|
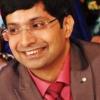
Pressure Drop In Swing Check Valve
#1
Posted 12 November 2009 - 11:31 AM
I have checked various charts and correlation for pressure drop in swing Check Valves but still i have a doubt.
suppose Initially , the valve is closed and there is no flow in line ,gradually flow starts building up and pressure increases and then the check valve is lifted and flow is established further in the line.
What Initial pressure is required for this check valve to lift and whats the drop while the check valve is lifted .I assume that P drop provided by correlation are once the flow is established through the line but what if there is not enough pressure in line to even lift the check valve !!!
#2
Posted 15 November 2009 - 04:40 AM
What correlations have you used, and what confuses you?
Here's one table from Cameron Databook that might be of some help.
Attached Files
#3
Posted 17 November 2009 - 05:48 PM
I believe the differential pressure required for establishing the flow through check valve is negligible. Can someone propose a different view? That could be an interesting discussion...
Wish granted. This is an excellent question and is one of the many "traps" an inexperienced process engineer may "fall for". We tend to go to Crane or a similar reference to get a value for L/D or K and to apply the tabular values indiscriminately in our hydraulic calcs. Often and especially for higher pressure systems, the calculational procedures are forgiving and allow us to get away with this approach. Then we tend to think of a check valve just like a block valve, elbow, or other "static" pipe fitting. In fact, a check valve has a MUCH higher resistance to flow than you might expect unless or until it is fully opened. Be aware of this fact and I would caution you to NEVER use a check valve in vacuum or low pressure service unless you can adequately consider this phenomenum. I tend to think of a check valve as requiring something like 2 to 4 psid (0.14 - 0.28 bard) to lift the disk. If you have allowed for more than that pressure drop through the check valve, then go ahead and switch over to the appropriate L/D or K value and continue with your hydraulic calcs. If you have less than that, then the disk has not fully lifted, and the valve will take much more pressure drop than you expect. Even low dP check valves need about 2 psid to fully lift, and that sort of loss cannot be tolerated in low pressure systems. So, check or non-return valves are great in pumped water services, but be very cautious about using them in low pressure applications.
#4
Posted 18 November 2009 - 05:19 AM
Indeed this is a very interesting topic & here I would like to share an interesting commissioning experience related to a check valve. Here it goes:
We were commissioning a spent ethylene glycol recovery system from a polyester plant which included two distillation columns in series with the column bottom of the first column pumped as feed to the second column. I was part of the team from the design consultant. A team leader was appointed who had worked on the system design as the design lead in the engineering office. Unfortunately, this was the first commissioning assignment for the team leader & since he had been involved in the design stage he considered it as his own baby. I was a last minute entry in the team because of my commisssioning/operations background & looked upon with a certain amount of contempt because of my very limited design experience.
The problem that we were facing was that we were not able to pump the 1st column bottom to the second column as feed. The pumping circuit had the usual Flow control loop & nothing was pumping was obvious from the flow meter not registering any reading. My team leader wanted to keep things under his control & was trying to troubleshoot on his own. Totallyexasperated after trying for a few hours, he called the whole team & declared that the wrong impeller had been fixed in the pump casing & no head was being built up in the pump & we should tell the client that the pump is just not pumping. I was not convinced about the pump being at fault after doing some of my own observations & advised the team leader not to discuss the matter with the client till we were 100% sure. It just so happened that my advise was not taken kindly & the pump being wrongly selected was reported to the client. The whole thing backfired when the client cooly informed that your own people had inspected the pump at the manufacturers shop before it was shipped. Imagine the red faces.
Meanwhile, I just could not digest the fact that the pump was faulty & decided to go through the system again with a tooth pick. Starting again from the suction line I repeated the process of checking the suction strainer/screen, checking for an inadvertent blind gasket, checking for some kind of obstruction in the pump casing or improper impeller clearance. Nothing, things were as they should have been.
Started working down the discharge side to check for blockages, blind gaskets, weld spatters in the check valve & found nothing to cause alarm. Had a very careful look at the check valve & did not find anything to be of concern. Boxed up the system and started the pump again, & there I was back to square one: "No Flow". Now I was getting disturbed because of lack of any progress. The technician who was working with me suddenly made a remark saying that the pump is also not working and the discharge pressure gauge is also faulty. I asked him why & he said that it is showing pressure when the pump is running & if there is no flow it shouldn't be showing any pressure. This aroused my curiosity & I asked him to vent the discharge pipe piece up to the check valve. As soon as we vented, the pressure gauge which was upstream of the check valve ran down to zero. I told the technician that his presumption of the gage being faulty was not correct.
This action also gave me an idea & I asked the technician to start the pump with the discharge side completely boxed up to the destination. When the pump started, the pressure gage immediately moved up & deadheaded at a particular point but the flowmeter which was further downstream was not reading. Everything was now coming clear to my mind. We stopped the pump & dismantled the check valve (a lift check valve). Just by instinct I kept the plug lift of the check valve in my palm & I knew what was wrong. I called the plant manager & asked him that I wanted to run the pump without the check valve installed & there was a small element of risk of reverse flow which could cause the impeller to unscrew. By this time, no one was in any mood to argue & I was granted my wish. The pump started and the flowmeter went out of range. The culprit had been nailed & we could move forward with our further commissioning activities including providing the correct check valve for the pump. Wow! That was one hell of a experience with a check valve.
Guys, I hope I have been able to share something important with you.
Regards,
Ankur.
#5
Posted 18 November 2009 - 06:56 AM
For calculating pressure drop while lifting of swing check plate of check valve we have take help from mechanical data of check valve as per my vision of thinking.
Take basic energy equation:
Energy required to lif the check = pressure energy loss by fluid.
Energy required to lif the check = Torque X Displacemet =(Pressure x dia)X (2*90 angle/dia)
Torque = Pressure x length of check valve =Pressure x dia of pipe, as dia. of check valve = pipe dia
Displacemet = angle traced/raduis = 90*2/dia.
Please this equation is as per basic engg analysis if some component is mising in consideration please comment.
Regards
SAM
#6
Posted 19 November 2009 - 08:50 AM
@djack:This is the answer i was looking for !

