|
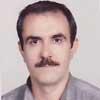
Criteria For Setting Pressures On Cooling Water Network
Started by fallah, May 21 2009 09:55 AM
13 replies to this topic
Share this topic:
#1
Posted 21 May 2009 - 09:55 AM
Dears,
I want to know the criteria (if any) may existed behind setting the min/normal/max pressure of cooling water input in users battery limits in a cooling water network.
As an example, the above mentioned pressures in basic design of a plant have been determined as 2.7/4.6/6.0 barg.
Any input would be highly appreciated
I want to know the criteria (if any) may existed behind setting the min/normal/max pressure of cooling water input in users battery limits in a cooling water network.
As an example, the above mentioned pressures in basic design of a plant have been determined as 2.7/4.6/6.0 barg.
Any input would be highly appreciated
#2
Posted 21 May 2009 - 10:11 AM
Fallah,
In my opinion the maximum pressure value (6.0 barg) should be based on the maximum operating pressure for the cooling water end user nearest and lowest (static head) from the defined battery limit whereas the minimum pressure value (2.7 barg) should be based on the minimum operating pressure required for the cooling water end user for the furthest & highest (static head) from the defined battery limit. This would serve as defining the operating pressure envelope for your cooling water.
This is the approach I have followed earlier for defining the CW operating envelope.
Hope this helps.
Regards,
Ankur.
#3
Posted 21 May 2009 - 11:05 AM
Ankur,
Thanks for your fast reply,but:
1-What about 4.6 barg at normal condition?
2-What is the procedure of calculation to approach to the value of 2.7 barg (or 4.6 barg,6 barg)?
As an additional information,the users are located in different levels (heights) of plant and the corresponding pressures at producer battery limit (min/normal/max) are 6 barg/7 barg/8 barg.
Thanks again
Thanks for your fast reply,but:
1-What about 4.6 barg at normal condition?
2-What is the procedure of calculation to approach to the value of 2.7 barg (or 4.6 barg,6 barg)?
As an additional information,the users are located in different levels (heights) of plant and the corresponding pressures at producer battery limit (min/normal/max) are 6 barg/7 barg/8 barg.
Thanks again
#4
Posted 21 May 2009 - 12:31 PM
Fallah,
Pointwise reply is as follows:
1. 4.6 barg can be an average value of the minimum and maximum pressure values.
2. Consider an example:
Heat Exchanger with Cooling Water on tube side. If minimum CW pressure for the HE tube side is specified as 1.5 barg and the static head measured from the CW inlet nozzle to the battery limit point is 10 m as well as the dynamic friction loss is say 0.2 bar then your minimum battery limit pressure gets automatically fixed as:
1.5 + 1.0 +0.2 = 2.7 barg
Essentially you need to do a CW network analysis for your plant with following inputs:
a. Min./Max. CW pressures for all your CW consumers
b. Static heads of all CW consumers from your reference battery limit point
c. Approximate pipe lengths/sizes of your CW consumers from reference battery limit point to get an idea of dynamic pressure losses. It is possible to ignore this if line lengths are very small and it is ascertained that dynamic pressure losses are going to be negligible.
Additionally after doing a network analysis and arriving at some battery limit pressure data I would put some margin (say 15-20%) on the calculated figures just in order to ensure a safety margin due to unexpected changes in equipment layout and/or piping routing.
Hope this helps.
Regards,
Ankur.
#5
Posted 21 May 2009 - 10:34 PM
Ankur,
Thanks again,but:
1-How has the minimum (or maximum) CW pressure for the HE tube side been specified?
The temperature of the inlet cooling water is 30 C and the outlet 40 C (in all heat exchangers).
2-There is no static head from the CW inlet nozzle to the battery limit point (CW pipes on sleeper) and pressures of 2.7 barg/4.6 barg/6.0 barg (as min/normal/max on B.L.) would be considered upstream of manually regulating valves inside B.L. and before heat exchangers.
I just think we must have sufficient pressure available on B.L. so that we can adjust the regulating valves and balance the flows to all the exchangers. Also higher the pressure of cooling water results in higher heat transfer rate.
Regards
#6
Posted 22 May 2009 - 04:09 AM
Fallah,
It is hard to believe that the CW consumers (heat exchangers) do not have operating (inlet) pressure specified in their data sheets. This data is essential, otherwise how do you specify the CW design pressure? Also, when designing the HE, the maximum allowable delta P for the CW side would be fixed based on the available inlet pressure of the CW. Hence, I cannot think of a HE without the fluid inlet conditions on both sides (shell & tube) such as pressure & temperature being specified.
Heat transfer rate is a function of the heat transfer coefficient which, in turn, is a function of the turbulence (read velocity). Higher the velocity, higher will be the heat transfer. However, the higher velocity translates into higher pressure drop. So, the HE design needs to optimize the velocity and pressure drop. The CW pressure has no direct contribution as such to the heat transfer rate on the cold side.
If in your case static head is not a factor at all, then only the dynamic pressure loss will play a role in determining the B.L pressure which will also include the maximum allowable delta P across the heat exchanger on the CW side as specified in the HE data sheet.
