|
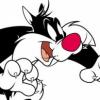
Oil-free Rotary Screw Compressor
Started by Zauberberg, Dec 31 2008 12:05 PM
11 replies to this topic
Share this topic:
#1
Posted 31 December 2008 - 12:05 PM
Good evening to forum members and happy New Year's Eve,
I am looking to find some more information related to possible causes of excessive discharge temperature for the air compressor. The compressor is two-stage rotary screw machine, oil-free, with an interstage and final discharge air cooling system.
There's nothing specific with regard to this unit; two compressors operate in parallel (lead/lag), with exactly the same process parameters (1st stage suction pressure and temperature, and 2nd stage suction pressure and temperature are equal for both machines). Compressor A exhibits high discharge temperatures (231C), while compressor B operates with normal/design discharge temperature (200C). Compressor A, apart from discharge temperature issues, also develops slightly lower air flow. At the time being, only compressor B is running which is sufficient to maintain air demands.
Both machines are packaged and enclosed within the metal box, and it's quite difficult to perform any troubleshooting without disassembling the unit. Since both compressor systems have identical performance up to the 2nd stage, my guess was that it could be related to mechanical integrity problems of the 2nd stage machine. I was hoping to get some guidance regarding this issue.
Best wishes in 2009,
I am looking to find some more information related to possible causes of excessive discharge temperature for the air compressor. The compressor is two-stage rotary screw machine, oil-free, with an interstage and final discharge air cooling system.
There's nothing specific with regard to this unit; two compressors operate in parallel (lead/lag), with exactly the same process parameters (1st stage suction pressure and temperature, and 2nd stage suction pressure and temperature are equal for both machines). Compressor A exhibits high discharge temperatures (231C), while compressor B operates with normal/design discharge temperature (200C). Compressor A, apart from discharge temperature issues, also develops slightly lower air flow. At the time being, only compressor B is running which is sufficient to maintain air demands.
Both machines are packaged and enclosed within the metal box, and it's quite difficult to perform any troubleshooting without disassembling the unit. Since both compressor systems have identical performance up to the 2nd stage, my guess was that it could be related to mechanical integrity problems of the 2nd stage machine. I was hoping to get some guidance regarding this issue.
Best wishes in 2009,
#2
Posted 05 January 2009 - 09:45 PM
Zauberberg,
I understood both machine are mechanically same. Please confirm.
When you said lead / lag operation, are the loading / unloading pressure setting different for both machines ? This may create some level of different in temperature.
Can symmetrical pipe routing and equipment arrangement contributes ? Slight different in backpressure may cause some changes in temperature.
Are FAT performance records same for both machines ? Any chances to obtain the machine efficiency ? Can the performance curve tell that machine are mechanically different ?
I understood both machine are mechanically same. Please confirm.
When you said lead / lag operation, are the loading / unloading pressure setting different for both machines ? This may create some level of different in temperature.
Can symmetrical pipe routing and equipment arrangement contributes ? Slight different in backpressure may cause some changes in temperature.
Are FAT performance records same for both machines ? Any chances to obtain the machine efficiency ? Can the performance curve tell that machine are mechanically different ?
#3
Posted 06 January 2009 - 01:25 PM
Thanks Joe,
Actually what I did was to gather shift operator log sheets and look at trends of both stage suction and discharge temperatures. It was obvious that the increase of 2nd stage discharge temperature was gradual, it was continuously progressing during the last three months. If you put P2/P1 versus T2/T1 on the graph, I believe you can observe if there is any mechanical issue (loss of efficiency would change the polytropic or adiabatic exponent). However, this was not the case for the air compressor. That made me think of partially plugged air cooler and/or air filter in the compressor A, which happens quite frequenly with air compressors. Another fact supporting this theory is that aftercooler of compressor A has sufficiently lower outlet temperature than the aftercooler of compressor B, in spite of tremendously higher inlet temperature. This can happen in the case of reduced airflow through the compressor A which, again, points out at partial pluggage within the compressor A assembly.
