive lessons to learn out in industry.
I spent approximately 12 years process designing, installing, operating, and modifying/dealing with gas compressors immediately after graduation from university. And I was doing 60% of this experience outside the USA, in developing countries and with a minimum of engineering assistance or guidance. However, I had the extreme and fortunate luck of having an excellent mechanical engineer as my mentor the first year and a half. This has to have been the richest and fastest-track learning period of my engineering career. I learned more about compressors – both reciprocating and centrifugals – during this era than most people learn about anything else. And I owe this to my mentor, Alf Newton, and to the excellent opportunities I had. To be thrown into a foreign country without any experience and given authority to design and operate industrial gas plants is a “sink or swim” situation and I have always felt that with this kind of pressure and a good mentor, a young engineer can only perfect him/herself if one is dedicated to self-improvement. I mention this background only because it leads me to advise all who read this thread that what I am about to write is based on real-life experience and situations – all of it real and factual.
One of the basic truths and most helpful technical guidelines I had from Alf was: “Pumps are designed and made to pump liquids; compressors are designed and made to transport gas or vapor. Never, never mis-apply the two.” That is why I always criticize the use of the term “vacuum pump”. This is an obvious misnomer and doesn’t make engineering sense. For the same reason, one never should allow a compressor – whether reciprocating, centrifugal, or screw type – to be fed any liquid fluids mixed in with the gas stream. There are compressor types or designs that are specifically designed to handle a mixture of gas and liquid (such as liquid ring or some screw types); however, these are exceptions rather than the norm and I assume that this thread accepts that premise. The basic, general rule should hold: Never introduce liquids into gas compressors unless specifically advised by the manufacturer.
The general, real-life situation where an engineer is called upon to compress a gas is one where the gas stream is usually “wet” – i.e., it originates from a system where it is in equilibrium with a parent liquid and is, therefore, saturated with that liquid. This doesn’t necessarily mean that the gas phase going to the compressor suction contains liquid particles or slugs. It just means that the gas stream is saturated. This is important to note and to stress that the quantity or quality of the liquid associated with that gas stream as it enters the compressor is often unknown or unproven. What I mean by this is that we experienced engineers often see to it that the gas stream to be compressed is subjected to Knock Out (KO) drums, vapor-liquid separators, or filter separators in order to ensure that all liquid particles (often less than a couple of microns) are separated from that gas entering the compressor. Sometimes this exercise and application is done well; sometimes it is done badly, not at all, or in a horrendous manner. This is what differentiates an experienced design from a “best-effort basis” type of design.
I pause here to mention that I presume I’m addressing experienced and knowledgeable engineers, like you Doug, and that we all understand the basics of phase equilibria. I have read asade abiodun’s comments and I feel that he is not differentiating between the water that is in the gas as a vapor phase and the water that exists as a LIQUID. The point here is that it is the liquid that poses a grave hazard to most compressors – not the water vapor. Any condensable vapor is important to note when applying a multi-stage compressor because there is subsequent condensation of the condensable vapor portion in the downstream stages. This is why it is vital to have an accurate calculation of contained condensables identified as one compresses from stage to stage. Adequate and efficient vapor-liquid separators must be employed to protect each of the subsequent downstream stages of compression by removing all the condensables – water, hydrocarbon, or any others.