Regards,
Ankur.
#7
Posted 04 June 2009 - 08:00 AM
Attached you will find a schematic diagram of the closed loop cooling water system based on what I have started in this this thread.
Three users are taking 30 C cooling water and the outlet would be 40 C.
Pressure drop in each user is around 0.7 bar
A (elevation) = 0.5 m
E (elevation) = 13 m
F (elevation) = 27 m
Pump discharge pressure = around 11 barg
Normal level of water in expansion tank (with respect to pump suction cehterline) = 3 m
Pressure drop in supply line = pressure drop in return line = 1.5 bar
If LPP (low pressure point) would have pressure equal to around 2 barg, what would be the set point of the PCV adjusting the N2 blanketing in the expansion tank installed in pump suction?
I think it would be around 3.7 barg. Please correct me if it is wrong.
Also, and veiwpoints about pressure balance and other relevant issues in the system would be highly appreciated.
Attached Files
#8
Posted 04 June 2009 - 12:24 PM
Dear Fallah,
From the excel sheet you have furnished and from the data given for LPP of 2 barg, this is how my calculation goes:
Pump Suction Pressure = 2 + ((0.5+13+27)*1/10.2)-1.5 = 4.47 barg
However what surprises me is that your expansion tank is at a lower elevation than the consumer III as shown in the excel sheet. My concept of an expansion tank is that it should be at a higher elevation than the highest elevation consumer. Is there an error in the representation of the expansion tank in the excel sheet? Can you please verify the location of the expansion tank? To me, the location (elevation) of the expansion tank in the sketch does not seem right.
Regards,
Ankur.
#9
Posted 05 June 2009 - 01:32 AM
Dear Ankur,
Theoretically you are right for the location of the expantion tank, because locating the tank in the level higher than highest elevation consumer would lead to lowest gauge pressure (when the pump is on) and smallest tank size. But for the system that is distributed vertically (such as the system is being discussed) the best location may not be the one that result in the smallest tank size (i.e. LPP).
Nowadays, for system not vented to the atmosphere, it is not uncommon to locate the expansion tank near the pump suction where the water entering the pump after passing all exchanger is being in the highest temperature and could be fully deaerated and its thermal expansion is to be damped in the tank. Also, the space would be available and the tank is readily accessible for maintenance and service. Of course, the tank in this situation would be pressurized and should have higher design pressure and also blanketed with relatively high source of N2.
Considering the above, please submit your viewpoints about the set point of PCV in expansion tank and other issues in this regard.
Best Wishes
#10
Posted 05 June 2009 - 07:39 PM
I tend to comment on how minimum pressure being defined, as discussed before, minimum pressure is determined based on hydraulic calculation which result in pressure required to flow all the cooling water for all consumers.
About high pressure setting, I believe we can go as high as we can as long as not exceed the lowest MAWP of equipment along the cooling water network. But, as a client, I would not put that high setting, due to wasted money for something that not critically needed.
The bottomline : determining setting pressure is based on reliability and economic justification.
For the expansion tank, I believe that the pressure setting is only required to maintain suction pressure to avoid cavitation due changes in water level. Consider the tag name is a "Tank", which the pressure can not be more than 1-2 bar(g)
About high pressure setting, I believe we can go as high as we can as long as not exceed the lowest MAWP of equipment along the cooling water network. But, as a client, I would not put that high setting, due to wasted money for something that not critically needed.
The bottomline : determining setting pressure is based on reliability and economic justification.
For the expansion tank, I believe that the pressure setting is only required to maintain suction pressure to avoid cavitation due changes in water level. Consider the tag name is a "Tank", which the pressure can not be more than 1-2 bar(g)
#11
Posted 05 June 2009 - 09:46 PM
Fallah,
This is not specific to your question, but given that you have raised the issue of operating pressures in cooling water systems, I would like to highlight one important point which is often missed out while designing cooling water circuits.
Pressure at the inlet of any CW consumer must be adequate to take care of all the hydraulic losses in its branch/sub-branches including any pressure drop across say control valves or the equipment itself. Having said that, there would be some equipments based on the equipment layout that require minimal pressure and there would be some requiring higher pressures dictate what the CW supply pressure should be. While selecting the CW distribution design, what is commonly missed out is other than the pressure requirements, what is the flow rate requirements of each consumer. Remember, for the CW pump differential head selection of say 60 m, if there are are consumers that require less inlet pressure that really requires head in the order of say 25 m; but have very high flow rates, it is wise to separate; if possible; their distribution circuit because the energy you end up consuming due to dropping the pressure which is often selected based on the highest pressure requirement in the entire system can be dangerously high. If one were to segregate the pumps and distribution system of such low pressure (but potentially high flow rate) consumers, it will surely add to some piping hardware and pumps themselves, but it is worth at times depending on what the numbers involved are.
To make it short, it is often necessary essential to study the flow rate pattern in tandem with the pressure requirement.
This is not specific to your question, but given that you have raised the issue of operating pressures in cooling water systems, I would like to highlight one important point which is often missed out while designing cooling water circuits.