Actually what I did was to gather shift operator log sheets and look at trends of both stage suction and discharge temperatures. It was obvious that the increase of 2nd stage discharge temperature was gradual, it was continuously progressing during the last three months. If you put P2/P1 versus T2/T1 on the graph, I believe you can observe if there is any mechanical issue (loss of efficiency would change the polytropic or adiabatic exponent). However, this was not the case for the air compressor. That made me think of partially plugged air cooler and/or air filter in the compressor A, which happens quite frequenly with air compressors. Another fact supporting this theory is that aftercooler of compressor A has sufficiently lower outlet temperature than the aftercooler of compressor B, in spite of tremendously higher inlet temperature. This can happen in the case of reduced airflow through the compressor A which, again, points out at partial pluggage within the compressor A assembly.
#4
Posted 07 January 2009 - 10:55 AM
Dear friend Zauberberg Hello,
I like 'as always' your two way problem solving and analytical approach.
We all must learn and adopt the same for our professional challenges.
You often 'In parallel' put things to forum colleagues without stopping your own problem solving analytical effort.
Which is Excellent example for our youth and student colleagues.
Best regards
Qalander
#5
Posted 07 January 2009 - 11:32 AM
Any possibility to check pressure drop across the Air cooler ? It probably can tell if partially blockage in the air cooler.
The temperature ratio are not big different (just a few %). As mentioned earlier, different pressure setting may lead to different temperature. Set them at same basis and check the different. Just wanna to verify different pressure setting is not the cause.
The temperature ratio are not big different (just a few %). As mentioned earlier, different pressure setting may lead to different temperature. Set them at same basis and check the different. Just wanna to verify different pressure setting is not the cause.
#6
Posted 09 January 2009 - 03:21 PM
Generally when a rotary compressor shows higher discharge temperature and also a lower flow, either there is a mechanical issue (rotor is dinged?) or there is an internal "recycle" of the compressed gas via some leak path you can't see, or there is an issue with capacity controls (usually a slide valve or a recycle valve leaking). Another possibility is something in the suction path causing a blockage and creating an effectively lower suction pressure inside the case.
Good luck tracking it down!
Marq
#7
Posted 09 January 2009 - 04:08 PM
Zauber:
I've held back on this topic on both this Forum and Eng-Tips, hoping someone would come up with the comment I would make. Marq has done that for me. I agree with what he has written.
My experience has shown that hardly any engineer can expect to purchase a "Dry" screw gas compressor and feel secure that it will run without any "slippage". The fact is, there is always slippage. I've known this from the very beginning when the screw design came out in the middle 1950s. The dry screw failed miserably as a competitive compressor then, when compared to the reciprocating models. The reason was not because of the engineering design. The weakness in the dry screw was (& still is, to some extent) the ultra-close machining and running tolerances required by the machine in order to avoid volumetric inefficiency and inherent & subsequent RECOMPRESSION - which reduces capacity and increases the discharge temperatures in each stage.
I am not surprised that David (although a very experienced mechanical engineer) has not mentioned that in Eng-Tips. He is a very experienced and capable mechanical engineer. But like most all engineers today, he has mainly worked with LUBRICATED screws (because of the inherent weaknesses of the dry screw) and has never had to take a screw compressor (especially a dry one) apart. David's experience, as I understand it, is not in operations. It is in design and installation. I have taken a dry screw apart in the past - and re-assembled it. I would never do it again. It isn't worth the effort and headaches. All screws are subject to ultra-special tooling and mechanical assembly experiences. That is the trade-off involved in selecting a screw machine. All screws should only be repaired/disassembled or modified by the original manufacturer - never outside of the supplier's control.
The tolerances in a dry screw have to be so precise and small that any bearing or main shaft wear (or deflection) will cause an abnormal alignment in the screws vis-a-vis themselves and the casing walls. A loss in capacity (due to slippage, mainly) and an increase in the discharge temperatures are the first indications of such internal problems.