And now for the Alf Newton seminar on why liquids are not allowed to enter compressors: Liquids are, as most engineers will admit, classed as incompressible – that is, they will not submit well to a reduction in the volume they occupy. As a result, if one tries to compress a liquid, it will be discovered all that happens is that a rapid and exponential increase in hydraulic pressure is produced – almost immediately! In fact, if one ponders for a while, that is precisely the basis of Pascal’s Law and how powerful hydraulic presses operate – using a liquid to impose tremendous forces on a piston and cylinder combination. Basic Physics then tells us that if we try to impose a hydraulic force on a compressor cylinder without it being designed to adequately deal with it and relieve itself if need be, then we are in deep trouble. Always remember that a compressor such as a reciprocating type is directly connected to a power source such as an electric motor or turbine and will do everything within its design capability to transmit that same work force into the working fluid. It is merely a stupid machine in the hands of a supposedly intelligent human engineer. If it meets a resistance (such as inlet and discharge valves) that does not permit transmission or relief of that force, it will continue to exert itself until relief (or driver failure) is reached. Often, the resulting effect of a reciprocating compressor failing to “compress” an incompressible fluid such as water will result in a mechanical failure rather than a driver failure (such as a power disconnect or shutdown). What this mechanical failure turns out to be depends on the magnitude of the force(s) generated and the type of machine. You really don’t want to be around the machine should this occur; the results are sometimes very catastrophic. I have been (and seen) to the sites of some really sad and bad failures. And all of these compressor failures could easily have been totally avoided! All that happened was that there was ignorance or disinterest in how a compressor works (or should work) and how to ensure that it (and the operators) are safely protected.
I have personally extracted cast iron pistons from compressor cylinders that had valve pieces (nuts, bolts, and steel chunks) embedded into the piston face because the valves were shattered by liquid forces generated when the compressor was allowed to ingest liquid. The compressor in question was connected to so much horsepower that once the incident occurred, the machine continued to literally pound the pieces of valve(s) that fell into the cylinder for a time after the failure. This was not a bad event – it was fortunate for the operators that this happened because all that was lost was the valves, the piston, and some bearings. Worse and more dangerous situations have occurred where the piston rods and the connecting rods have been bent beyond repair. One incident resulted in a connecting rod bending and rupturing such that it broke out of the cast iron crankcase! Bear in mind that almost all compressor crankcases are of cast iron – the same material that make up grenades because it produces a shattered spray of shrapnel. Another case was one where a horizontal cylinder blew out its cover head plate. It was blown through a brick wall and out of a building. The worse one I have seen is where a cast iron crankshaft broke into pieces and totally ruptured the crankcase. That is why I never, ever allow cast iron crankshafts to be used on compressors. I know of many engineers that don’t know that some manufacturers will furnish compressors with cast iron crankshafts. I always insist and demand forged steel crankshafts on compressors because of the above possibility. When you generate hydraulic forces, you must be prepared to confront the results and capable of controlling them. Nothing in the usual design of a gas compressor addresses this need. I can tell you from personal experience that what vicini has described is not accurate. The effects are much worse and instantly quicker than what is described.
I am presently expediting the application of two, 1,000 hp, 3-stage, reciprocating natural gas compressors that will be installed next to two other, similar ones. The existing compressors had a bad and sad case of bad design engineering where the inlet, saturated gas separator used a cheap and un-calibrated dP cell transmitter to control the liquid level. No visual level gage was employed on the separator (as well as on the other two separators) and operators were unable to calibrate the level transmitter or to detect the actual level of the liquid in the separator(s). The predictable event happened. Two cylinders underwent total suction valve ruptures and compressor cylinder damage. We’re talking about million-dollar machines damaged due to a stupid design oversight or technical naivety. This is a clear case where design engineers failed to recognize what is a well-known field problem. I am finding more and more that today’s young graduate engineers unfortunately lack the quality and the opportunity of having experienced and capable engineering mentors to guide them through the early years of their career and without this “jump-start”, they lack the ability to recognize what is an obvious engineering stumbling block.
There is no practical or dependable way to see or detect liquid droplets or particles going into a compressor cylinder. There is only the tell-tale signs left AFTER the destructive effects have taken place. Therefore, my advice to young engineers is: simply don’t go there! In other words, avoid this situation and design for NO liquids being able to enter the compressor. This involves efficient 2-phase separators, low superficial velocities, liquid level detection and control (complete with alarm and shut down points), good temperature control, and reliable drain valves and actuators.
