We frequently encounter pressure vessels which are also designed for full vacuum as per datasheet.
But from fundamentals of physics we know that full vacuum is not practically possible to achieve. I mean as we go from atmospheric pressure towards full vacuum, we need more robust construction so that the vessel may not fail. It is possible to approach full vacuum this way, but as soon as we reach full vacuum , there will be no molecules in the system and the volume should be zero, I mean the vessel will collapse. Correct me if I am wrong in my understanding.
My question is when we specify full vacuum in datasheets for pressure vessels, what is the exact value of vacuum we are specifying? Do we really mean it shall be designed for FULL VACUUM?
|
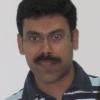
Design Vacuum
Started by benoyjohn, Apr 01 2004 04:20 AM
2 replies to this topic
Share this topic:
#1
Posted 01 April 2004 - 04:20 AM
#2
Posted 01 April 2004 - 12:55 PM
Benoy:
Allow me to address your direct question(s) first,
1) The exact value of vacuum you are specifying is 15 psi - according to the ASME code in the USA; it may be different in other countries or other codes, I don't know.
2) We really mean it shall be designed for FULL VACUUM (full vacuum being defined as 15 psi of external pressure).
Since Chemical Engineers often are called upon to carry out Project Engineering positions (I was, for some years & it was the most interesting and diversified part of my career), we often have to work with and relate to Mechanical Engineering standards, customs, and codes. The ASME code is the main topic of interest here. One of the best and most practical books ever written (in my opinion) is one that is seldom enjoyed by Chem E.'s and can still be obtained through the Internet. This book will often come up in future discussions and references for those practicing as project engineers:
Pressure Vessel Handbook
by Eugene F. Megyesy
Pressure Vessel Handbook Publishing, Inc.
P. O. Box 35365; Tulsa, OK 74135
I highly recommend this book to all Chem E's - especially those that will eventually have to face up to filling in Specification Sheets for vessels. It is one of the most practical and profitable books you will ever buy - and it's fun to read! I'm going to quote from Megyesy's Section on "External Pressure" (note that Mech. E's often talk about external pressure, while Chem. E's identify with "vacuum" - it's all the same, most of the time):
"Design Pressure-
Vessels intended for service under external working pressures of 15 psi or less, which are to be stamped with the Code symbol denoting compliance with the rules for external pressure, shall be designed for a maximum allowable external pressue of 15 psi or 25% more than the maximum possible external pressure, whichever is smaller. Code UG-28(f)
A vessel which is designed and constructed to Code requirements for internal pressure and which is required to be designed for an external pressure of 15 psi or less need not be designed to Code rules for the external pressure condition. However, no external pessure rating may be shown with the Code stamping unless Code requirements for external pressure are met. Code UG-28(f) note.
This shall not be applied if the vessel is operated at a temperature below minus 20 oF and the design pressure is determined by the Code UCS-66 -© (2) or Code UHA-51 -(B) to avoid the necessity of impact test."
Megyesy goes on to give calculation examples of heads, cylindrical shells, and other components under "external pressure".
The reason I'm citing all this information is because the subject is very, very important and one which (in my experience) Mechanical Engineers are better versed and trained in than Chemical Engineers. This is unfortunate, but not something that can't be overcomed. Of course, one has to take the initiative and that is why I always recommend Megyesy's book. It's a start to understanding the art and skill of how and why pressure vessels are designed, fabricated and installed the way they are. We already know the way they are operated; we need to know the other three aspects of a pressure vessel.
Note that although the vessel may be able to handle a partial vacuum, we have no way of knowing that via the ASME code stamp. We have to specify that the calculations be done and the ASME stamp carry the information. And this should be done at the time the Specification Sheet is prepared and prior to submitting it to a designer/fabricator. The reason I state all this is because we all know (or should know) that Chemical Engineers play a very significant role in the design of a pressure vessel - whether we want to admit it or not. For example, it is the Chem E. that is the source of knowing whether a process system that is handling/filled with a condensible vapor that can, upon shutdown, totally condense and immediately produce a total vacuum. One cannot normally expect the Mechanical Engineer encharged with preliminarily designing the vessel to be aware of the process variables. Therefore, a process/project Chem E. must play a very important role in the vessel's design up-front and during it's fabrication. A knowledge of its strength (MAWP & MAWV) are certainly a pre-requisite when it comes time to design and rate the required safety relief devices! And don't forget that it is the Owner and his engineers who are held legally responsible for knowing and controlling the pressure and safety limits of all equipment installed in a process plant or environment -- this is the law in the USA and in most western countries.
Please excuse my long and extended "tirade" on vacuum design; it's a subject I consider important due to my experience and I've found that many young Chem. E.s are starved of information on it. I believe it is important to know of the dangers involving a vessel's failure due to pressure and vacuum conditions. I hope I've succeeded in addressing your questions and given you a logical response.