The rotor mis-alignment is the worst horror. The next cause could be the capacity control slide valve adjustments and calibrations. Either way, it looks like a job for the manufacturer if the situation gets any worse.
That is the MAIN REASON WHY OIL-FLOODED SCREWS WERE INTRODUCED approximately 20-25 years ago and finally the screw was able to compete with the recip. Flooded screws do not require the "tight" and close tolerances required of dry screws. But then, the oil system takes on a more serious design and gas contamination becomes an issue. Everything has a trade-off.
I've held back on this topic on both this Forum and Eng-Tips, hoping someone would come up with the comment I would make. Marq has done that for me. I agree with what he has written.
My experience has shown that hardly any engineer can expect to purchase a "Dry" screw gas compressor and feel secure that it will run without any "slippage". The fact is, there is always slippage. I've known this from the very beginning when the screw design came out in the middle 1950s. The dry screw failed miserably as a competitive compressor then, when compared to the reciprocating models. The reason was not because of the engineering design. The weakness in the dry screw was (& still is, to some extent) the ultra-close machining and running tolerances required by the machine in order to avoid volumetric inefficiency and inherent & subsequent RECOMPRESSION - which reduces capacity and increases the discharge temperatures in each stage.
I am not surprised that David (although a very experienced mechanical engineer) has not mentioned that in Eng-Tips. He is a very experienced and capable mechanical engineer. But like most all engineers today, he has mainly worked with LUBRICATED screws (because of the inherent weaknesses of the dry screw) and has never had to take a screw compressor (especially a dry one) apart. David's experience, as I understand it, is not in operations. It is in design and installation. I have taken a dry screw apart in the past - and re-assembled it. I would never do it again. It isn't worth the effort and headaches. All screws are subject to ultra-special tooling and mechanical assembly experiences. That is the trade-off involved in selecting a screw machine. All screws should only be repaired/disassembled or modified by the original manufacturer - never outside of the supplier's control.
The tolerances in a dry screw have to be so precise and small that any bearing or main shaft wear (or deflection) will cause an abnormal alignment in the screws vis-a-vis themselves and the casing walls. A loss in capacity (due to slippage, mainly) and an increase in the discharge temperatures are the first indications of such internal problems.
The rotor mis-alignment is the worst horror. The next cause could be the capacity control slide valve adjustments and calibrations. Either way, it looks like a job for the manufacturer if the situation gets any worse.
That is the MAIN REASON WHY OIL-FLOODED SCREWS WERE INTRODUCED approximately 20-25 years ago and finally the screw was able to compete with the recip. Flooded screws do not require the "tight" and close tolerances required of dry screws. But then, the oil system takes on a more serious design and gas contamination becomes an issue. Everything has a trade-off.
#8
Posted 09 January 2009 - 10:11 PM
Dear/Respected Art
Splendid!
Now I exactly know the reasons of Air Compressor(Oil free type) frequent tripping on high temperature at my previos employer site.
Thanks& Best Regards
Qalander
#9
Posted 10 January 2009 - 01:09 PM
Hello Art/Marq,
Thank you for such a detailed explanation. I was digging through many textbooks these days (Bloch, Hanlon, etc.) in order to look for weak points of dry rotary screw machines; your experience concurs with what I have found, and even more, it gives such a clear picture of dry compressor design and operational issues. Thanks again to both of you.
When looking at compressor assembly (the sketch is attached below), I have eliminated the possibility of capacity control (recycle) valve leakage, since this line goes back to the suction after the interstage cooler (interstage temperature is OK). The only thing left could be a partial blockage of intercooler (process-side) or some other element between the 1st and the 2nd stage, or it is a mechanical issue (I sincerely hope it isn't; I remember these kinds of machines being fairly trouble-free in refineries/gas plants, when employed for air compression).
I hope there will be an opportunity to inspect the equipment soon; at the moment we need it in operation (lag mode) since our air demand has increased when running the plant at full rates. I will come back once when we find out the reason for excessive discharge temperature; at the moment, simply by cleaning the coolers from outside, the temperature has dropped by almost 10C but it is still way above the design value, and much higher than for the other compressor operating in lead mode.