I am also finding the same topic taking a prominent role these days in what is considered a basic, industrial application: mechanical refrigeration cycles and systems. Adequate and efficient protection must be provided to the refrigeration compressor – regardless of the type. A liquid is harmful to a compressor not only because it imposes hydraulic forces. It also imparts an effect of literally “washing away” any protective and lubricating effects of compressor oil. This has harmful effects on the rotors or impellers used on some dynamic or positive displacement machines. Internal bearings suffer due to the type of liquid contaminant entering the machine. Centrifugal machines suffer traumatic damage due to the impact forces imposed on their moving parts – particularly the impellers. All of this reinforces the basics of the Alf Newton philosophy: compressors are not (and never were) designed to handle liquids! If one insists on introducing a 2-phase mixture into a gas compressor, one must do it either with total responsibility for the end results or with the blessings of the manufacturer. I prefer the latter – it’s more logical, safer, and it makes for common engineering sense.
I apologize for this long (and probably boring) dissertation on one of my favorite subjects. I thought you would like to have full explanations for some of the things that I take for granted as general knowledge and possibly not known to many young engineering graduates.
I hope this experience helps out.
This is a not only an interesting topic, it is a topic that – in my experience – can only be learned out in real life, engineering practice. It is very unfortunate that this very important topic and all the real-life applications that are related to it are not even mentioned in University engineering training – much less taught. Nevertheless, it is a subject that must be well understood and appreciated by all engineers dealing with compressible fluids – especially those that specialize in process design. Engineering errors or oversights can prove to be very hazardous, embarrassing, and expensive lessons to learn out in industry.
I spent approximately 12 years process designing, installing, operating, and modifying/dealing with gas compressors immediately after graduation from university. And I was doing 60% of this experience outside the USA, in developing countries and with a minimum of engineering assistance or guidance. However, I had the extreme and fortunate luck of having an excellent mechanical engineer as my mentor the first year and a half. This has to have been the richest and fastest-track learning period of my engineering career. I learned more about compressors – both reciprocating and centrifugals – during this era than most people learn about anything else. And I owe this to my mentor, Alf Newton, and to the excellent opportunities I had. To be thrown into a foreign country without any experience and given authority to design and operate industrial gas plants is a “sink or swim” situation and I have always felt that with this kind of pressure and a good mentor, a young engineer can only perfect him/herself if one is dedicated to self-improvement. I mention this background only because it leads me to advise all who read this thread that what I am about to write is based on real-life experience and situations – all of it real and factual.
One of the basic truths and most helpful technical guidelines I had from Alf was: “Pumps are designed and made to pump liquids; compressors are designed and made to transport gas or vapor. Never, never mis-apply the two.” That is why I always criticize the use of the term “vacuum pump”. This is an obvious misnomer and doesn’t make engineering sense. For the same reason, one never should allow a compressor – whether reciprocating, centrifugal, or screw type – to be fed any liquid fluids mixed in with the gas stream. There are compressor types or designs that are specifically designed to handle a mixture of gas and liquid (such as liquid ring or some screw types); however, these are exceptions rather than the norm and I assume that this thread accepts that premise. The basic, general rule should hold: Never introduce liquids into gas compressors unless specifically advised by the manufacturer.
The general, real-life situation where an engineer is called upon to compress a gas is one where the gas stream is usually “wet” – i.e., it originates from a system where it is in equilibrium with a parent liquid and is, therefore, saturated with that liquid. This doesn’t necessarily mean that the gas phase going to the compressor suction contains liquid particles or slugs. It just means that the gas stream is saturated. This is important to note and to stress that the quantity or quality of the liquid associated with that gas stream as it enters the compressor is often unknown or unproven. What I mean by this is that we experienced engineers often see to it that the gas stream to be compressed is subjected to Knock Out (KO) drums, vapor-liquid separators, or filter separators in order to ensure that all liquid particles (often less than a couple of microns) are separated from that gas entering the compressor. Sometimes this exercise and application is done well; sometimes it is done badly, not at all, or in a horrendous manner. This is what differentiates an experienced design from a “best-effort basis” type of design.