well you have tempted me to ask one more query i am appending it at the end of my reply..
@Ankur:whoa ,Great Job..Kudos.

During Checklisting i have seen NRVs in opposite direction of flow !!!
hey ,i need one help please explain how you could sense this "Just by instinct I kept the plug lift of the check valve in my palm & I knew what was wrong."
@Makroo : That was revising the old Physics Fundas..But remember the postulate of 'Dynamic Equilibrium'

So one more related Problem
We have a system where there is a low pressure Dosing (Chemical agent diluted in HC) vessel operating at a pressure of about 0.5 Kg/cm2 g .This vessel is blanketed with nitrogen (with Pressure Control Valve) and as typical in case of overpressure we have control valve(split range to nitrogen control valve) to flare.Design pressure of this vessel is low about 1.5 Kg/cm2 and we would like Control valve to open at 1 Kg/cm2 g operating pressure and relieve the system.
I was thinking of a scenario where Flare Header Back pressure is about 1.2 Kg/cm2 g (typical flare header operating range 0.1-1.7 kg/cm2 g ),in this case HCs from flare (reverse flow from header to vessel)will pressurize the system instead of relieving it !

in case we put a NRV to prevent Backflow we will have problem of lifting of NRV at Low Pressure in the vessel.what should be done here ???

Also ,while writing this it just struck my mind that i have seen NRVs on Flare subheaders joining to Flare Main header ,is it a wise decision???