Best regards,
Air_Compressor.JPG 90.23KB
69 downloads
Thank you for such a detailed explanation. I was digging through many textbooks these days (Bloch, Hanlon, etc.) in order to look for weak points of dry rotary screw machines; your experience concurs with what I have found, and even more, it gives such a clear picture of dry compressor design and operational issues. Thanks again to both of you.
When looking at compressor assembly (the sketch is attached below), I have eliminated the possibility of capacity control (recycle) valve leakage, since this line goes back to the suction after the interstage cooler (interstage temperature is OK). The only thing left could be a partial blockage of intercooler (process-side) or some other element between the 1st and the 2nd stage, or it is a mechanical issue (I sincerely hope it isn't; I remember these kinds of machines being fairly trouble-free in refineries/gas plants, when employed for air compression).
I hope there will be an opportunity to inspect the equipment soon; at the moment we need it in operation (lag mode) since our air demand has increased when running the plant at full rates. I will come back once when we find out the reason for excessive discharge temperature; at the moment, simply by cleaning the coolers from outside, the temperature has dropped by almost 10C but it is still way above the design value, and much higher than for the other compressor operating in lead mode.
Best regards,

#10
Posted 21 January 2009 - 12:27 PM
Art,
What happens if there is a leakage from 2nd stage discharge through the recycle valve seat, and then to the suction (and atmosphere - through the silencer; look at the sketch above)? How does this reflect on rotary screw machine capacity and discharge temperature? Suction temperature for both stages is normal and well within design specifications.
How does, in general, leakage from discharge to the atmosphere or suction affects screw compressor power and discharge temperature?
The machine operates in lag (backup) mode, with a discharge pressure setting 0.5bar lower than the lead compressor.
What happens if there is a leakage from 2nd stage discharge through the recycle valve seat, and then to the suction (and atmosphere - through the silencer; look at the sketch above)? How does this reflect on rotary screw machine capacity and discharge temperature? Suction temperature for both stages is normal and well within design specifications.
How does, in general, leakage from discharge to the atmosphere or suction affects screw compressor power and discharge temperature?
The machine operates in lag (backup) mode, with a discharge pressure setting 0.5bar lower than the lead compressor.
#11
Posted 09 February 2009 - 01:25 PM
Good evening,
I guess I'm quite aggressive with this topic, but I definitely need to clarify to myself what is all about - if something is wrong, or it has been designed from the day No.1; I am also approaching compressor vendor in order to get their feedback as well.
After the equipment cleaning has been completed (coolers, filters, moisture separators), I've gathered process trends for temperature and pressure across both compressors (operator log sheets, not linked to DCS) for the period between 19-Jan to 07-Feb 2009. The averaged data have been plugged into the very simple HYSYS model of compressor unit in order to estimate performance parameters, such are compressor efficiency, useful work, and other parameters. All the data are attached below. Compressor B is LEAD machine, Compressor A is in LAG mode. Both compressors are loaded.
PK_3502_Follow_up_on_performance_monitoring.doc 41.5KB
56 downloads
PK_3502_Data.xls 2.96MB
67 downloads
Flowsheet.JPG 70.34KB
43 downloads
Now, the questions which have arrived:
1. Why two identical compressors have different interstage pressures? What could be the cause of this?
2. Is it possible for machine A to have some internal leakage (recycle) which lowers the effective 1st stage discharge pressure, showing average efficiency to be higher than it actualy is? Somehow I don't believe in this difference in efficiencies in "A" machine, and it makes me think something else is going on there.
Art, you're the mastermind of gas compression. I'm waiting to hear your comments, and if you need some additional data, let me know. Other forum members, you are most welcome as well; sometimes even a non-expert person can bring interesting thoughts and ideas how to proceed further.
Thanks in advance,
I guess I'm quite aggressive with this topic, but I definitely need to clarify to myself what is all about - if something is wrong, or it has been designed from the day No.1; I am also approaching compressor vendor in order to get their feedback as well.