I pause here to mention that I presume I’m addressing experienced and knowledgeable engineers, like you Doug, and that we all understand the basics of phase equilibria. I have read asade abiodun’s comments and I feel that he is not differentiating between the water that is in the gas as a vapor phase and the water that exists as a LIQUID. The point here is that it is the liquid that poses a grave hazard to most compressors – not the water vapor. Any condensable vapor is important to note when applying a multi-stage compressor because there is subsequent condensation of the condensable vapor portion in the downstream stages. This is why it is vital to have an accurate calculation of contained condensables identified as one compresses from stage to stage. Adequate and efficient vapor-liquid separators must be employed to protect each of the subsequent downstream stages of compression by removing all the condensables – water, hydrocarbon, or any others.
And now for the Alf Newton seminar on why liquids are not allowed to enter compressors: Liquids are, as most engineers will admit, classed as incompressible – that is, they will not submit well to a reduction in the volume they occupy. As a result, if one tries to compress a liquid, it will be discovered all that happens is that a rapid and exponential increase in hydraulic pressure is produced – almost immediately! In fact, if one ponders for a while, that is precisely the basis of Pascal’s Law and how powerful hydraulic presses operate – using a liquid to impose tremendous forces on a piston and cylinder combination. Basic Physics then tells us that if we try to impose a hydraulic force on a compressor cylinder without it being designed to adequately deal with it and relieve itself if need be, then we are in deep trouble. Always remember that a compressor such as a reciprocating type is directly connected to a power source such as an electric motor or turbine and will do everything within its design capability to transmit that same work force into the working fluid. It is merely a stupid machine in the hands of a supposedly intelligent human engineer. If it meets a resistance (such as inlet and discharge valves) that does not permit transmission or relief of that force, it will continue to exert itself until relief (or driver failure) is reached. Often, the resulting effect of a reciprocating compressor failing to “compress” an incompressible fluid such as water will result in a mechanical failure rather than a driver failure (such as a power disconnect or shutdown). What this mechanical failure turns out to be depends on the magnitude of the force(s) generated and the type of machine. You really don’t want to be around the machine should this occur; the results are sometimes very catastrophic. I have been (and seen) to the sites of some really sad and bad failures. And all of these compressor failures could easily have been totally avoided! All that happened was that there was ignorance or disinterest in how a compressor works (or should work) and how to ensure that it (and the operators) are safely protected.
I have personally extracted cast iron pistons from compressor cylinders that had valve pieces (nuts, bolts, and steel chunks) embedded into the piston face because the valves were shattered by liquid forces generated when the compressor was allowed to ingest liquid. The compressor in question was connected to so much horsepower that once the incident occurred, the machine continued to literally pound the pieces of valve(s) that fell into the cylinder for a time after the failure. This was not a bad event – it was fortunate for the operators that this happened because all that was lost was the valves, the piston, and some bearings. Worse and more dangerous situations have occurred where the piston rods and the connecting rods have been bent beyond repair. One incident resulted in a connecting rod bending and rupturing such that it broke out of the cast iron crankcase! Bear in mind that almost all compressor crankcases are of cast iron – the same material that make up grenades because it produces a shattered spray of shrapnel. Another case was one where a horizontal cylinder blew out its cover head plate. It was blown through a brick wall and out of a building. The worse one I have seen is where a cast iron crankshaft broke into pieces and totally ruptured the crankcase. That is why I never, ever allow cast iron crankshafts to be used on compressors. I know of many engineers that don’t know that some manufacturers will furnish compressors with cast iron crankshafts. I always insist and demand forged steel crankshafts on compressors because of the above possibility. When you generate hydraulic forces, you must be prepared to confront the results and capable of controlling them. Nothing in the usual design of a gas compressor addresses this need. I can tell you from personal experience that what vicini has described is not accurate. The effects are much worse and instantly quicker than what is described.
