A heat exchanger was used for many many years. This exchanger was cleaned during T/A last May. 3 months after May, we experienced a very significant loss in the heat transfer rate. Seems like fouling had been occured. Thus, we isolated and hydroblasted it. Now, 2 months after we cleaned it up, we are noticing what seems to be fouling situation on this heat exchanger.
Initially, we thought that the velocity of fluid through this heat exchanger was too slow. We increased the flow rate. However, increasing the flow rate did not seem to help at all.
My question is.... what may have caused this loss of performance on the heat exchanger?
FYI, this heat exchanger is exchanging heat between lean and rich amine. When we cleaned it up last May, we analyzed the deposit on both the tubes and shell sides. Approximately 65% of the deposits(for both shell and tubes sides) are iron and approximately 30% of are sulfides. Does this indicate a really bad corrossion issue? For the senior engineers, what are your recommendation(s) to mitigate this issue?
Thanks.
|
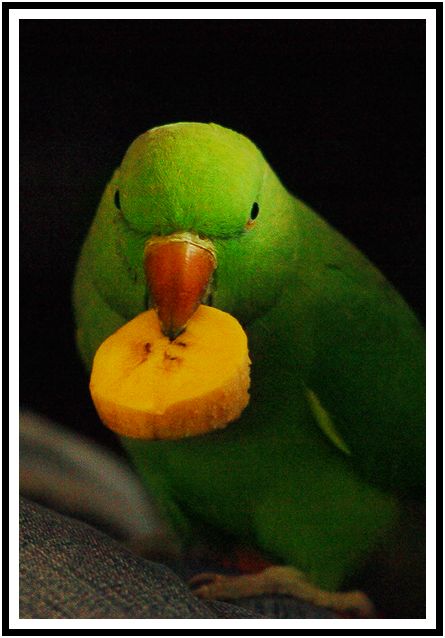
Heat Exchanger Fouling Problem
Started by dylant, Sep 23 2007 09:26 PM
3 replies to this topic
Share this topic:
#1
Posted 23 September 2007 - 09:26 PM
#2
Posted 24 September 2007 - 07:10 AM
Dylant:
You haven’t stated it outright, so I’ll make the following assumptions:
The exchanger in question is a Lean-Rich Amine heat exchanger that is found directly downstream of the Amine reboiler on an Amine regeneration unit.
These exchangers were normally supplied as two units, in series, to avoid temperature crosses; today they are usually supplied as one, multi-tube pass unit; I assume this is what you have;
I have always employed stainless steel tubes in my Lean-Rich Amine exchangers; you describe what seems to be carbon steel tubes; I would change out the tubes to 316 ELC stainless for starters;
I have never had a bad experience with Amine heat exchangers – as long as I kept the Amine solution clean and in good chemical condition. I never added any additive, “de-foamers”, “Amine guards”, surfactants, etc., etc. I always did the plain, ordinary, common horse sense thing of keeping the solution clean and pure and I never had corrosion, foaming, or fouling. And I’ve designed, installed, operated, and retro-fitted a lot of Amine units – going back to my first assignment out of college which was in Jamaica, West Indies.
When you run an Amine unit with clean, pure solution you have no fouling – period. But in order to ensure that your solution is clean and is kept that way you must regenerate properly, re-distill constantly, and/or apply efficient activated carbon adsorption on 100% of your solution. My MEA was always “horse piss” pure – in other words, the solution samples came out like the light color of horse urine – a sign that the solution is perfectly clean. This kind of solution gives you no problems nor is it corrosive.
I assume you are using MDEA, although you don’t say which Amine you are using;
The best (and surest) mitigation against Amine corrosion and fouling is a clean, pure solution. It sounds like you are far from it.
If you need further comments or help you must tell us the basic data. You have not told us the type of unit, the size of unit, the gas treated, the impurities, the circulation load, the designer, the CO2 loadings, the solution strength, etc., etc., etc………………..
#3
Posted 05 November 2007 - 06:42 AM
Corrosion rates increase with increasing temperature, particularly in rich amine service. Temperatures above about 220oF (104oC) can result in acid gas flashing and severe localized corrosion if the pressure drop is high enough.
The rich amine side of the lean/rich exchangers, hot lean amine piping, hot rich amine piping, the amine solution pumps, and the reclaimers are also areas where corrosion problems occur.
The Amine system design should incorporate measures to control local pressure drop to minimize flashing. In areas where it is unavoidable, upgrading to 300 Series SS or other corrosion resistant alloys may be required. SS410 trays and internals are also used in absorber and stripping towers.
Luis Marques
The rich amine side of the lean/rich exchangers, hot lean amine piping, hot rich amine piping, the amine solution pumps, and the reclaimers are also areas where corrosion problems occur.
The Amine system design should incorporate measures to control local pressure drop to minimize flashing. In areas where it is unavoidable, upgrading to 300 Series SS or other corrosion resistant alloys may be required. SS410 trays and internals are also used in absorber and stripping towers.
Luis Marques
#4
Posted 22 November 2007 - 03:46 PM
Dylant,
What is the type of amine used in this particular unit? Check your lean and reach amine load. Do you operate your regenerator tower properly? Have you experienced any changes in feed (sour gas) quality or flow rate? Have you tried to increase amine circulation rate and/or regenerator reboiler temperature, and what are the effects? What is the colour of your lean amine?
There are so many questions to be answered before any action can be taken.
What is the type of amine used in this particular unit? Check your lean and reach amine load. Do you operate your regenerator tower properly? Have you experienced any changes in feed (sour gas) quality or flow rate? Have you tried to increase amine circulation rate and/or regenerator reboiler temperature, and what are the effects? What is the colour of your lean amine?
There are so many questions to be answered before any action can be taken.
Similar Topics
Steam Pressure In Heat ExchangerStarted by Guest_mvanrijnbach_* , 15 Apr 2025 |
|
![]() |
||
Heat Exchanger Steam FlowStarted by Guest_aliebrahem17_* , 25 Nov 2024 |
|
![]() |
||
Discussion - Predict Storage Tank Heat Transfer Precisely By Jimmy D KStarted by Guest_raj shekhar_* , 25 Mar 2025 |
|
![]() |
||
Cross Over Temperature In Countercurrent Heat ExchangerStarted by Guest_panoska_* , 18 Feb 2025 |
|
![]() |
||
Aspen Hysys - Blowdown Utility Heat Flux MethodStarted by Guest_yuvi.ardekar1999@gmail.com_* , 27 Feb 2025 |
|
![]() |