After the equipment cleaning has been completed (coolers, filters, moisture separators), I've gathered process trends for temperature and pressure across both compressors (operator log sheets, not linked to DCS) for the period between 19-Jan to 07-Feb 2009. The averaged data have been plugged into the very simple HYSYS model of compressor unit in order to estimate performance parameters, such are compressor efficiency, useful work, and other parameters. All the data are attached below. Compressor B is LEAD machine, Compressor A is in LAG mode. Both compressors are loaded.



Now, the questions which have arrived:
1. Why two identical compressors have different interstage pressures? What could be the cause of this?
2. Is it possible for machine A to have some internal leakage (recycle) which lowers the effective 1st stage discharge pressure, showing average efficiency to be higher than it actualy is? Somehow I don't believe in this difference in efficiencies in "A" machine, and it makes me think something else is going on there.
Art, you're the mastermind of gas compression. I'm waiting to hear your comments, and if you need some additional data, let me know. Other forum members, you are most welcome as well; sometimes even a non-expert person can bring interesting thoughts and ideas how to proceed further.
Thanks in advance,
#12
Posted 22 February 2009 - 02:45 AM
Dear sirs (Art and Z)
I am interested in this topic for two reasons:
1. I am presently deciding about purchase of an air compressor system for N2 production unit and we are discussing the cap/op cost benefits of oil-free vs oil-flooded as against doing away the dryer and filters before PSA.
2. I have been on the operation team handling both recip air comp and oil filled air compressors for an oil and gas plant as well on design teams for selection /purchase of air compressors.
Operation wise, intially the rotary looks nice (well packed, less noise and with modern gadgets all parameters are auto logged). over long run, recip is better for the reason it can run trouble free with regular inplant maintenance (rotary requires the vendor /mftr to be present and the units to be moved to the mftr shop!)
Oil-free sounds nice for a designer, but a horror for the operation guys esp once the unit starts giving trouble; as Z mentioned you can do all u can with cooler, separators, filters/screens, silencers but u cannot touch the machine; essentially they are just matching / mismatching screws and the operators feel screwed (only pun intended). With no oil seal to prevent the slippage of air along the screw, they (oil-free) tend to lose the capacity and show a trend of increase in discharge temperature. (even your B machine would be showing an increasing temp trend albeit slow)
We don't have data of the string test or FAT results for these compressors to know if they were exactly same during the 72 hour run test (if one such was conducted) either at shop or at site. The models are same (no doubt) but the actual mechanics would be different.
Now, coming to the operating data of the machines in hand, from the diagram, the ist stage discharge pressure is not the screw outlet pressure (typically a pressure probe can be placed there at a plug near the temp sensor to see the actual performance) but essentially the after cooler pressure or the second stag suction. for machine B, i expect a slightly higher temperature for the second stage discharge, which is true as the 2nd stage suction pressure is less than machine A but discharge is common for both compressors. Thus second stage compression ratio is more.
the first stage performance of the screw A itself is apparently less as the discharge temperature is less compared to the machine B. I donot suspect serious slippage of air along the screw as otherwise the temperature would be higher. The conclusion is the first stage is loaded less and the temperature is less for machine A.
I presume overall pressure control for the system would be from a common vessel. For the given speed the second stage screw of machine A is capable of a higher compression and this forces the discharge requirement of the first stage. As we dont have individual capacity loops, the machine sees a overall suction and discharge; and the intermediate pressure depends on the compression profile of the 2nd set of screw. you cannot force the machine to have a higher 1st stage discharge pressure as the screw profiles decide the performance. this can be brought out by FAT test.
The above may sound odd; but because the second set is CAPABLE of higher compression ratio, the temperature is more! and the unfortunate thing is this is how the machine is now.