#7
Posted 20 November 2009 - 07:19 AM
A lot of trouble shooting in the field is done on a hit-&-trial basis & on instinct. But even for this you need to have experience and a feel for it. This feel or instinct gets developed like that of a rookie detective getting promoted in the police ranks as his detection skills increase with time & experience.
When I held the plug of the lift check valve in my palm, the damn thing felt heavy & it struck to me that the inertia of the plug is too large to overcome the kinetics of the flow.
As far as your question of providing a NRV on the subheader connecting the main flare header, some company standards strongly discourage it. Instead, a complete individual relief valve discharge, sub-header & main header study is undertaken to arrive at the back-pressures at the individual relief valves in a relief network & then based on this the selection of the type of relief valve is done, such as conventional, balanced-bellows & pilot-operated. Another important aspect during relief/flare study is how many contigencies are you considering to happen simultaneously. By elimination of cases called as 'Double Jeopardy' in engineering parlance you try to reduce the number of relief/flare contigencies happening simultaneously. This prevents gross oversizing of flare/relief systems, which could be impractical & expensive.
Hope this helps.
Regards,
Ankur.
#8
Posted 19 August 2010 - 05:27 PM
If we imagine the plates just open - increasing the flow would initially see a pressure drop as the plates open completely and a fully developed flow regime is allowed to develop. Increasing flow further would - as expected - see pressure drop increasing.
Pressure drop can indeed be considerable across a check valve. Often a process engineer pays no heed to the design, although I have seen DP's of 0.5 bar+
#9
Posted 23 August 2010 - 05:56 PM
Himanshu,I understand that this will be dependent on type and manufacturer of valve but still a generalized approximate values will be of great use for 'Learning' engineers like me.
First my appologies in not getting back to you sooner. I was "off-line" for several months, and this thread got buried until Poosticks reopened it. I'm not sure if you're aware of how I feel about so-called "rules of thumb", but they are grossly overrated. Anyway, I'll try to fill your request and hope you know not to take any rules of thumb too seriously.
Easiest comment is to say that a check valve will often not be fully open until the velocity through it is >= 3 ft/sec or 1 m/sec. That's what I'd most recommend as a "rough rule". In terms of pressure drop, about 2 to 3 psid or say 0.2 bard would probably do it for low dP check valves. All this is very, very rough and is highly dependent on many things such as fluid phase, density, viscosity, valve orientation, and many other factors. You've assured me that you are aware that these devices have characteristics that "vary all over the map", so I expect you to keep that in mind. (Is it obvious that I have taught classes for a period of time?)
When you get further down your last post, I really start to worry. You may not discharge the PSV from a vessel designed for 1.5 kg/cm^2 into a flare header that could sometimes be at 1.7 kg/cm^2. Notice that I did not say "usually", "maybe", or anything else half-hearted. This is a case of "Thou shall not".
No, it is not a wise decision. Others may disagree, but I would NEVER put a NRV in a flare line.Also ,while writing this it just struck my mind that i have seen NRVs on Flare subheaders joining to Flare Main header ,is it a wise decision???
#10
Posted 01 September 2010 - 08:06 AM
I appreciate your reply on the topic,atleast there is some vague idea or a numerical value !
can we safely say that initially pressure drop while NRV opening/lifting would be more as compared with once flow is fully established.
#11
Posted 08 September 2010 - 05:49 PM
yes, this is a true statement.can we safely say that initially pressure drop while NRV opening/lifting would be more as compared with once flow is fully established.
Similar Topics
Steam Pressure In Heat ExchangerStarted by Guest_mvanrijnbach_* , 15 Apr 2025 |
|
![]() |
||
Check Valve FailureStarted by Guest_Falah_* , 26 Mar 2025 |
|
![]() |
||
Multiport Selector Valve (Msv)Started by Guest__1angelia23_* , 12 Mar 2025 |
|
![]() |
||
![]() Valve Cavity - Pressure Relief ValveStarted by Guest_CS10_* , 20 Feb 2025 |
|
![]() |
||
Pressure Of An Isolated Flow In PipeStarted by Guest_phoroogh_* , 30 Jan 2025 |
|
![]() |