Art Montemayor
Allow me to address your direct question(s) first,
1) The exact value of vacuum you are specifying is 15 psi - according to the ASME code in the USA; it may be different in other countries or other codes, I don't know.
2) We really mean it shall be designed for FULL VACUUM (full vacuum being defined as 15 psi of external pressure).
Since Chemical Engineers often are called upon to carry out Project Engineering positions (I was, for some years & it was the most interesting and diversified part of my career), we often have to work with and relate to Mechanical Engineering standards, customs, and codes. The ASME code is the main topic of interest here. One of the best and most practical books ever written (in my opinion) is one that is seldom enjoyed by Chem E.'s and can still be obtained through the Internet. This book will often come up in future discussions and references for those practicing as project engineers:
Pressure Vessel Handbook
by Eugene F. Megyesy
Pressure Vessel Handbook Publishing, Inc.
P. O. Box 35365; Tulsa, OK 74135
I highly recommend this book to all Chem E's - especially those that will eventually have to face up to filling in Specification Sheets for vessels. It is one of the most practical and profitable books you will ever buy - and it's fun to read! I'm going to quote from Megyesy's Section on "External Pressure" (note that Mech. E's often talk about external pressure, while Chem. E's identify with "vacuum" - it's all the same, most of the time):
"Design Pressure-
Vessels intended for service under external working pressures of 15 psi or less, which are to be stamped with the Code symbol denoting compliance with the rules for external pressure, shall be designed for a maximum allowable external pressue of 15 psi or 25% more than the maximum possible external pressure, whichever is smaller. Code UG-28(f)
A vessel which is designed and constructed to Code requirements for internal pressure and which is required to be designed for an external pressure of 15 psi or less need not be designed to Code rules for the external pressure condition. However, no external pessure rating may be shown with the Code stamping unless Code requirements for external pressure are met. Code UG-28(f) note.
This shall not be applied if the vessel is operated at a temperature below minus 20 oF and the design pressure is determined by the Code UCS-66 -© (2) or Code UHA-51 -(B) to avoid the necessity of impact test."
Megyesy goes on to give calculation examples of heads, cylindrical shells, and other components under "external pressure".
The reason I'm citing all this information is because the subject is very, very important and one which (in my experience) Mechanical Engineers are better versed and trained in than Chemical Engineers. This is unfortunate, but not something that can't be overcomed. Of course, one has to take the initiative and that is why I always recommend Megyesy's book. It's a start to understanding the art and skill of how and why pressure vessels are designed, fabricated and installed the way they are. We already know the way they are operated; we need to know the other three aspects of a pressure vessel.
Note that although the vessel may be able to handle a partial vacuum, we have no way of knowing that via the ASME code stamp. We have to specify that the calculations be done and the ASME stamp carry the information. And this should be done at the time the Specification Sheet is prepared and prior to submitting it to a designer/fabricator. The reason I state all this is because we all know (or should know) that Chemical Engineers play a very significant role in the design of a pressure vessel - whether we want to admit it or not. For example, it is the Chem E. that is the source of knowing whether a process system that is handling/filled with a condensible vapor that can, upon shutdown, totally condense and immediately produce a total vacuum. One cannot normally expect the Mechanical Engineer encharged with preliminarily designing the vessel to be aware of the process variables. Therefore, a process/project Chem E. must play a very important role in the vessel's design up-front and during it's fabrication. A knowledge of its strength (MAWP & MAWV) are certainly a pre-requisite when it comes time to design and rate the required safety relief devices! And don't forget that it is the Owner and his engineers who are held legally responsible for knowing and controlling the pressure and safety limits of all equipment installed in a process plant or environment -- this is the law in the USA and in most western countries.
Please excuse my long and extended "tirade" on vacuum design; it's a subject I consider important due to my experience and I've found that many young Chem. E.s are starved of information on it. I believe it is important to know of the dangers involving a vessel's failure due to pressure and vacuum conditions. I hope I've succeeded in addressing your questions and given you a logical response.
Art Montemayor
#3
Posted 20 October 2010 - 05:16 PM
dear art,
thanks for giving such a useful clarification.
thanks for giving such a useful clarification.
Similar Topics
Refinery Lpg Deethanizer Column DesignStarted by Guest_Ilyes_* , 15 Feb 2025 |
|
![]() |
||
Alkaline Electrolytic Cell/stack Sizing/design For H2 ProductionStarted by Guest_BRS09_* , 13 Mar 2025 |
|
![]() |
||
![]() Heat Exchanger Network DesignStarted by Guest_Kakashi-01_* , 21 Feb 2025 |
|
![]() |
||
Vacuum RecoveryStarted by Guest_Paper_* , 25 Feb 2025 |
|
![]() |
||
Gas-Liquid Separator Design With CondenserStarted by Guest_shambola_* , 16 Jan 2025 |
|
![]() |