Coming back to my experience of operation, whenever the mftr is called for mainteance, the screw bending (yes they happen), edge deformation and any visible dents/scrapes are all blamed on operation and rebuilding or replacing is what is offered! we went to the extent of leasing an air compressor operation from the mftr (it is his outlook for the machine performance, maintenance. shift personnel etc), but the cotnract is to supply air of the required quality/quantity to be available. This was done for our LPG2 plant for almost three years and ran well .
regards
neelakantan
I am interested in this topic for two reasons:
1. I am presently deciding about purchase of an air compressor system for N2 production unit and we are discussing the cap/op cost benefits of oil-free vs oil-flooded as against doing away the dryer and filters before PSA.
2. I have been on the operation team handling both recip air comp and oil filled air compressors for an oil and gas plant as well on design teams for selection /purchase of air compressors.
Operation wise, intially the rotary looks nice (well packed, less noise and with modern gadgets all parameters are auto logged). over long run, recip is better for the reason it can run trouble free with regular inplant maintenance (rotary requires the vendor /mftr to be present and the units to be moved to the mftr shop!)
Oil-free sounds nice for a designer, but a horror for the operation guys esp once the unit starts giving trouble; as Z mentioned you can do all u can with cooler, separators, filters/screens, silencers but u cannot touch the machine; essentially they are just matching / mismatching screws and the operators feel screwed (only pun intended). With no oil seal to prevent the slippage of air along the screw, they (oil-free) tend to lose the capacity and show a trend of increase in discharge temperature. (even your B machine would be showing an increasing temp trend albeit slow)
We don't have data of the string test or FAT results for these compressors to know if they were exactly same during the 72 hour run test (if one such was conducted) either at shop or at site. The models are same (no doubt) but the actual mechanics would be different.
Now, coming to the operating data of the machines in hand, from the diagram, the ist stage discharge pressure is not the screw outlet pressure (typically a pressure probe can be placed there at a plug near the temp sensor to see the actual performance) but essentially the after cooler pressure or the second stag suction. for machine B, i expect a slightly higher temperature for the second stage discharge, which is true as the 2nd stage suction pressure is less than machine A but discharge is common for both compressors. Thus second stage compression ratio is more.
the first stage performance of the screw A itself is apparently less as the discharge temperature is less compared to the machine B. I donot suspect serious slippage of air along the screw as otherwise the temperature would be higher. The conclusion is the first stage is loaded less and the temperature is less for machine A.
I presume overall pressure control for the system would be from a common vessel. For the given speed the second stage screw of machine A is capable of a higher compression and this forces the discharge requirement of the first stage. As we dont have individual capacity loops, the machine sees a overall suction and discharge; and the intermediate pressure depends on the compression profile of the 2nd set of screw. you cannot force the machine to have a higher 1st stage discharge pressure as the screw profiles decide the performance. this can be brought out by FAT test.
The above may sound odd; but because the second set is CAPABLE of higher compression ratio, the temperature is more! and the unfortunate thing is this is how the machine is now.
Coming back to my experience of operation, whenever the mftr is called for mainteance, the screw bending (yes they happen), edge deformation and any visible dents/scrapes are all blamed on operation and rebuilding or replacing is what is offered! we went to the extent of leasing an air compressor operation from the mftr (it is his outlook for the machine performance, maintenance. shift personnel etc), but the cotnract is to supply air of the required quality/quantity to be available. This was done for our LPG2 plant for almost three years and ran well .
regards
neelakantan
Similar Topics
![]() Hysys Expander/compressor Input Using Dimensionless CurveStarted by Guest_Alfreedo_* , 21 Apr 2025 |
|
![]() |
||
Inlet Line Not Free DrainingStarted by Guest_Asifdcet_* , 07 Apr 2025 |
|
![]() |
||
Centriugal CompressorStarted by Guest_Rahimzadeh_* , 02 Mar 2025 |
|
![]() |
||
Pulsation Device In Reciprocating CompressorStarted by Guest_zaidanamir_* , 17 Feb 2025 |
|
![]() |
||
Recip Compressor Discharge PrvsStarted by Guest_go-fish_* , 15 Oct 2022 |
|
![]() |