Pressure at the inlet of any CW consumer must be adequate to take care of all the hydraulic losses in its branch/sub-branches including any pressure drop across say control valves or the equipment itself. Having said that, there would be some equipments based on the equipment layout that require minimal pressure and there would be some requiring higher pressures dictate what the CW supply pressure should be. While selecting the CW distribution design, what is commonly missed out is other than the pressure requirements, what is the flow rate requirements of each consumer. Remember, for the CW pump differential head selection of say 60 m, if there are are consumers that require less inlet pressure that really requires head in the order of say 25 m; but have very high flow rates, it is wise to separate; if possible; their distribution circuit because the energy you end up consuming due to dropping the pressure which is often selected based on the highest pressure requirement in the entire system can be dangerously high. If one were to segregate the pumps and distribution system of such low pressure (but potentially high flow rate) consumers, it will surely add to some piping hardware and pumps themselves, but it is worth at times depending on what the numbers involved are.
To make it short, it is often necessary essential to study the flow rate pattern in tandem with the pressure requirement.
#12
Posted 05 June 2009 - 10:44 PM
Usually, CW header pressure is 7 barG or 100 psiG. Even at the end of the CW loop, pressure does not drop to below 5 barG. If the exchanger is not designed for this pressure, the pressure is killed as required. What's more important is that, CW velocity, for effective heat transfer, is usually limited to 3-3.5m/s.
#13
Posted 05 June 2009 - 11:33 PM
QUOTE (akslzf @ Jun 5 2009, 10:44 PM) <{POST_SNAPBACK}>
Usually, CW header pressure is 7 barG or 100 psiG. Even at the end of the CW loop, pressure does not drop to below 5 barG.
This is for horizontally distributed network.Our case is vertically distribution.
#14
Posted 07 June 2009 - 10:27 PM
@fallah:
At the moment, no one except you know the details. Many of respondents, including me, to your thread have\might have done this work before so previous experiences are being shared with you and you should NOT take that as final wordings for your system as you are the one to set design basis for this specific work.
I suggest you have answers for below questions before you go with setting pressures:
1. What is the req. inlet pressure at each consumer?
2. What is the Delta T required at CW side of each consumer? (This would help you to calculate the flow rate).
Once you have these things, you should:
a. Calculate the pump discharge pressure based on hydraulic calculations that give you item '1' above for each consumer.
b. Based on this, you will have to OR your client will have to decide if you want to use single CWS for all three consumers or need to change the strategy. This could be based on how Rajesh defined earlier in his reply (Don't want to write all that and make it a big, unreadable reply).
For Cooling Water Return (CWR) header, you need to know:
1. The pressure at which expansion tank is being maintained and its design pressure, MAWP.
2. Max and Min DeltaP for CWS of each consumer.
3. Velocity of water at Tube side of Shell & Tube HX is normally maintained at 3 m/sec... 3.5m/sec is a higher estimate. But again, it depends on how much Delta P and Delta T is desired (Min and Max values).
Once you have these things, it is matter of simple hydraulic calculations to set values.
At the moment, no one except you know the details. Many of respondents, including me, to your thread have\might have done this work before so previous experiences are being shared with you and you should NOT take that as final wordings for your system as you are the one to set design basis for this specific work.
I suggest you have answers for below questions before you go with setting pressures:
1. What is the req. inlet pressure at each consumer?
2. What is the Delta T required at CW side of each consumer? (This would help you to calculate the flow rate).
Once you have these things, you should:
a. Calculate the pump discharge pressure based on hydraulic calculations that give you item '1' above for each consumer.
b. Based on this, you will have to OR your client will have to decide if you want to use single CWS for all three consumers or need to change the strategy. This could be based on how Rajesh defined earlier in his reply (Don't want to write all that and make it a big, unreadable reply).
For Cooling Water Return (CWR) header, you need to know:
1. The pressure at which expansion tank is being maintained and its design pressure, MAWP.
2. Max and Min DeltaP for CWS of each consumer.
3. Velocity of water at Tube side of Shell & Tube HX is normally maintained at 3 m/sec... 3.5m/sec is a higher estimate. But again, it depends on how much Delta P and Delta T is desired (Min and Max values).
Once you have these things, it is matter of simple hydraulic calculations to set values.
Similar Topics
Water Hammer Study: Hysys Dynamics Vs PipenetStarted by Guest_powerox29_* , 07 Apr 2025 |
|
![]() |
||
![]() Steam Carrying Liquid From The Sour Water Stripping TowerStarted by Guest_kaidlut_* , 12 Sep 2024 |
|
![]() |
||
Water TreatmentStarted by Guest_not_mikhail_* , 01 Apr 2025 |
|
![]() |
||
![]() Transfer Water By Gravity - Maximum Velocity CriteriaStarted by Guest_56200358_* , 05 Mar 2025 |
|
![]() |
||
![]() Heat Exchanger Network DesignStarted by Guest_Kakashi-01_* , 21 Feb 2025 |
|
![]() |