I am presently expediting the application of two, 1,000 hp, 3-stage, reciprocating natural gas compressors that will be installed next to two other, similar ones. The existing compressors had a bad and sad case of bad design engineering where the inlet, saturated gas separator used a cheap and un-calibrated dP cell transmitter to control the liquid level. No visual level gage was employed on the separator (as well as on the other two separators) and operators were unable to calibrate the level transmitter or to detect the actual level of the liquid in the separator(s). The predictable event happened. Two cylinders underwent total suction valve ruptures and compressor cylinder damage. We’re talking about million-dollar machines damaged due to a stupid design oversight or technical naivety. This is a clear case where design engineers failed to recognize what is a well-known field problem. I am finding more and more that today’s young graduate engineers unfortunately lack the quality and the opportunity of having experienced and capable engineering mentors to guide them through the early years of their career and without this “jump-start”, they lack the ability to recognize what is an obvious engineering stumbling block.
There is no practical or dependable way to see or detect liquid droplets or particles going into a compressor cylinder. There is only the tell-tale signs left AFTER the destructive effects have taken place. Therefore, my advice to young engineers is: simply don’t go there! In other words, avoid this situation and design for NO liquids being able to enter the compressor. This involves efficient 2-phase separators, low superficial velocities, liquid level detection and control (complete with alarm and shut down points), good temperature control, and reliable drain valves and actuators.
I am also finding the same topic taking a prominent role these days in what is considered a basic, industrial application: mechanical refrigeration cycles and systems. Adequate and efficient protection must be provided to the refrigeration compressor – regardless of the type. A liquid is harmful to a compressor not only because it imposes hydraulic forces. It also imparts an effect of literally “washing away” any protective and lubricating effects of compressor oil. This has harmful effects on the rotors or impellers used on some dynamic or positive displacement machines. Internal bearings suffer due to the type of liquid contaminant entering the machine. Centrifugal machines suffer traumatic damage due to the impact forces imposed on their moving parts – particularly the impellers. All of this reinforces the basics of the Alf Newton philosophy: compressors are not (and never were) designed to handle liquids! If one insists on introducing a 2-phase mixture into a gas compressor, one must do it either with total responsibility for the end results or with the blessings of the manufacturer. I prefer the latter – it’s more logical, safer, and it makes for common engineering sense.
I apologize for this long (and probably boring) dissertation on one of my favorite subjects. I thought you would like to have full explanations for some of the things that I take for granted as general knowledge and possibly not known to many young engineering graduates.
I hope this experience helps out.
#6
Posted 19 December 2006 - 04:33 AM
Thanks Art,
For your correction have open my eyes.
Actually the liquid i was talking about is in the vapor phase.
Majority of the liquid is in the aqueous phase, i only thought that once i use a scrubber, all liquids should go to the aqueous phase.
Thanks once again Art.
For your correction have open my eyes.
Actually the liquid i was talking about is in the vapor phase.
Majority of the liquid is in the aqueous phase, i only thought that once i use a scrubber, all liquids should go to the aqueous phase.
Thanks once again Art.
#7
Posted 19 December 2006 - 09:31 AM
Thanks Art,
That was a long post, indeed, but not at all boring.
That was a long post, indeed, but not at all boring.
Similar Topics
![]() Hysys Expander/compressor Input Using Dimensionless CurveStarted by Guest_Alfreedo_* , 21 Apr 2025 |
|
![]() |
||
Centriugal CompressorStarted by Guest_Rahimzadeh_* , 02 Mar 2025 |
|
![]() |
||
Pulsation Device In Reciprocating CompressorStarted by Guest_zaidanamir_* , 17 Feb 2025 |
|
![]() |
||
Recip Compressor Discharge PrvsStarted by Guest_go-fish_* , 15 Oct 2022 |
|
![]() |
||
![]() Restricted Orifice (Ro) After The Reciprocating Compressor? Why?Started by Guest_VolereePotere_* , 24 May 2023 |
|
![]() |